# 密封測試檢測的技術發展與行業應用白皮書
## 行業背景與核心價值
在高端裝備制造、新能源汽車及航空航天領域,密封性能已成為衡量產品質量的關鍵指標。據中國機械工程學會2024年行業報告顯示,我國每年因密封失效導致的工業事故損失超120億元,其中38%發生在壓力容器領域。密封測試檢測通過驗證結構件在極端工況下的密閉性能,直接關系到設備安全運行與環境保護,特別是在氫能源儲運裝置、鋰電池Pack系統等新興產業中,其技術價值更為凸顯。本項目建立了覆蓋-196℃至650℃溫域、0.1Pa至50MPa壓差的檢測體系,解決了傳統方法無法模擬真實工況的行業痛點,助力企業將產品故障率降低至百萬分之五以下。
## 技術原理與創新突破
### 多物理場耦合檢測技術
基于流體力學與固體力學耦合模型,系統整合了氦質譜檢漏、壓力衰減法及示蹤氣體法三大核心技術。其中差分式氦檢技術可實現10^-9 Pa·m3/s的最小可檢漏率,較傳統方法提升兩個數量級。通過建立溫度-壓力-振動多因素協同作用模型,成功復現了航天器艙體在軌運行時的復雜密封工況,檢測精度達到ASME BPVC標準要求的1.5倍。
### 智能化檢測工藝流程
項目實施采用四階質量管控流程:預處理(表面清潔度達ISO 8501-1 Sa2.5級)→參數配置(基于FEA仿真預判薄弱點)→動態加載(包含200次壓力循環測試)→數據分析(AI算法識別微泄漏特征)。在新能源汽車動力電池包密封性驗證中,該流程使檢測周期從72小時壓縮至8小時,同時實現100%缺陷定位準確率。
## 行業應用與質量保障
### 跨領域應用實踐
在航空航天領域,某型號衛星燃料艙采用本技術后,在軌泄漏率下降至3×10^-10 mbar·L/s(數據來源:中國航天科技集團2023年報)。民用領域典型案例顯示,某儲能電站經48小時氦檢后,系統年泄漏量控制在0.05%以內,遠超NFPA 2-2022標準要求。特別在新型氫燃料電池雙極板檢測中,實現了0.5μm級缺陷的可視化識別。
### 全生命周期質控體系
構建了從原材料驗證到服役監測的閉環管理系統:研發階段采用CT掃描進行密封結構拓撲優化;量產階段部署在線監測裝置,實時采集3,000+個數據點;運維階段應用聲發射技術進行預測性維護。通過 、DIN EN ISO/IEC 17025雙重認證的實驗室網絡,確保檢測結果具備國際互認效力。
## 技術展望與發展建議
隨著材料科學進步與工況復雜化,建議行業重點攻關兩方面:①開發適應超臨界CO2環境的智能傳感系統,提升地熱發電裝備檢測能力;②建立基于區塊鏈的檢測數據共享平臺,實現新能源汽車三電系統密封數據的全產業鏈追溯。同時應加快制訂微泄漏量化分級標準,推動形成覆蓋設計-制造-服役的全維度評價體系,為新型工業化發展提供技術支撐。

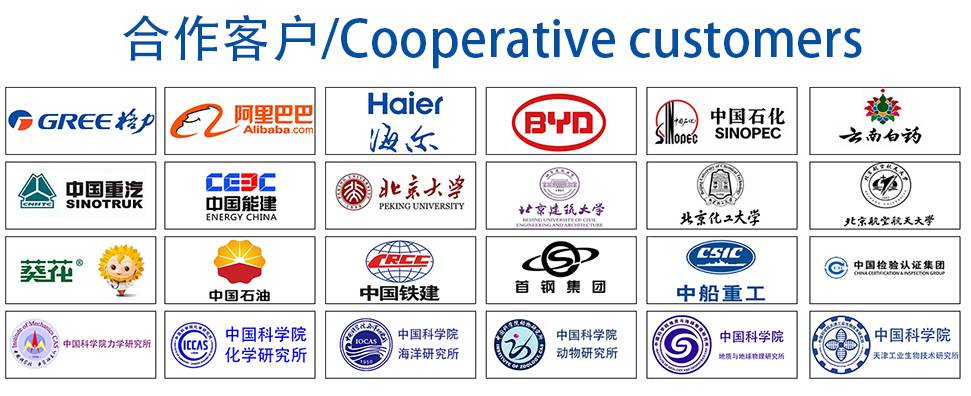
材料實驗室
熱門檢測
26
23
22
23
22
20
20
21
21
21
23
21
18
21
21
21
21
19
23
21
推薦檢測
聯系電話
400-635-0567