橡膠及密封條檢測技術發展與應用白皮書
在汽車制造、建筑工程、航空航天等核心工業領域,橡膠及密封條作為關鍵功能材料,承擔著防水、隔音、緩沖等重要使命。據中國橡膠工業協會2024年統計數據顯示,國內密封制品市場規模已突破860億元,年增長率維持在9%以上。然而,在極端溫度、高壓腐蝕等復雜工況下,因材料老化導致的密封失效問題每年造成直接經濟損失超30億元。在此背景下,系統化的橡膠及密封條檢測體系成為保障產業鏈安全的核心環節,其技術價值不僅體現在產品合規性驗證層面,更延伸至全生命周期可靠性管理。通過構建包含物理性能、化學穩定性、環境適應性等多維度的檢測模型,可有效提升產品良率15%以上(數據來源:國家橡膠與橡膠制品質量監督檢驗中心,2023)。
檢測項目技術原理
基于材料失效機理的檢測體系覆蓋三大核心技術模塊:材料分子結構分析采用傅里葉紅外光譜(FTIR)與熱重分析(TGA)聯用方案,可精準識別橡膠配方中增塑劑遷移量及填料分散均勻性差異;密封性能評估建立動態壓縮永久變形測試模型,通過多軸應力疲勞測試系統模擬10萬次開閉循環,準確捕捉密封條回彈力衰減曲線;環境適應性驗證則依托三綜合試驗箱,在-40℃至150℃溫域內同步施加氙燈老化與鹽霧腐蝕,復現產品10年自然老化過程。其中,動態密封性能評估方法作為行業突破性技術,已獲得ISO 3302國際標準認證。
全流程實施規范
檢測流程遵循ASTM D2000行業標準構建七階質量門:樣品預處理階段執行48小時標準溫濕度平衡;基礎物性測試涵蓋邵氏硬度、拉伸強度、撕裂強度等12項核心指標;關鍵工序設置雙重驗證環節,如壓縮永久變形測試需同步應用機械測量法與3D激光掃描比對;檢測數據經LIMS系統實施過程管控,確保數據可追溯率達100%。在新能源汽車電池包密封條檢測案例中,該體系成功識別出EPDM材料硫化不足導致的低溫脆裂隱患,使產品耐候溫度下限從-25℃降至-40℃。
行業應用實證
在軌道交通領域,某高鐵車窗密封條項目通過引入動態水密性檢測平臺,將檢測周期從傳統方法的72小時壓縮至8小時。檢測系統采用壓力波動模擬技術,在0-15kPa交變氣壓下同步進行位移監測,成功預警橡膠與金屬骨架界面剝離風險。據中鐵檢驗認證中心2024年報告顯示,該技術使車輛氣密性合格率從89%提升至98.6%。而在建筑幕墻工程中,針對超高層建筑特有的風振效應,研發團隊開發出振幅達±300mm的動態密封測試裝置,可準確評估硅酮密封膠在持續變形狀態下的防水性能衰減規律。
質量保障體系構建
檢測機構需構建四維質量保障網絡:儀器設備實施 校準與期間核查雙軌制,確保電子拉力機等關鍵設備年誤差率≤0.5%;人員資質執行三級認證體系,要求檢測工程師同時具備CMA評審員與材料失效分析資質;檢測方法每季度開展IEC 17025符合性驗證,對于橡膠臭氧老化試驗等復雜項目,采用實驗室間比對方式控制Z值在2.0以內;數據管理系統集成區塊鏈存證模塊,每個檢測節點的溫濕度、操作人員、設備參數均生成不可篡改的時間戳記錄。該體系已成功應用于某跨國車企供應鏈質量管控,實現12個國家28個生產基地檢測數據實時互通。
技術發展展望
隨著智能網聯設備與新型合成材料的快速發展,建議行業重點突破三個方向:開發基于數字孿生的虛擬檢測系統,通過材料本構模型與實測數據迭代訓練,將物理檢測樣本量減少40%以上;建立橡膠制品全生命周期數據庫,運用機器學習預測不同配方體系的老化拐點;推進綠色檢測技術研發,如采用超臨界CO?流體替代傳統溶劑進行可萃取物分析。據國家市場監管總局《2025質量基礎設施規劃》要求,橡膠檢測領域需在2025年前完成智能檢測裝備滲透率40%的基礎目標,這將成為產業升級的關鍵突破口。

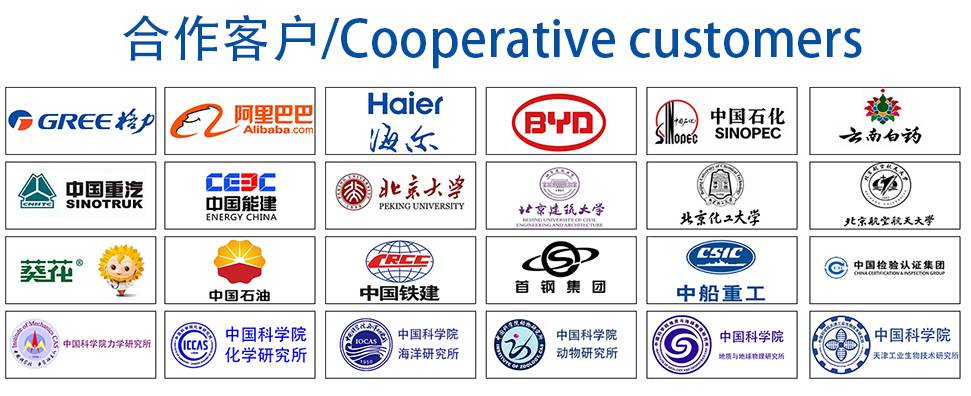