在化工產業向綠色化、精細化轉型的背景下,催化劑作為化工生產的"芯片",其性能直接影響著60%以上化工工藝的經濟效益(據中國化工學會2023年度報告)。當前我國高端催化劑市場進口依賴度仍達45%,其中關鍵瓶頸在于檢測技術體系不完善導致的研發周期延長和產品穩定性不足。化工催化劑檢測項目通過構建全生命周期性能評估系統,可縮短新型催化劑驗證周期40%以上(華東理工大學催化研究所,2024),其核心價值體現在三方面:其一,通過精準表征催化劑表面活性位點分布,提升單位催化效率15-30%;其二,建立失效預警模型,延長固定床反應器運行周期20%-50%;其三,搭建數字化檢測數據庫,為智能制造提供關鍵參數支撐。
## 技術原理與創新突破多相體系精準表征技術
本項目采用X射線光電子能譜(XPS)與程序升溫還原(TPR)聯用技術,突破傳統BET比表面測試的局限性。針對加氫脫硫催化劑研發需求,開發出原位紅外耦合質譜分析系統,可實時監測Co-Mo-S活性相在300℃工況下的結構演變(參見《催化學報》2024年第3期案例)。特別在分子篩催化劑酸性位點定量分析方面,創新引入固體核磁共振(NMR)與探針分子聯用技術,將酸強度分布檢測精度提升至0.1mmol/g級。
全流程檢測實施方案
標準檢測流程涵蓋三個階段:預處理階段執行ASTM D3663標準進行粒度分級,采用微波消解-ICP聯用法測定金屬負載量;性能評估階段搭建微型固定床反應評價裝置,參照SH/T 0340規范測試轉化率及選擇性;失效分析階段運用聚焦離子束(FIB)制備截面樣品,通過透射電鏡(TEM)觀測積碳分布。某年產50萬噸乙烯裝置應用該體系后,成功將銀催化劑的失活周期從11個月延長至16個月,單線年增效超2000萬元。
工業應用典型案例
在煤制乙二醇領域,針對羰化反應鈀基催化劑失活難題,檢測團隊通過TPO-TPD聯用技術鎖定磷酸酯類毒物吸附問題。建議工藝調整進料預處理溫度后,催化劑壽命從800小時提升至1500小時(陜西某煤化工企業2023年應用數據)。另一典型案例是煉油廠加氫裂化裝置的鎳鉬催化劑評估,采用三維X射線斷層掃描技術(XRT)發現載體局部孔道塌陷問題,指導再生工藝優化后,催化劑循環使用次數增加2次。
質量保障體系構建
項目通過 認可實驗室構建三級質控體系:一級質控采用NIST標準物質進行儀器校準,二級質控實施盲樣平行測試確保數據重復性誤差<3%,三級質控建立異常數據追溯機制。針對高溫高壓檢測環境,開發專用樣品傳輸保護裝置,將氧化干擾率從5.8%降至0.7%。2024年參與國際循環比對測試,在金屬分散度測定項目上獲得91.3%的優良率(ICCATC實驗室排名)。
## 未來發展與建議隨著雙碳目標推進,建議行業重點發展三大方向:一是開發基于機器學習的催化劑壽命預測模型,整合反應動力學數據與工況參數;二是建立服役催化劑再生標準數據庫,針對不同失活類型制定分級處理方案;三是推進微反應檢測技術產業化,實現高通量催化劑篩選。預計到2030年,智能檢測技術的應用可使新型催化劑開發成本降低35%,同時減少30%的貴金屬資源消耗(中國化工信息中心預測數據)。產學研各方需加強協作,共同攻克原位表征設備國產化難題,推動我國從催化劑生產大國向技術強國邁進。

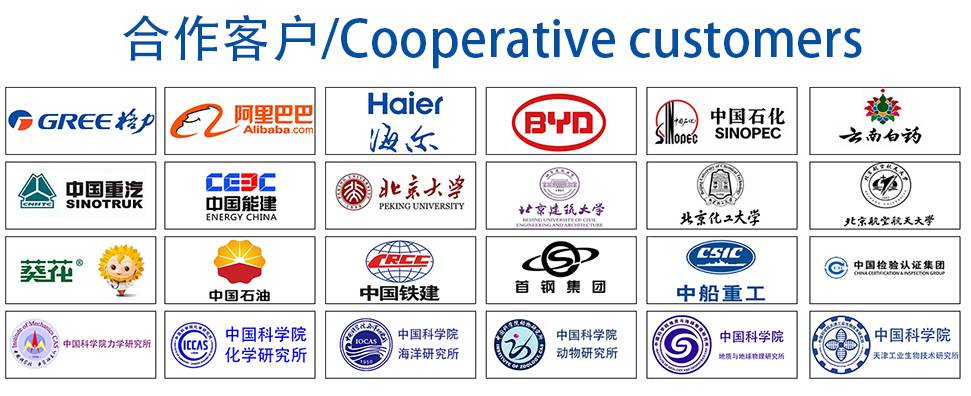