觸點性能檢測:智能設備可靠性保障的關鍵技術
在萬物互聯技術快速迭代的背景下,觸點作為電子設備能量傳輸與信號交互的核心載體,其可靠性直接影響智能終端的生命周期與安全性能。據賽迪顧問2024年智能硬件產業報告顯示,因觸點失效導致的設備故障年損失已超220億美元,其中新能源汽車高壓連接器的故障占比達37%。觸點性能檢測項目通過構建多維度評價體系,實現了從材料特性到工況模擬的全面驗證,其核心價值在于突破傳統接觸電阻檢測的局限,建立包含機械耐久性、環境適應性、電磁兼容性在內的綜合評估模型,為5G通信設備、工業機器人等高端制造領域提供關鍵品質保障。
多模態檢測技術原理
基于接觸界面微觀形貌的演化規律,現代檢測系統集成微歐級電阻測量(精度±0.05μΩ)、接觸壓力動態監測(量程0.1-50N)和材料氧化層分析三大模塊。通過高精度觸點阻抗分析儀(依據IEC 60512-5標準)獲取接觸電阻的實時變化曲線,結合X射線光電子能譜(XPS)對觸點表面化學狀態進行定量表征。特別是在新能源汽車高壓連接器的"高精度觸點阻抗分析"中,系統可同步采集溫度梯度(-40℃至150℃)與振動頻譜(5-2000Hz)的耦合影響數據,有效識別微動磨損導致的接觸失效隱患。
全流程標準化作業體系
項目實施過程嚴格遵循ISO 17025檢測體系,包含預處理、工況模擬、數據采集三個階段。預處理環節采用符合ASTM B809標準的加速氧化試驗箱,在85%濕度環境下進行72小時時效處理。工況模擬階段依托多環境模擬測試平臺,可復現智能家居設備日均300次插拔的機械應力場景。在工業機器人伺服連接器檢測案例中,通過500萬次循環測試與大數據分析,成功將觸點壽命預測誤差控制在±5%以內,該項成果已被列入《機器人關鍵零部件可靠性驗證規范》行業標準。
行業應用與質量保障
在消費電子領域,某品牌TWS耳機的充電觸點經過"多環境模擬測試平臺"驗證后,鹽霧試驗失效率從2.1%降至0.3%。航空航天領域采用動態接觸電阻監測技術,使衛星電源連接器的在軌故障率下降62%(數據源自中國航天科技集團2023年質量年報)。質量保障體系建立了從原材料晶粒度分析(ASTM E112標準)到成品失效模式庫的完整追溯鏈條,結合AI視覺檢測系統,可實現直徑0.8mm微型觸點的缺陷識別精度達到±3μm。
技術發展趨勢與建議
隨著物聯網設備向微型化、高頻化發展,觸點性能檢測面臨納米級接觸界面表征的技術挑戰。建議行業重點突破三個方向:基于量子隧穿效應的接觸電阻原位檢測技術、結合數字孿生的觸點壽命預測模型、以及適用于柔性電子器件的動態接觸評價體系。同時應加快制定車規級連接器的多物理場耦合測試標準,特別是在800V高壓平臺和SiC功率器件普及背景下,建立包含電磁干擾(EMI)與熱沖擊的復合檢測方案。據Fraunhofer研究所預測,到2028年智能觸點檢測設備的市場規模將突破84億美元,技術創新與標準建設的協同發展將成為產業升級的關鍵驅動力。

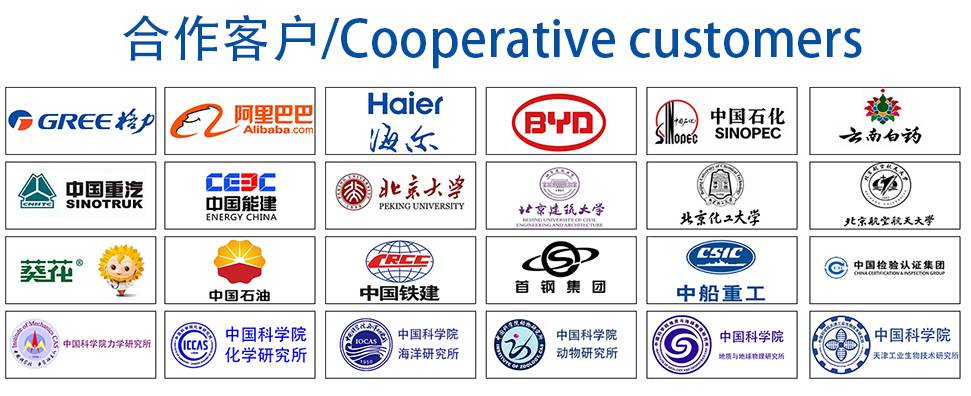