一、焊縫內(nèi)部缺陷的主要類型
- 氣孔(Porosity) 焊接過程中熔池中的氣體未及時逸出,形成空洞,多為圓形或橢圓形。
- 夾渣(Slag Inclusion) 焊渣或氧化物殘留在焊縫內(nèi)部,形態(tài)不規(guī)則,可能呈條狀或片狀。
- 未熔合(Lack of Fusion) 焊縫金屬與母材或焊層之間未完全熔合,界面處存在縫隙。
- 未焊透(Incomplete Penetration) 焊縫根部未完全熔透,導致連接強度不足。
- 裂紋(Crack) 冷裂紋、熱裂紋或延遲裂紋,危害性最大,易引發(fā)結(jié)構(gòu)斷裂。
二、焊縫內(nèi)部缺陷的核心檢測項目
1. 缺陷類型識別與定位
- 檢測技術(shù):
- 射線檢測(RT):利用X射線或γ射線穿透焊縫,通過底片或數(shù)字成像系統(tǒng)顯示缺陷的二維投影,適用于氣孔、夾渣等體積型缺陷。
- 超聲波檢測(UT):通過高頻聲波反射信號判斷缺陷的位置、大小和形狀,對未熔合、裂紋等線性缺陷敏感。
- 相控陣超聲檢測(PAUT):通過多晶片陣列實現(xiàn)聲束聚焦和掃查,可生成三維圖像,提升檢測精度。
- 檢測要點:
- 確定缺陷類型(如氣孔與夾渣的區(qū)分)。
- 記錄缺陷坐標(深度、長度、距焊縫中心距離)。
2. 缺陷尺寸量化
- 檢測技術(shù):
- 數(shù)字化射線檢測(DR):通過平板探測器生成數(shù)字圖像,結(jié)合軟件分析缺陷面積和周長。
- TOFD(衍射時差法):利用衍射波測量缺陷高度,適用于裂紋深度測量。
- 檢測標準:
- 依據(jù)ISO 17636(射線檢測)、ISO 10863(TOFD)等標準評估缺陷尺寸是否超限。
3. 缺陷危害性評估
- 檢測項目:
- 缺陷密集度分析:統(tǒng)計單位面積內(nèi)的氣孔數(shù)量,判定是否符合AWS D1.1等行業(yè)規(guī)范。
- 裂紋尖端應力分析:結(jié)合有限元模擬,評估裂紋擴展風險。
- 判定依據(jù):
- 根據(jù)ASME BPVC Section VIII或EN ISO 5817標準,將缺陷分為驗收級、修補級和拒收級。
4. 焊接工藝驗證
- 檢測內(nèi)容:
- 焊接參數(shù)(電流、電壓、速度)對缺陷形成的影響分析。
- 母材與焊材的相容性測試,避免因成分差異導致未熔合。
- 方法:
- 通過破壞性檢測(如切片金相分析)驗證無損檢測結(jié)果的準確性。
三、主流檢測技術(shù)對比及選擇建議
檢測技術(shù) | 適用缺陷類型 | 優(yōu)點 | 局限性 |
---|---|---|---|
射線檢測(RT) | 氣孔、夾渣、未焊透 | 直觀成像,永久記錄 | 輻射防護要求高 |
超聲波檢測(UT) | 裂紋、未熔合 | 靈敏度高,實時性強 | 需耦合劑,依賴操作經(jīng)驗 |
工業(yè)CT | 復雜三維缺陷 | 三維斷層成像,精度高 | 設(shè)備昂貴,速度慢 |
PAUT | 所有內(nèi)部缺陷 | 可編程掃查,效率高 | 設(shè)備復雜度高 |
- 常規(guī)檢測優(yōu)先選擇RT或UT;
- 高精度需求(如航空航天)選用工業(yè)CT或PAUT;
- 現(xiàn)場快速檢測可采用便攜式TOFD設(shè)備。
四、檢測標準與質(zhì)量控制
- 國際標準:
- ISO 17636(射線檢測)、ISO 11666(超聲波檢測)。
- ASME Section V(壓力容器焊縫檢測規(guī)范)。
- 質(zhì)量控制措施:
- 定期校準設(shè)備(如射線源強度、超聲探頭靈敏度)。
- 檢測人員需持有ASNT/EN 473等認證證書。
- 建立焊縫缺陷數(shù)據(jù)庫,用于工藝優(yōu)化和追溯。
五、發(fā)展趨勢
- 智能化檢測:AI算法輔助缺陷識別(如深度學習分析DR圖像)。
- 在線監(jiān)測系統(tǒng):焊接過程中集成聲發(fā)射(AE)傳感器,實時預警缺陷。
- 多技術(shù)融合:RT+UT+PAUT聯(lián)合檢測,提升覆蓋率與可靠性。
六、結(jié)語
上一篇:吸濕率檢測下一篇:鐵的質(zhì)量分數(shù)(以Fe計)檢測

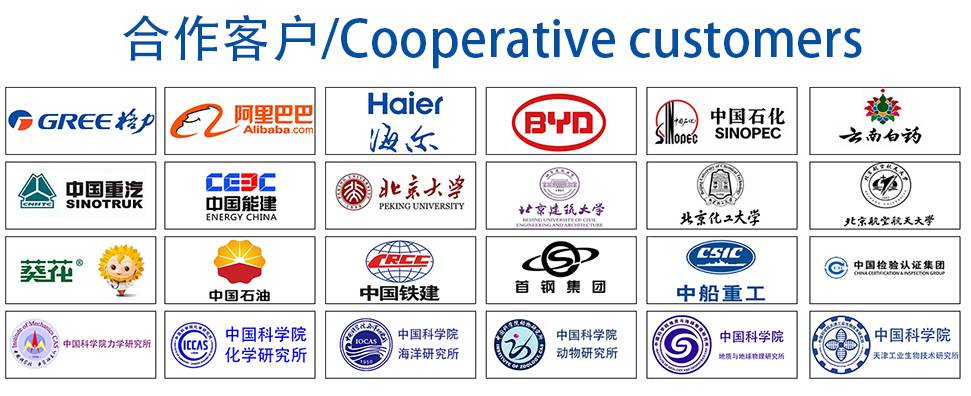
材料實驗室
熱門檢測
18
20
17
22
22
20
23
20
18
17
16
15
21
18
18
27
26
27
23
25
推薦檢測
聯(lián)系電話
400-635-0567