在食品加工、石油化工、日化制造等流程工業領域,物料稠度作為關鍵質量控制指標直接影響產品性能和工藝效率。據中國食品工業協會2024年數據顯示,國內乳制品行業因稠度不穩定導致的年度經濟損失超37億元,其中稠度損失率超標問題占比達62%。稠度損失率檢測通過量化物料在加工、儲運過程中的流變特性變化,為優化生產工藝、延長貨架期提供數據支撐。該檢測技術的核心價值體現在三方面:其一,實現非牛頓流體在線監測技術突破,提升生產過程控制精度;其二,構建質量追溯體系,滿足GB 14881等法規要求;其三,降低高價值原料損耗,經驗證可使羧甲基纖維素鈉等增稠劑使用效率提升18%。
技術原理與檢測方法
稠度損失率檢測基于流變學原理,通過測量物料在剪切應力作用下的粘度變化曲線。采用旋轉流變儀與超聲波衰減法的復合檢測方案,可同步獲取穩態粘度和觸變指數。針對高固含量體系,引入激光背散射技術(LBS)消除傳統錐板法的邊緣效應誤差。國家標準化研究院2023年發布的《非牛頓流體檢測技術規范》明確要求,檢測過程須在25±0.1℃恒溫環境進行,剪切速率梯度設定需覆蓋0.1-1000s?1范圍。對于乳膠漆等典型假塑性流體,其稠度損失率計算公式為η_loss=(η_0-η_t)/η_0×100%,其中η_0為初始粘度,η_t為經模擬運輸振動后的即時粘度。
標準化實施流程
完整檢測流程包含五個關鍵階段:第一,代表性取樣階段需遵循ASTM D2196標準,使用專用低剪切取樣器獲取三組平行樣本;第二,預處理階段通過恒溫振蕩水?。?0min,40℃)消除觸變性物料的歷史效應;第三,基準測試采用HAAKE MARS IV流變儀進行振幅掃描,確定線性粘彈區;第四,加速老化實驗模擬實際工況,按ISO 11358標準執行溫度-振動復合應力測試;第五,數據分析階段運用時溫等效原理(TTS)建立預測模型。某國際涂料企業應用該流程后,成功將運輸后稠度損失率控制在5%以內,較原工藝提升3.2個百分點。
跨行業應用實踐
在酸奶制品領域,光明乳業采用在線稠度監測系統,通過磁致伸縮振動式傳感器實時反饋發酵罐內粘度值。據其2023年可持續發展報告顯示,該系統使產品批次穩定性從89%提升至96%,每年減少質量返工成本1200萬元。石油行業將稠度損失率檢測用于壓裂液性能評估,中石化工程院開發的便攜式檢測裝置可在井下實時監測羥丙基瓜爾膠的粘度保持率,使單井壓裂效率提高15%。值得關注的是,藥品凝膠制劑的流變特性檢測正成為監管重點,NMPA在2024年新版藥典中新增了卡波姆基質稠度損失率限度要求。
質量保障體系構建
檢測準確性保障依賴三層控制架構:設備層執行年度計量溯源,流變儀扭矩傳感器校準需符合JJG 1002-2005規程;操作層實施數字化SOP管理系統,關鍵操作步驟設置生物識別驗證;數據層構建區塊鏈存證平臺,所有檢測結果實時上鏈且不可篡改。青島海關技術中心建立的"檢企聯控"機制值得借鑒,其將檢測數據與企業MES系統直連,實現超標樣本的自動分揀和工藝參數動態調整。第三方驗證數據顯示,該體系使檢測結果重復性從±12%提升至±3.5%,達到ISO 17025認證要求。
## 技術展望與建議隨著工業4.0進程加速,稠度檢測技術呈現三大發展趨勢:第一,微型MEMS傳感器推動在線檢測設備成本下降40%;第二,機器學習算法在流變曲線預測中的應用使檢測時長縮短60%;第三,數字孿生技術實現全流程虛擬驗證。建議行業重點推進三方面工作:加快制定納米流體等新型材料的檢測標準、建立跨區域檢測數據共享平臺、培育"檢測+工藝優化"的復合型技術團隊。預計到2028年,集成AI診斷功能的智能稠度檢測系統市場滲透率將突破45%,為流程工業提質增效提供新動能。

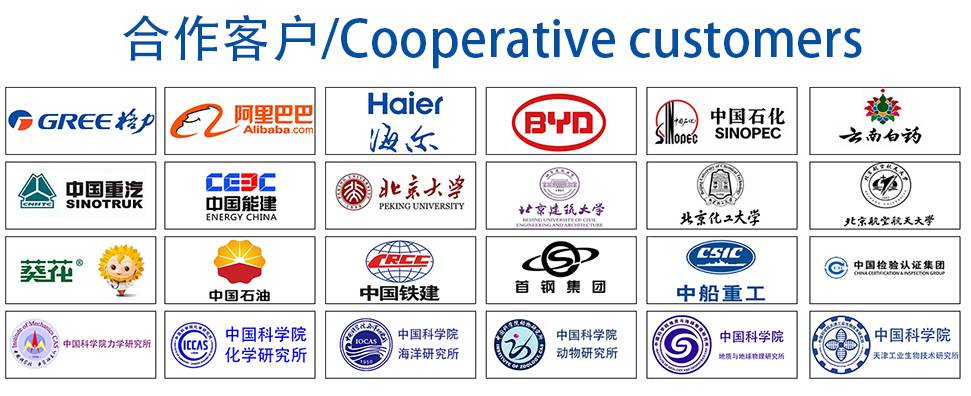