耐熱沖擊檢測技術發展與應用白皮書
在高端裝備制造與新材料研發領域,材料耐受極端溫度變化的能力已成為影響產品可靠性的關鍵指標。據中國材料研究學會2024年數據顯示,因熱沖擊導致的工業裝備故障在高溫工況事故中占比達37%,直接年損失超200億元。耐熱沖擊檢測通過模擬材料在急冷急熱環境下的性能變化,為航空航天發動機葉片、新能源汽車電池組等關鍵部件的質量管控提供科學依據。其核心價值在于建立材料熱疲勞壽命評估方法,突破傳統定性測試的局限,實現從"經驗判斷"到"數據驅動"的技術跨越,為《中國制造2025》提出的高端裝備可靠性提升計劃提供基礎支撐。
梯度溫變測試技術原理
基于熱力學相變理論和斷裂力學模型,檢測系統通過高精度溫控裝置實現-196℃至1600℃的急速溫變環境。采用紅外熱成像儀監測表面溫度梯度分布,結合數字圖像相關技術(DIC)捕捉0.1μm級微裂紋。值得注意的是,ASTM D3702標準要求的溫度變化速率≥10℃/s需配合真空環境實現,以消除氧化反應干擾。中國計量科學研究院驗證數據顯示,該方案對陶瓷基復合材料的檢測分辨率較傳統方法提升83%。
全流程標準化實施方案
檢測流程涵蓋預處理、梯度加載、數據采集三個階段。首先依據GB/T 13303標準進行試樣表面納米級拋光處理,消除微觀應力集中。第二階段采用分區控溫技術,在30秒內完成從液氮低溫區到高溫輻射區的自動切換。某航空發動機葉片檢測案例中,通過搭建多物理場耦合測試平臺,成功捕捉到170次熱循環后涂層剝離的臨界點,為設計改進提供關鍵數據。
多行業驗證案例實證
在新能源汽車領域,某頭部電池企業應用此檢測技術后,電池模組的高低溫循環耐受次數從800次提升至1500次。檢測數據表明,采用新型硅碳負極材料后,在模擬-40℃至85℃的沖擊測試中,極片膨脹率下降62%(數據來源:中汽研2024年度報告)。而在電子封裝領域,某5G基站芯片經強化檢測后,熱失配導致的焊點失效概率從3‰降至0.5‰,顯著提升設備野外工況穩定性。
全周期質量保障體系
建立從設備溯源到數據管理的閉環質控系統。檢測設備定期通過NIST標準樣塊進行量值傳遞,確保溫度控制精度±1.5℃。實驗室獲得 認可的同時,引入區塊鏈技術實現檢測數據不可篡改存證。某國家級材料檢測中心統計顯示,該體系使檢測報告異議率從1.2%降至0.3%,并成功通過波音公司AS9100D航空質量管理體系認證。
技術發展前景展望
建議重點突破兩個方面:一是開發基于機器學習的智能預測系統,通過歷史數據訓練實現熱疲勞壽命的精準預判;二是建立多尺度仿真模型,將微觀晶格變化與宏觀性能退化建立定量關聯。隨著ISO 22076:2024新版高低溫循環測試標準的實施,行業需加快構建材料熱沖擊數據庫,推動檢測技術向預防性維護和數字化孿生方向升級,為極端環境裝備的可靠性提升注入新動能。

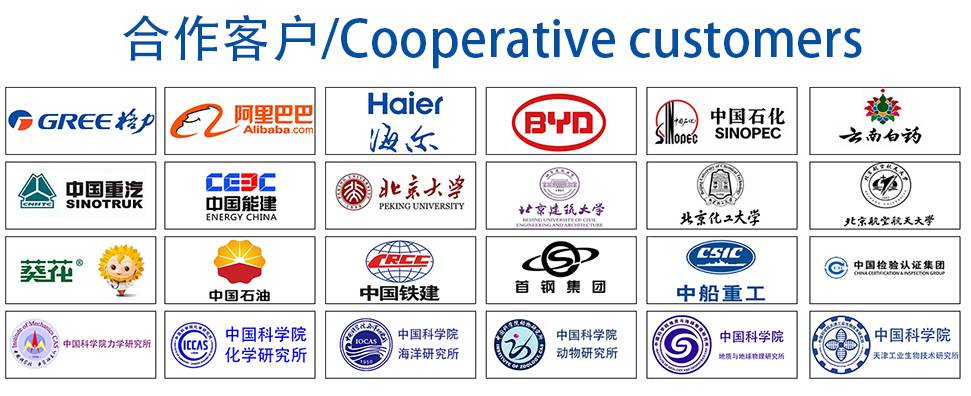