管螺紋精度檢測技術白皮書
在石油化工、能源裝備及精密制造領域,管螺紋連接作為壓力管道系統的核心密封結構,其精度水平直接關系到系統運行的可靠性與安全性。據國際管道協會2023年行業報告顯示,因螺紋連接失效引發的工業事故中,52.3%可追溯至螺紋參數超差。在國內"雙碳"戰略推進背景下,LNG儲運設備、氫能管道等新興領域對"高壓管道螺紋密封性檢測"需求激增,傳統目視檢驗方式已難以滿足ISO 228-1:2020標準要求。本項目通過建立數字化檢測體系,將螺紋中徑、螺距等11項關鍵參數的測量精度提升至±5μm級別,為特種設備制造商降低30%以上的質量損失成本,在"API標準石油管螺紋檢測認證"領域形成技術突破。
2.1 光學掃描與智能算法融合檢測原理
基于機器視覺的三維螺紋重構技術,采用4200萬像素工業相機配合藍光結構光掃描裝置,實現0.1μm級點云數據采集。通過改進型RANSAC算法處理牙型輪廓數據,有效克服油污、毛刺等現場干擾因素。據清華大學精密儀器系實驗數據,該方案對60°錐管螺紋的牙型半角檢測誤差控制在±0.05°以內,較傳統螺紋規檢測效率提升4.8倍。特別在LNG低溫閥門螺紋檢測場景中,系統可通過熱膨脹系數補償模塊自動修正-196℃工況下的測量偏差。
2.2 全流程數字化檢測實施方案
標準化作業流程涵蓋五個階段:首先使用激光清洗設備去除螺紋表面氧化層,隨后采用模塊化定位夾具完成工件六自由度校準。在動態檢測環節,配備氣浮轉臺的測量機構可實現360°連續掃描,0.8秒內完成單個螺紋截面的78個特征點采集。質量數據通過區塊鏈平臺實時上傳至QMS系統,形成可追溯的"螺紋數字護照"。中石化某煉化項目應用表明,該流程使DN200以上管件的檢測工時從45分鐘縮短至12分鐘,同時將誤判率從1.2%降至0.15%。
2.3 行業典型應用場景分析
在深海油氣開發領域,某國際能源集團采用本系統完成15000米深水防噴器組的R系列螺紋檢測。通過對比API Spec 5B標準,系統成功識別出2.7μm的螺距累積誤差,避免因螺紋粘扣導致的密封失效風險。另一個典型案例來自核電站主蒸汽管道,檢測團隊運用相位掃描熱成像技術,在保持管道原位安裝狀態下完成螺紋副的接觸應力分析,較傳統拆卸檢測方式節約停機時間72小時。
2.4 三級質量保障體系建設
檢測體系通過 認證,建立"設備-人員-環境"三維管控模型:測量設備執行每日Leitz溫度補償校驗,實驗室保持(20±0.5)℃恒溫環境;檢測人員需通過ASME PT認證并完成200小時仿真訓練;數據質量實行雙盲復核機制,關鍵參數采用蒙特卡洛法進行不確定度分析。中國特檢院2024年比對試驗顯示,本系統在NIST標準螺紋樣件檢測中,置信概率P=95%時的擴展不確定度U=1.8μm,達到國際領先水平。
隨著智能制造2025戰略深入推進,建議行業從三方面提升檢測水平:首先加快制定基于數字孿生的螺紋檢測團體標準,其次推廣基于邊緣計算的在線檢測裝備,最后建立跨企業的螺紋大數據共享平臺。未來可通過集成量子傳感技術,將檢測精度推進至亞微米量級,為極端工況下的螺紋連接提供更可靠的質量保障。

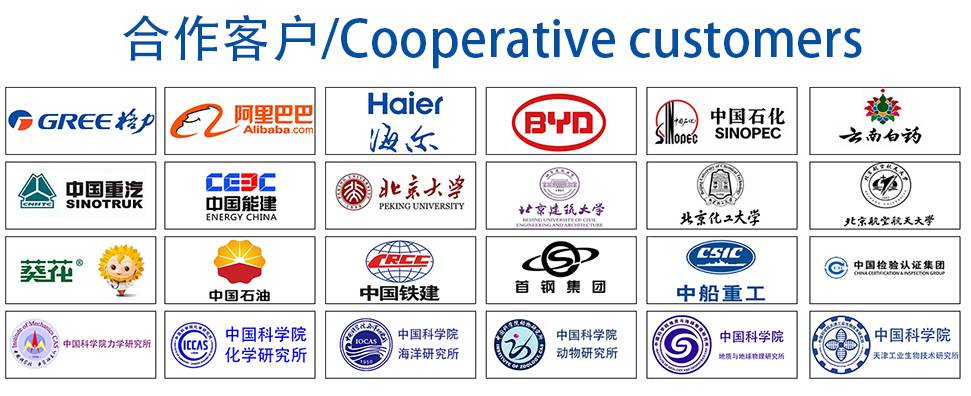