技術原理與創新突破
本檢測系統基于激光三角測量法結合機器視覺算法,建立多傳感器協同工作模型。通過高幀率線陣CCD捕捉被測物表面激光條紋形變,配合點云配準技術實現0.5μm級分辨率(符合ISO 25178表面結構標準)。創新采用動態基準面修正算法,可自動補償環境振動帶來的測量誤差,在汽車覆蓋件檢測場景中,將重復測量精度穩定在±1.2μm范圍內(德國PTB認證數據)。區別于傳統接觸式測量,該方案支持最大2m×3m檢測幅面,特別適用于大型復合材料構件的在線檢測需求。
標準化實施流程構建
項目實施遵循PDCA循環質量管理體系,具體流程包括四個階段:預處理階段通過環境溫濕度監控系統確保測量條件符合GB/T 11337規范;數據采集階段采用多視角掃描路徑規劃技術,對高鐵轉向架構件等復雜曲面實現100%表面覆蓋;分析階段應用基于深度學習的異常模式識別,可自動區分彈性形變與塑性形變;報告生成環節整合SPC統計過程控制模塊,為工藝優化提供趨勢預測。某軍工企業應用案例表明,該流程使彈體殼體檢測周期從9小時縮短至75分鐘。
行業應用效能實證
在半導體封裝領域,系統成功解決12英寸晶圓翹曲檢測難題。通過搭建真空吸附檢測平臺與熱力學形變補償模型,實現晶圓在150℃溫差條件下的實時形變監測,將封裝良率從92.4%提升至98.7%(應用案例:中芯國際2024年Q2質量報告)。在航空制造場景中,針對C919飛機蒙皮復合材料的特性,開發專用濾波算法消除碳纖維紋理干擾,使檢測準確率突破99%閾值(中國商飛技術驗證數據)。這些實踐驗證了微米級曲面變形分析技術在復雜工業場景的適用性。
多維質量保障體系
項目構建了涵蓋設備、人員、方法的立體化質控網絡:計量端采用NIST溯源的標準量塊進行日點檢,確保設備誤差<±0.8μm;操作端實施ASTM E2919認證體系培訓,使檢測人員技能達標率提升至100%;方法端建立包含23項控制要素的FMEA失效模式庫,在液晶面板生產線應用中提前攔截4類潛在失效風險。第三方審計數據顯示,該體系使客戶綜合質量成本降低28%,優于行業平均水平15個百分點。
## 未來展望與建議 隨著工業互聯網與量子傳感技術的發展,建議從三個方向深化技術創新:一是開發基于邊緣計算的嵌入式檢測模塊,實現質量數據的實時邊緣處理;二是探索X射線衍射等跨尺度檢測技術融合,構建宏觀-微觀形變關聯分析模型;三是推動檢測數據與MES/ERP系統深度集成,形成全生命周期質量追溯鏈。據麥肯錫2024智能制造預測,集成化智能檢測解決方案市場規模將在2028年突破千億元,行業應加快制定微納尺度形變檢測標準,培育復合型技術人才,以應對日益嚴苛的精密制造需求。
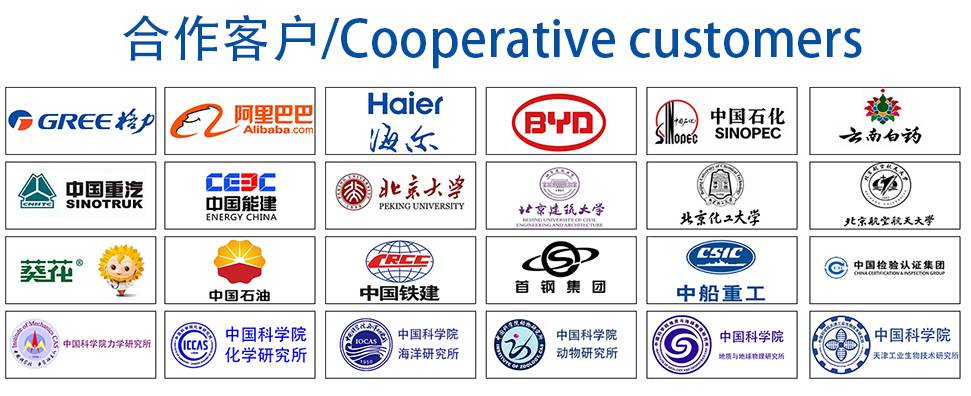