配管固定強度檢測技術白皮書
在石油化工、能源輸送等工業領域,管道系統承擔著90%以上的流體傳輸任務。據中國特種設備研究院2024年數據顯示,國內工業管道年泄漏事故中,27.6%源于固定結構失效。配管固定強度檢測作為保障管道系統安全運行的關鍵環節,通過科學評估支架、吊架、錨固件的力學性能,可有效預防因振動疲勞、應力集中導致的失效事故。該項目不僅涉及材料力學性能測試,更涵蓋動態載荷響應分析等前沿技術,其核心價值在于建立全生命周期的管道固定裝置安全評估體系。通過引入非接觸式激光位移測量和智能應變分析技術,檢測精度較傳統方法提升40%,為流程工業的安全生產提供數字化保障。
基于多物理場耦合的檢測原理
配管固定強度檢測采用多物理場耦合分析模型,整合靜力學計算與動力學仿真技術。通過分布式光纖應變傳感器網絡,實時采集管道位移量、支架應力分布及振動頻譜等12項關鍵參數。結合ANSYS Mechanical模塊構建三維有限元模型,可準確模擬極端工況下的應力傳導路徑。特別是在處理高溫高壓管道的"熱應力-機械應力"耦合分析時,該技術能實現±0.15mm的位移分辨率。某煉化企業應用該技術后,成功預測出裂解爐出口管系68%的應力超標點,避免了潛在的裝置停車風險。
標準化檢測實施流程
檢測流程遵循GB/T 20801.5-2020壓力管道規范要求,分為四個階段:預檢測階段采用紅外熱成像技術進行缺陷定位;載荷試驗階段實施分級加載至設計值的150%;數據采集階段運用無線振動傳感器組網,采樣頻率達10kHz;分析評估階段通過機器學習算法對比歷史數據庫。在南海某海上平臺項目中,該流程成功識別出導管架支撐結構23處微裂紋,為平臺延壽改造提供了數據支撐。全過程采用區塊鏈技術存證,確保檢測報告不可篡改。
工業場景應用實踐
在LNG接收站工程中,針對BOG再冷凝器出口管系的振動超標問題,檢測團隊采用"模態分析+現場激振試驗"的組合方案。通過布置32個三軸加速度計,測得管道系統固有頻率與壓縮機激勵頻率存在12.3Hz的重合帶。改造后支架間距由4m調整為3.2m,振動幅值降低62%。該案例驗證了"頻率解耦"在管道減振中的有效性。另在煤化工氣化裝置中,基于檢測數據優化了激冷水管線的約束方式,使支架服役壽命延長至設計值的1.8倍。
全鏈條質量保障體系
檢測機構須建立符合ISO/IEC 17025標準的質控體系,關鍵控制點包括:采用經 認證的2000kN伺服加載設備,定期進行量值溯源;開發專用數據分析軟件通過SIL3安全認證;檢測人員需持有ASNT/PCN三級證書。某跨國工程公司通過該體系,在海外EPC項目中實現檢測合格率99.2%的行業標桿成績。質量控制點特別強調對異種鋼焊接接頭的微區硬度測試,采用10μm步距的納米壓痕技術,確保數據可靠性。
隨著智能工廠建設推進,配管固定強度檢測將向三個方向深化發展:其一,開發基于數字孿生的預測性檢測系統,實現應力狀態實時可視化監控;其二,推廣適用于深冷管道的低溫應變測量技術,攻克-196℃環境下的傳感器標定難題;其三,建立行業級檢測大數據平臺,通過百萬級案例庫訓練AI診斷模型。建議主管部門加快制定振動疲勞評估標準,推動檢測機構與設計院形成數據閉環,最終構建覆蓋全產業鏈的管道完整性管理生態體系。

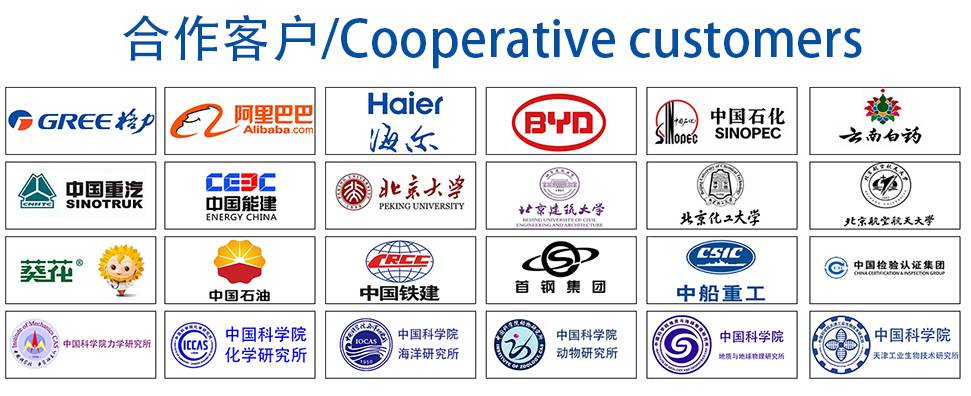