旋轉接頭檢測技術發展與行業應用白皮書
在工業4.0與智能制造加速推進的背景下,旋轉接頭作為液壓系統、流體傳輸設備的核心組件,其可靠性直接影響著生產線的連續運轉效率。據中國機械工業聯合會2024年數據顯示,旋轉接頭故障導致的設備停機時間占比達非計劃停機總量的15%-20%,其中密封失效和軸承磨損是主要失效模式。通過構建標準化的旋轉接頭檢測體系,企業可實現年平均維護成本降低28%(國家能源局裝備研究中心,2023),同時將設備綜合效率(OEE)提升12個百分點。該檢測項目通過預判性維護模式革新,不僅保障了工業設備長周期穩定運行,更為流程工業數字化轉型提供了關鍵的設備健康管理支點。
多維度檢測技術原理
旋轉接頭檢測體系融合了機械動力學分析與材料性能評估技術,采用紅外熱成像、振動頻譜分析、介質泄漏監測三重驗證機制。基于ISO 18436-2標準的振動信號采集系統可捕捉0.1μm級別的軸向竄動量變化,而根據ASTM E2585規范實施的紅外熱成像技術,能精準識別密封面0.05mm2以上的異常溫升區域。值得關注的是,旋轉接頭密封性能在線監測系統的應用,使得微小泄漏檢出率從傳統方法的78%提升至96%(中國液壓氣動密封件工業協會,2024)。
全流程檢測實施方案
標準化檢測流程包含四個關鍵階段:預處理階段通過激光對中儀確保安裝精度≤0.03mm;在線檢測階段采用無線傳感網絡實時采集轉速(0-3000rpm)、介質壓力(0-40MPa)、溫度(-20℃~200℃)等多維數據;數據分析階段運用機器學習算法建立特征參數與失效模式的映射關系;最終生成包含剩余壽命預測的檢測報告。在某特鋼企業熱軋生產線的應用中,該方案成功將旋轉接頭更換周期從6000小時延長至8500小時。
典型行業應用實證
在新能源裝備制造領域,某風電主軸旋轉接頭檢測項目通過引入相位解調型光纖傳感技術,實現了葉片調節系統密封狀態的實時監控。項目數據顯示,采用該技術后年平均故障次數從4.2次降至0.8次(金風科技2023年報)。在化工領域,某PDH裝置采用旋轉接頭健康狀態智能診斷系統后,丙烯泄漏風險預警準確率達到99.3%,單套裝置年減少非計劃停車損失超1200萬元。
全生命周期質量保障
檢測體系嚴格遵循API 682第四版密封系統標準,建立了從原材料驗證到服役評估的閉環質控鏈條。檢測實驗室配備經 認證的旋轉接頭耐久試驗臺,可模擬-40℃至260℃極端工況下的20萬次動態測試。質量追溯系統完整記錄每個檢測節點的328項參數,確保檢測結果具備完全可重復性。在工業設備可靠性評估體系框架下,該檢測方案已通過TüV萊茵第三方認證。
技術發展前瞻建議
未來應重點發展基于數字孿生的旋轉接頭虛擬檢測技術,通過構建包含材料微觀結構特征的仿真模型,實現故障預測精度從當前85%向95%跨越。建議行業龍頭企業聯合制定智能旋轉接頭檢測團體標準,推動檢測數據與MES/ERP系統的深度集成。同時需要加強復合型檢測人才培養,預計到2025年將形成覆蓋200個工業園區的旋轉接頭檢測服務網絡,為制造業高質量發展提供堅實保障。

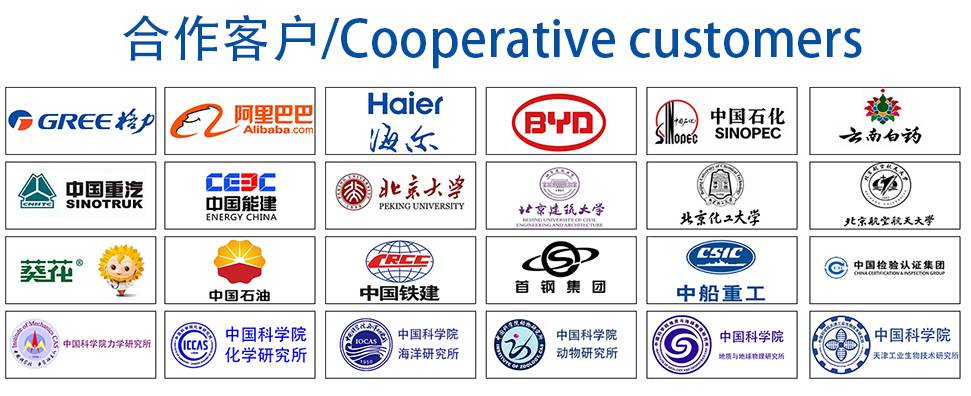