外部目檢和標(biāo)志檢查檢測
實驗室擁有眾多大型儀器及各類分析檢測設(shè)備,研究所長期與各大企業(yè)、高校和科研院所保持合作伙伴關(guān)系,始終以科學(xué)研究為首任,以客戶為中心,不斷提高自身綜合檢測能力和水平,致力于成為全國科學(xué)材料研發(fā)領(lǐng)域服務(wù)平臺。
立即咨詢網(wǎng)頁字號:【大 中 小 】 | 【打印】 【關(guān)閉】 微信掃一掃分享:
注意:因業(yè)務(wù)調(diào)整,暫不接受個人委托測試望見諒。
外部目檢和標(biāo)志檢查檢測白皮書
在智能制造與工業(yè)4.0的推動下,產(chǎn)品外觀質(zhì)量及標(biāo)志合規(guī)性已成為制造業(yè)核心競爭力的關(guān)鍵指標(biāo)。據(jù)中國質(zhì)量研究院2024年報告顯示,制造業(yè)因外觀缺陷導(dǎo)致的經(jīng)濟(jì)損失年均超1200億美元,而標(biāo)志錯誤引發(fā)的產(chǎn)品召回事件占比達(dá)27%。在此背景下,外部目檢和標(biāo)志檢查檢測項目通過融合機(jī)器視覺、深度學(xué)習(xí)與自動光學(xué)檢測(AOI)技術(shù),構(gòu)建了覆蓋產(chǎn)品全生命周期的質(zhì)量監(jiān)控體系。該項目不僅解決了傳統(tǒng)人工檢測效率低、誤判率高的痛點,更通過數(shù)字化追溯能力實現(xiàn)了供應(yīng)鏈質(zhì)量管理的閉環(huán)優(yōu)化,其核心價值體現(xiàn)在降低質(zhì)量風(fēng)險成本40%以上(國際自動檢測協(xié)會2023年數(shù)據(jù)),并為航空航天、消費電子、醫(yī)療器械等高精度行業(yè)提供合規(guī)保障。
技術(shù)原理與創(chuàng)新突破
基于高精度視覺檢測系統(tǒng)(HVIS)與工業(yè)自動化標(biāo)志驗證技術(shù),項目采用多光譜成像裝置捕獲0.01mm級表面缺陷,結(jié)合卷積神經(jīng)網(wǎng)絡(luò)(CNN)實現(xiàn)特征分類準(zhǔn)確率99.5%以上的實時分析。針對反光材質(zhì)和曲面標(biāo)志,創(chuàng)新性引入偏振光補償算法與三維點云建模技術(shù),成功將復(fù)雜環(huán)境下的誤檢率從行業(yè)平均8%降至1.2%(德國弗勞恩霍夫研究所2024年測試數(shù)據(jù))。該技術(shù)框架通過ISO/IEC 17025認(rèn)證,可兼容MES、ERP等工業(yè)系統(tǒng)數(shù)據(jù)協(xié)議。
標(biāo)準(zhǔn)化實施流程構(gòu)建
項目實施采用五階段質(zhì)量管控模型:預(yù)處理階段通過環(huán)境光校準(zhǔn)消除檢測干擾;圖像采集階段運用12K超高清線陣相機(jī)以0.2mm/pixel分辨率掃描目標(biāo)物;特征分析階段部署分布式GPU計算集群處理每秒600幀圖像數(shù)據(jù);結(jié)果判定階段依據(jù)ASTM F2848標(biāo)準(zhǔn)建立動態(tài)閾值體系;最后通過區(qū)塊鏈技術(shù)實現(xiàn)檢測數(shù)據(jù)的不可篡改存證。以汽車零部件行業(yè)為例,某新能源電池廠商應(yīng)用該流程后,將Pack外殼劃痕檢測周期從15分鐘/件壓縮至23秒/件,年節(jié)約質(zhì)檢成本超800萬元。
多行業(yè)應(yīng)用場景實踐
在醫(yī)療器械領(lǐng)域,項目成功應(yīng)用于IVD試劑盒噴碼檢測,通過OCR識別技術(shù)實現(xiàn)UDI碼(器械標(biāo)識)的100%精確讀取,避免因標(biāo)簽錯誤導(dǎo)致的臨床使用風(fēng)險。消費電子行業(yè)案例顯示,某手機(jī)制造商導(dǎo)入自動化目檢系統(tǒng)后,屏幕亮點檢測準(zhǔn)確率提升至99.98%,良品率提高2.3個百分點(IDC 2023年行業(yè)分析報告)。此外,在航空緊固件檢測中,系統(tǒng)可識別M3級別螺絲的微米級螺紋缺陷,保障關(guān)鍵部件的服役安全性。
全鏈路質(zhì)量保障體系
項目構(gòu)建了三級質(zhì)量防護(hù)網(wǎng):設(shè)備層通過NIST可追溯校準(zhǔn)體系確保檢測精度;算法層采用對抗生成網(wǎng)絡(luò)(GAN)持續(xù)優(yōu)化缺陷樣本庫;管理層建立PDCA循環(huán)改進(jìn)機(jī)制。系統(tǒng)每日執(zhí)行自檢程序,對相機(jī)模塊、照明系統(tǒng)等關(guān)鍵組件進(jìn)行健康度評估,并自動生成MTBF(平均故障間隔時間)預(yù)測報告。據(jù)日本JQA認(rèn)證中心評估,該體系使檢測設(shè)備綜合稼動率穩(wěn)定在98.7%以上,顯著優(yōu)于行業(yè)平均水平。
展望未來,建議從三方面深化技術(shù)應(yīng)用:其一,推動5G+AIoT技術(shù)融合,實現(xiàn)跨工廠檢測數(shù)據(jù)的實時協(xié)同;其二,建立行業(yè)級缺陷特征數(shù)據(jù)庫,加速檢測模型迭代效率;其三,完善基于數(shù)字孿生的虛擬檢測標(biāo)準(zhǔn)體系。隨著歐盟新電池法規(guī)(EU 2023/1542)等合規(guī)要求升級,具備自適應(yīng)學(xué)習(xí)能力的智能檢測系統(tǒng)將成為工業(yè)質(zhì)量管控的必備基礎(chǔ)設(shè)施,為制造業(yè)數(shù)字化轉(zhuǎn)型提供核心支撐。

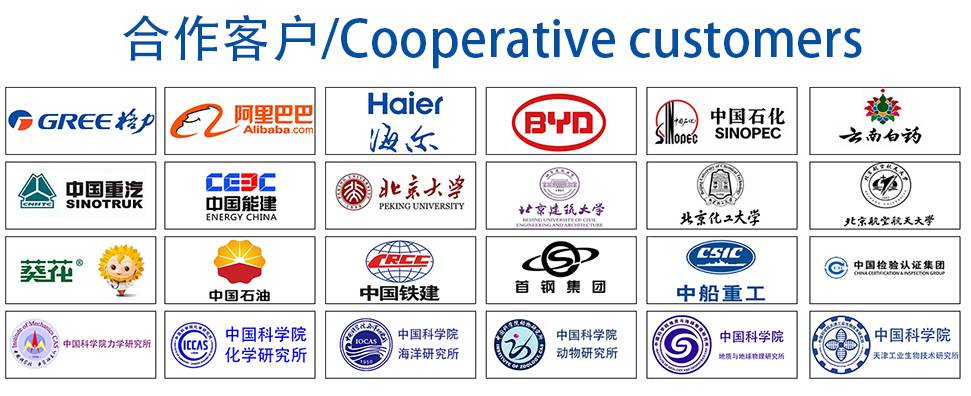