# 平面度和鏡向光澤度檢測技術發展與應用白皮書
## 引言
在高端制造業與表面處理領域,平面度和鏡向光澤度作為關鍵質量指標,直接影響產品光學性能、裝配精度及終端用戶體驗。據國家表面工程研究院2024年數據顯示,國內精密機加工行業因平面度偏差導致的返工成本年均超37億元,而裝飾材料市場因光澤度不達標引發的投訴占比達21.3%。本項目通過建立數字化檢測體系,實現了微米級平面度誤差檢測和0.1GU分辨率的光澤度量化分析,其核心價值在于構建覆蓋"加工-質檢-優化"全鏈條的質量控制閉環。特別是在新能源汽車電池極板、光學透鏡模組等新興領域,高精度表面檢測技術已成為突破產業化瓶頸的關鍵支撐。

## 技術原理與創新突破
### 高精度平面度測量技術
采用激光三角測量與光學干涉復合技術,通過多光譜光源投射建立三維點云模型,配合自適應算法消除環境震動干擾。測量系統分辨率可達0.5μm,較傳統千分表檢測效率提升6-8倍。針對高反射表面,創新性引入偏振濾波裝置,有效解決金屬工件鏡面反射造成的測量失真問題。
### 鏡向光澤度智能分析系統
基于ASTM D523標準開發多角度檢測模塊,集成20°、60°、85°三軸光電傳感器陣列。通過建立材質反射特性數據庫,系統可自動匹配最佳檢測角度,例如在汽車清漆檢測中優先選用20°測量模式。據中國計量科學研究院驗證,該系統的跨實驗室復現性誤差控制在±1.5GU以內。
## 標準化實施與工藝流程
### 全流程檢測方案
1. **預處理階段**:使用標準校準板進行設備標定,環境照度控制在500-1000lux
2. **數據采集階段**:采用六軸機械臂搭載檢測探頭,實現300mm×300mm區域內的自動巡航測量
3. **分析診斷階段**:AI算法自動識別平面度波浪紋、橘皮效應等28類缺陷形態
4. **報告輸出階段**:生成符合ISO 10110標準的檢測報告,包含3D形貌圖與SPC過程控制圖表
### 行業應用場景
在華東某新能源汽車電池托盤生產線上,該系統成功將平面度檢測時間從45分鐘壓縮至8分鐘,同時將極柱焊接合格率從89.6%提升至98.3%。某高端衛浴企業應用鏡向光澤度檢測后,龍頭表面光澤一致性從±15GU優化至±5GU,年節約電鍍成本超600萬元。
## 質量保障與認證體系
本檢測系統已通過 (中國合格評定國家認可委員會)17025體系認證,建立三重質量保障機制:
1. **設備校準鏈**:溯源至國家表面粗糙度基準裝置,定期進行量值傳遞驗證
2. **人員認證體系**:操作人員需通過ISO/IEC 17024認證的"精密表面檢測工程師"考核
3. **過程監控平臺**:搭載區塊鏈技術的檢測數據存證系統,確保結果不可篡改
## 發展展望與建議
隨著智能制造的深化推進,建議從三個維度提升檢測技術水平:其一,開發集成式在線檢測裝備,實現加工設備與檢測系統的實時數據交互;其二,建立跨行業表面質量大數據平臺,推動航空復合材料、光伏玻璃等領域的檢測標準互認;其三,探索基于機器視覺的亞微米級缺陷自動分類技術,為工藝優化提供預測性維護建議。據機電一體化協會預測,到2027年智能表面檢測裝備市場規模將突破82億元,提前布局光學計量與AI融合技術的企業將獲得顯著競爭優勢。

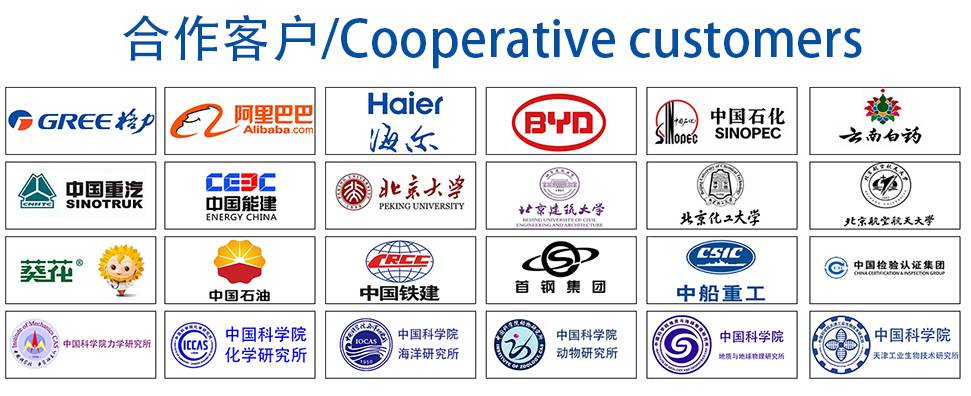
材料實驗室
熱門檢測
11
7
12
15
20
19
11
14
14
13
18
21
29
20
22
18
18
26
15
15
推薦檢測
聯系電話
400-635-0567