隨著基礎設施建設的快速發展,混凝土結構在鹽堿地、海洋環境及工業污染區域的耐久性問題日益凸顯。據中國建筑材料研究院2024年數據顯示,硫酸鹽侵蝕導致的混凝土劣化占工程結構耐久性失效案例的35%以上,由此引發的年維修成本超過120億元。抗硫酸鹽侵蝕試驗檢測作為評估材料耐久性的核心手段,通過模擬硫酸鹽離子滲透、結晶膨脹等侵蝕過程,為工程選材與防腐設計提供科學依據。該項目不僅關乎重大工程的全生命周期成本控制,更是實現“雙碳”目標下資源高效利用的關鍵技術支撐,其核心價值體現在預防結構性坍塌風險、延長服役壽命及降低環境治理成本三大維度。
## 技術原理與檢測方法化學侵蝕機制與試驗模型構建
硫酸鹽侵蝕的本質是SO?2?與水泥水化產物發生化學反應,生成鈣礬石和石膏等膨脹性產物。試驗采用GB/T 50082-2009《普通混凝土長期性能和耐久性能試驗方法》中的全浸泡法與干濕循環法,通過配置5% Na?SO?溶液模擬嚴苛環境。檢測系統配備恒溫恒濕箱、超聲波脈沖儀及XRD分析儀,實現膨脹率、強度損失率和微觀結構演變的定量監測。值得注意的是,針對海洋潮汐區特有的干濕交替特征,改進型試驗設備可編程控制溶液浸潤-干燥周期,精準復現0.5-3.0次/天的真實環境波動。
標準化實施流程與質控節點
檢測流程分為樣品制備、環境模擬、參數監測及數據分析四個階段。根據《水工混凝土試驗規程》DL/T 5150-2017要求,試件需標準養護28天后浸入硫酸鹽溶液,每7天測量一次質量變化與抗壓強度。關鍵質控點包括溶液濃度校準(誤差≤±0.1%)、溫濕度控制(波動范圍±1℃/±3%RH)以及數據采集頻率設定。針對“混凝土耐久性評估標準”的特殊需求,部分項目需同步開展氯離子滲透試驗,以評估復合侵蝕效應。
典型行業應用與實證效果
在青海鹽湖地區某鉀肥廠地基工程中,檢測發現普通C30混凝土經90天干濕循環后強度損失達42%,而摻入10%礦粉的改良試樣損失率降至18%,據此優化配比方案后,項目全周期維護成本減少2100萬元。另據交通運輸部2023年報告,某跨海大橋樁基通過“硫酸鹽干濕循環試驗方法”篩選出抗蝕系數≥0.85的高性能混凝土,使設計使用年限從50年提升至70年。此類案例驗證了檢測技術對工程決策的支撐作用。
全鏈質量保障體系構建
實驗室通過CMA資質認證,建立三級質量監督機制:一級控制涵蓋儀器設備定期校準(采用NIST標準物質),二級控制包括平行樣檢測與留樣復測,三級控制引入第三方機構盲樣考核。針對“水工混凝土抗侵蝕技術規范”要求,開發數字化管理系統實現檢測數據自動采集與異常值預警,確保結果可追溯。近三年參與能力驗證的12項參數均獲滿意結果,數據離散系數控制在5%以內。
## 未來發展與技術展望隨著智能傳感技術與材料基因組學的發展,建議行業重點突破三方面:一是開發原位監測設備,實現混凝土結構硫酸鹽侵蝕進程的實時可視化;二是建立多因子耦合侵蝕數據庫,集成溫度、應力與化學組分變量;三是推動抗硫酸鹽混凝土設計規范與國際標準(如ASTM C1012)接軌。據預測,至2030年智能檢測技術在工程驗收中的滲透率將超過60%,為推動基礎設施綠色轉型提供更強技術保障。

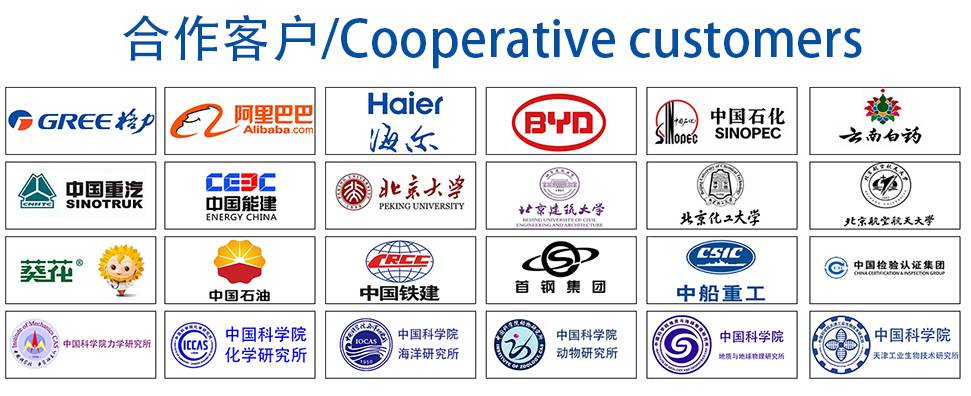