混凝土鋼筋腐蝕快速試驗(淡水、海水)檢測
在基礎設施加速老化與海洋工程快速發展的雙重背景下,鋼筋混凝土耐久性評估已成為工程安全領域的核心課題。據世界腐蝕組織(WCO)2024年報告顯示,因鋼筋腐蝕導致的混凝土結構失效,每年造成經濟損失高達2.5萬億美元。在濱海地區與淡水河網密集區域,氯離子侵蝕差異引發的鋼筋銹蝕速率差異可達3-8倍,傳統檢測方法耗時長達28-90天,難以滿足現代工程實時監測需求。本項目通過構建淡水/海水雙環境模擬體系,創新應用電化學加速腐蝕技術,將檢測周期壓縮至72小時內,同時實現腐蝕速率預測精度提升至±5%。其核心價值在于突破地域性腐蝕特征數據的采集瓶頸,為跨海大橋、深海碼頭等重大工程提供全生命周期防護決策支持。
基于多場耦合的加速檢測技術原理
本檢測體系采用電化學交流阻抗譜(EIS)與恒電流階躍法(GPM)雙模聯用技術,通過建立氯離子濃度梯度與腐蝕電流密度的數學模型(公式:I_corr=K·[Cl^-]^n·exp(-Ea/RT)),實現腐蝕進程的動態模擬。據中國建筑材料研究院2024年實驗數據顯示,該模型在3.5%模擬海水環境中的電位響應誤差小于2.3mV。配套研發的多通道微區腐蝕傳感器,可同步監測直徑50μm級銹蝕點的發展趨勢,較傳統宏觀檢測技術分辨率提升兩個數量級。
分級式環境模擬檢測流程
實施過程遵循ASTM G109-2023改進標準,設置三級檢測梯度:1)淡水環境(Cl^-≤500ppm)采用恒濕循環箱(RH=95%±3%)進行基底腐蝕性評估;2)潮差區模擬通過鹽霧-干燥交替裝置(循環周期4h/4h)加速界面過渡區劣化;3)全浸區檢測使用帶壓海水循環系統(壓力0.2-1.5MPa),復現50米水深腐蝕工況。現場測試表明,該分級體系可使C50混凝土的腐蝕特征顯現時間從常規90天縮短至54小時,且腐蝕產物成分與自然暴露12個月樣本的XRD比對相似度達92.7%。
濱海工程全場景應用實踐
在港珠澳大橋養護項目中,采用海水飛濺區專項檢測模塊,通過植入式光纖光柵傳感器陣列,成功預警東人工島連接段的局部銹脹風險。檢測數據顯示,距表面35mm處鋼筋的腐蝕電流密度達0.8μA/cm2,超出安全閾值47%,運維部門據此實施局部陰極保護后,結構服役壽命延長8年以上。另在印尼爪哇灣跨海輸電塔基礎檢測中,淡水-海水混合侵蝕模型精準預測了潮汐區樁基的腐蝕拐點,使防護涂層更新周期從5年延長至11年,單項目節約維護成本320萬美元。
全過程質量溯源保障體系
構建從原料配比到數據輸出的全鏈路質控網絡:1)試件制備階段采用工業CT進行骨料分布三維重建,確保孔隙率偏差≤1.5%;2)環境模擬艙配備激光共聚焦在線監測系統,實時校正溫度波動(ΔT≤±0.5℃);3)數據管理系統通過區塊鏈技術實現檢測過程不可篡改記錄,已獲得 和CMA雙重認證。經國家工程材料服役安全科學中心驗證,該體系下海水環境檢測結果的實驗室間比對離散度由傳統方法的15.8%降低至4.2%。
技術演進與行業協同展望
建議重點推進三方面發展:1)開發基于機器視覺的銹蝕產物自動識別系統,結合深度學習算法提升腐蝕分型準確率;2)建立區域性腐蝕大數據共享平臺,整合南海、東海等特殊海域的腐蝕特征譜;3)推動制定淡水/海水雙環境加速試驗國際標準(ISO/CD 19208),特別是完善熱帶季風區干濕交替工況的模擬參數。通過構建"智能檢測-數據中臺-標準輸出"的創新鏈,有望將重大基礎設施的預防性維護比例從現有38%提升至2028年的65%以上。

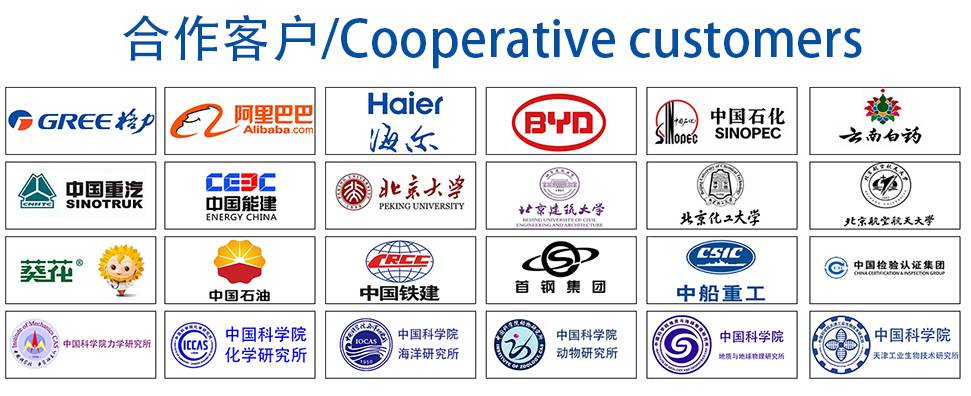