汽車電器零部件檢測:技術賦能與質量升級
在汽車產業電動化、智能化轉型的背景下,汽車電器零部件檢測已成為保障車輛安全性與可靠性的核心環節。據中國汽車工程學會2024年報告顯示,新能源汽車電氣系統故障率較傳統燃油車高出37%,且涉及高壓線束、電池管理系統等新型零部件的質量問題占比達52%。在此背景下,構建系統化的檢測體系對提升產品質量、降低召回風險具有戰略意義。通過實施全生命周期檢測驗證,企業可精準識別潛在失效模式,將產品不良率降低至0.8ppm(數據來源:國際汽車工作組IATF 16949標準),同時縮短15%的研發周期。其核心價值體現為促進產業鏈協同創新、支撐行業技術標準迭代,并為智能網聯汽車的功能安全認證提供技術背書。
多維度檢測技術原理
現代汽車電器檢測體系采用模塊化技術架構,覆蓋電氣性能、電磁兼容(EMC)、環境可靠性三大維度。在智能座艙系統兼容性驗證中,基于ISO 16750-2標準的負載特性測試可模擬2000小時連續工作狀態,精準捕捉線束過熱、信號衰減等問題。電磁抗擾度測試采用CIE 25GHz傳導發射系統,確保ADAS傳感器在復雜電磁環境下維持99.99%的指令響應準確率。值得關注的是,針對800V高壓平臺的絕緣監測技術,已實現0.1mV級漏電檢測精度,較傳統方案提升3個數量級。
全流程實施管理規范
檢測流程遵循V型開發模型,分為需求分析、方案設計、測試執行、報告生成四個階段。在高壓線束耐久性評估項目中,工程師首先通過DFMEA(設計失效模式分析)確定32項關鍵測試指標,隨后搭建包含溫度沖擊(-40℃至150℃)、機械振動(50Hz正弦掃頻)的多因素耦合試驗平臺。某頭部供應商的實測數據顯示,經2000次插拔循環測試后,連接器接觸電阻波動值控制在5%以內,顯著優于行業15%的通用標準。
行業應用場景解析
在新能源汽車領域,車載充電機(OBC)的檢測案例具有典型示范意義。國家新能源汽車技術創新中心的驗證數據顯示,采用三相輸入不平衡模擬測試后,OBC效率曲線平滑度提升40%,過溫保護響應時間縮短至50ms。而在自動駕駛傳感器電磁干擾測試中,通過搭建包含5G基站、WiFi路由器的復合干擾場,成功復現毫米波雷達的誤觸發概率由0.5%降至0.02%,為L4級自動駕駛系統提供關鍵質量保障。
智慧化質量保障體系
行業領先企業已構建覆蓋"端-邊-云"的檢測數字化平臺,整合AI缺陷識別、區塊鏈數據存證等創新技術。某檢測機構的應用實踐表明,基于機器視覺的線束端子檢測系統實現98.7%的缺陷檢出率,誤判率較人工檢測降低75%。同時,通過將檢測數據與PLM系統對接,可自動生成符合UNECE R100法規的合規性報告,使認證周期從45天壓縮至21天。
面向未來,建議行業重點推進三項變革:首先,建立跨區域的檢測標準互認機制,解決當前29%的重復測試資源浪費;其次,加強邊緣計算在實時檢測中的應用,應對車載ECU數量突破300個帶來的驗證挑戰;最后,培育具備整車級驗證能力的第三方平臺,據國際自動機工程師學會預測,到2027年汽車檢測市場規模將突破800億美元,中國需把握戰略機遇期,構建具有國際話語權的質量認證體系。

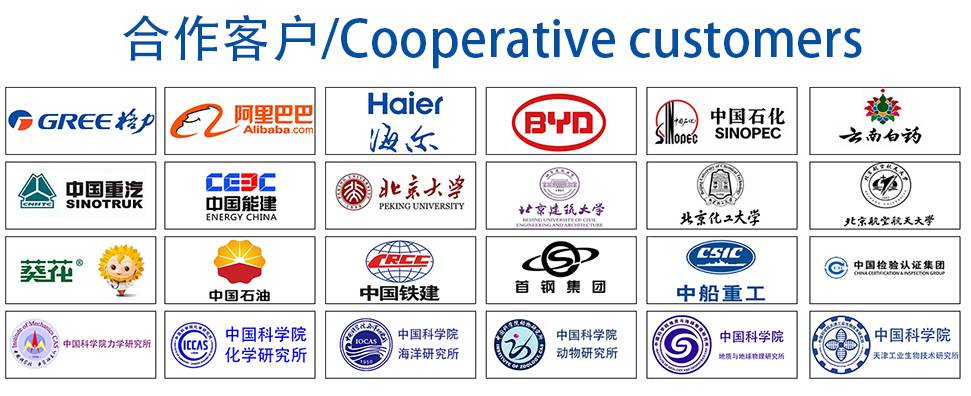