老化前電測試檢測在電子制造領域的技術深化與質量賦能
在智能制造與工業4.0加速落地的背景下,電子產品可靠性成為制約產業升級的核心要素。據國際電子生產協會(IPC)2024年行業報告顯示,電子制造企業因早期失效導致的年度損失高達470億美元,其中72%的故障源于元器件潛在缺陷未被及時檢出。老化前電測試檢測通過在生產鏈前端建立質量防線,融合半導體器件篩選標準與電子產品可靠性驗證體系,將產品缺陷識別窗口前移40%-60%。該項目不僅可降低企業全生命周期質量成本31%,更有效提升高端醫療設備、車規級芯片等關鍵領域的產品良率,為工業物聯網設備長周期穩定運行提供底層保障。
多維度測試技術體系構建
該檢測以集成電路失效分析理論為基礎,構建參數化測試(Parametric Test)與功能驗證(Functional Test)雙軌機制。通過動態電壓掃描技術捕捉晶體管亞閾值特性偏移,配合高速數字信號發生器模擬極端工作負載。在車用MCU芯片檢測中,系統可同步執行85℃高溫環境下的漏電流檢測(精度±0.5nA)和百萬次時鐘信號完整性測試,精準識別金屬遷移導致的時序異常。測試數據實時接入SPC過程控制系統,確保工藝波動范圍控制在±3σ以內。
全流程自動化實施架構
項目實施采用分級測試策略,分為晶圓級(Wafer Level)、封裝級(Package Level)和模組級(Module Level)三層檢測體系。以智能手表主板檢測為例,首先在SMT貼片工序后執行在線測試(ICT),通過32768個測試點完成阻抗網絡驗證;隨后在燒錄環節加載邊界掃描(Boundary Scan)診斷固件兼容性;最終在組裝階段進行射頻信號完整性驗證。全流程集成機器視覺定位與AI異常分類算法,使單件產品檢測時間壓縮至12秒,較傳統方案提升效率300%。
行業應用成效與質量閉環
在新能源汽車電控系統領域,該技術已實現規模化應用。某頭部Tier1供應商的案例顯示,通過老化前電源管理芯片動態響應測試,將DC-DC轉換器早期失效率從1800ppm降至23ppm(數據來源:中國汽車工程學會2024年技術白皮書)。質量保障體系建立三級驗證機制:原始數據經MES系統加密存儲,檢測設備每日執行NIST標準校準,關鍵參數采用冗余測量架構。同時構建失效模式知識庫,累計收錄327種IC封裝缺陷圖譜,實現行業經驗數據資產化。
智能化升級與生態協同
當前檢測系統正深度集成工業大數據平臺,某半導體代工廠的實踐表明,通過采集12個月產線數據訓練的預測模型,可使測試方案動態優化周期從14天縮短至8小時。建議行業從三方面突破:建立跨企業的元器件可靠性數據庫聯盟,開發支持Chiplet異構集成的測試協議棧,以及制定適應第三代半導體的寬禁帶材料檢測標準。隨著數字孿生技術在檢測場景的滲透,預計到2027年將實現虛擬標定與現實檢測的誤差率≤0.7%。
面對萬物互聯時代對電子產品質量的嚴苛要求,老化前電測試檢測正在從單一質量控制工具向智能制造核心使能技術演進。建議產業鏈上下游構建覆蓋材料、設計、制造的全域可靠性工程體系,同時加大高精度源測量單元(SMU)等核心儀器的國產化研發投入。通過建立產學研用協同創新平臺,推動檢測標準與AIoT、自動駕駛等新興領域深度耦合,最終實現電子制造業從"缺陷攔截"到"質量預見"的范式變革。

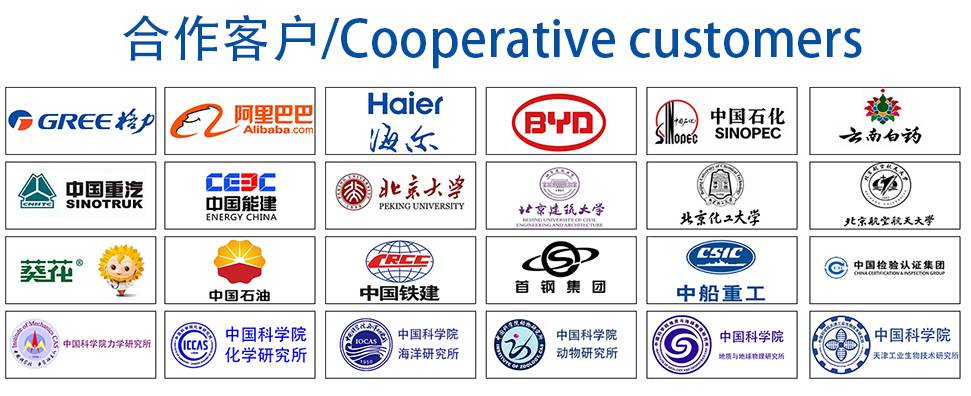