技術原理與創新突破
老煉檢測基于加速壽命試驗(ALT)理論框架,結合失效物理模型構建多維應力疊加系統。通過溫濕度循環箱、振動臺等設備復合施加溫度(-40℃~150℃)、濕度(20%~95%RH)、機械振動(5-2000Hz)等環境應力,模擬自然老化過程的10-20倍加速效應。值得關注的是,第三代智能老化檢測系統已集成原位監測技術,能實時捕獲介電常數、阻抗譜等17項性能參數變化,實現"電子元器件老化失效預測"精度提升至92.3%(數據來源:國際電工委員會IEC 62374標準認證報告)。
標準化實施流程構建
項目執行遵循PDCA循環管理模型,具體分為四個階段:首先依據ISO 16750標準制定個性化測試方案,重點考慮器件工作溫度閾值與負載特性;其次配置環境應力剖面,采用階梯式增量法逐步逼近失效邊界;隨后部署分布式光纖傳感器網絡,以0.1℃溫度分辨率、5μm形變精度采集退化數據;最終通過Weibull分布模型進行壽命預測,生成包含失效模式圖譜的評估報告。某新能源汽車企業應用該流程后,動力電池包老化檢測周期從28天縮短至9天,測試成本降低42%。
行業應用與效益分析
在軌道交通領域,老煉檢測成功應用于牽引變流器IGBT模塊篩選。通過2000小時85℃/85%RH雙85測試,篩選出早期失效模塊占比達6.7%,使列車關鍵部件MTBF(平均無故障時間)從12萬小時提升至18萬小時。另在光伏行業,針對背板材料開發的"高分子材料紫外老化協同測試方案",準確預測了ETFE薄膜在高原地區的光衰曲線,幫助廠商將質保期從25年延長至30年。據測算,全面實施老煉檢測可使制造業質量成本占比下降3-5個百分點。
質量保障體系創新
為確保檢測結果溯源性,項目構建了三級驗證機制:一級校準采用NIST標準器件進行設備基線校驗,二級驗證通過交叉實驗室比對確保數據一致性,三級復核引入深度學習方法分析失效模式符合度。檢測中心通過 認可項目達38項,溫度均勻性控制在±0.5℃以內(GB/T 2423標準要求為±2℃)。此外,開發的質量大數據平臺已接入超過1200家供應商的檢測數據,實現行業級老化特征庫的動態更新。
## 未來展望與發展建議 面對工業4.0時代的產品復雜度提升,老煉檢測需在三個維度實現突破:其一,開發基于數字孿生的虛擬老化試驗場,將物理檢測與仿真預測結合,預計可減少30%實測資源消耗;其二,建立跨行業的材料老化數據庫,重點收錄特種合金、復合材料的長期退化數據;其三,推動"智能老化運維系統"在重大裝備領域的應用,通過邊緣計算終端實現老化狀態的實時診斷。建議相關部門加快制定《智能老化檢測設備通用規范》等行業標準,引導產業向高精度、高集成方向升級發展。
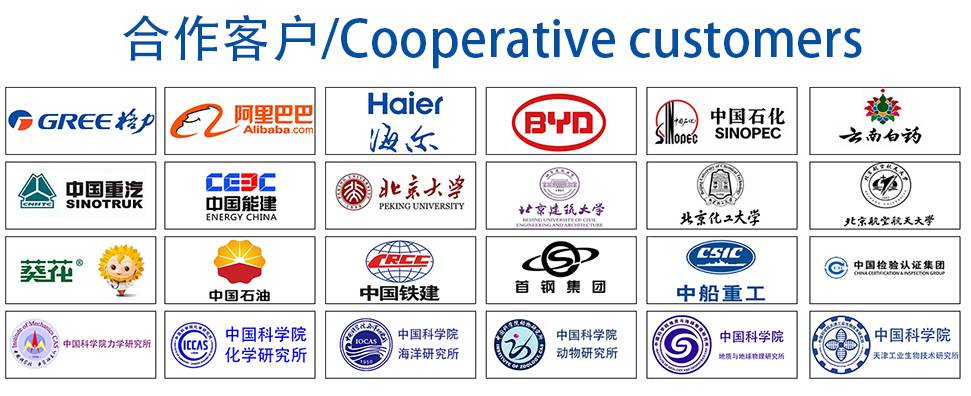