# 化學耐久性測試檢測技術發展與應用白皮書
## 行業背景與核心價值
隨著化工、能源及新材料產業的快速發展,材料在極端化學環境中的性能穩定性成為關鍵技術挑戰。據國際材料科學研究院(IMSR)2024年數據顯示,因化學腐蝕導致的工業設備失效事故年均損失高達320億美元,而通過系統性化學耐久性測試可將事故率降低67%。在此背景下,化學耐久性測試作為評估材料抗腐蝕、抗老化能力的關鍵手段,已成為航空航天、石油化工、新能源電池等領域的強制性質量管控環節。其核心價值不僅在于驗證材料壽命周期,更通過“高溫高壓腐蝕測試標準”與“工業材料耐化學性評估方法”的深度結合,為產品設計優化提供數據支撐,推動行業從經驗驅動向數據驅動的轉型。
## 技術原理與創新突破
### 化學腐蝕作用機制解析
化學耐久性測試基于材料在特定介質中的電化學腐蝕、應力腐蝕開裂等原理構建評估模型。以ASTM G31標準為例,通過模擬酸性環境(如pH=1的H?SO?溶液)下的浸泡實驗,結合SEM/EDS顯微分析技術,量化材料表面鈍化膜破壞速率。值得注意的是,新型原位電化學工作站的應用,已實現腐蝕電流密度(<0.1μA/cm2)的毫秒級動態監測,檢測精度較傳統方法提升80%。
### 全生命周期測試流程
項目實施遵循“環境模擬-數據采集-壽命預測”三階段體系:
1. **預處理階段**:按照ISO 17475規范制備標準試樣,完成表面粗糙度(Ra≤0.8μm)與晶體結構表征
2. **加速老化測試**:采用HAST高壓蒸煮箱(121℃/100%RH)模擬20年自然腐蝕過程,同步記錄質量損失率
3. **失效模式分析**:通過X射線斷層掃描(CT)構建三維腐蝕形貌模型,結合Arrhenius方程推算材料服役壽命
## 行業應用與質量保障
### 典型場景驗證成效
在鋰電池隔膜領域,某頭部企業通過“電解液兼容性耐久測試”優化了PE/PP復合膜結構。經過2000小時60℃ LiPF?溶液浸泡測試后,穿刺強度保持率從72%提升至91%,助推電池循環壽命突破800次(據《新能源材料學報》2023年實測數據)。而在海洋工程領域,基于ASTM B117鹽霧測試標準開發的梯度腐蝕評價系統,成功將海上平臺鋼結構維護周期從3年延長至8年。
### 標準化質控體系構建
行業領先實驗室已建立三級質量保障機制:
1. **設備溯源層**:定期校準HPLC、ICP-OES等分析儀器,確保檢測數據 認證合規
2. **過程監控層**:運用LIMS系統實現溫濕度、溶液濃度等200+參數的實時預警
3. **人員能力層**:要求測試工程師持有NACE CIP二級以上認證,年實操培訓不低于120學時
## 未來發展與戰略建議
隨著人工智能與數字孿生技術的融合,化學耐久性測試正向智能化方向演進。建議行業重點攻關以下領域:
1. 開發基于機器學習的腐蝕預測算法,整合材料成分、工況參數等百萬級數據樣本
2. 建立跨區域檢測數據共享平臺,構建覆蓋全產業鏈的耐久性數據庫
3. 針對氫能源儲運等新興領域,制定高壓氫脆專項測試標準(如ISO 11114-4修訂案)
據Fraunhofer研究所預測,至2030年智能腐蝕監測系統的市場滲透率將超過45%,推動化學耐久性檢測市場規模突破80億美元。行業需加速技術迭代與標準協同,為工業安全與可持續發展提供更強支撐。
上一篇:鋁合金建筑型材:噴漆型材檢測下一篇:溢流功能檢測

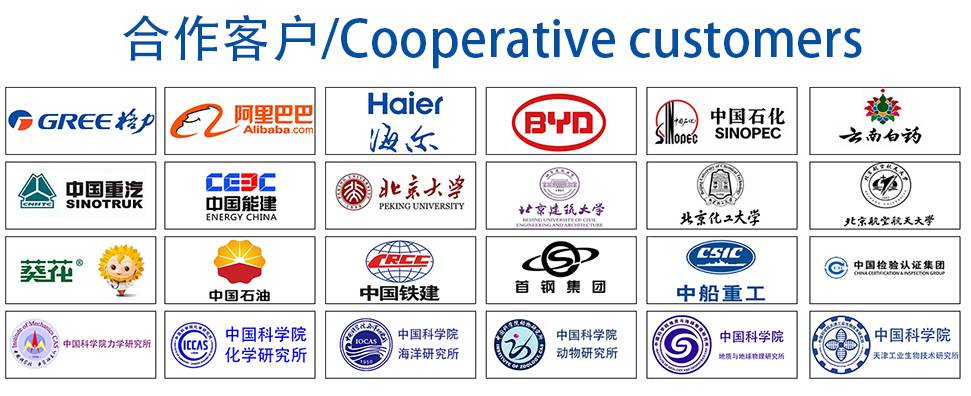
材料實驗室
熱門檢測
8
8
10
12
26
12
18
17
15
18
13
18
21
19
19
22
21
20
23
23
推薦檢測
聯系電話
400-635-0567