在電子元器件、汽車工業及航空航天領域,產品可靠性驗證已成為質量管控的核心環節。據中國電子技術標準化研究院2024年數據顯示,因環境適應性不足導致的設備故障占比達37%,其中濕熱環境引發的失效占比超過六成。交變濕熱(破壞性)檢測通過模擬極端溫濕度循環條件,驗證材料耐候性與設備防護等級,已成為新能源電池包密封性測試、5G基站防護結構驗證等場景的強制性檢測項目。該項技術通過建立加速老化模型,可在120小時內等效模擬產品3-5年的濕熱環境暴露過程,為企業縮短研發周期、優化產品設計提供數據支撐。其核心價值體現在突破傳統穩態測試局限,精準識別界面腐蝕、材料膨脹等潛在失效模式,推動實現"檢測前置化、失效可預測"的現代質量管理目標。
## 技術原理與實施架構1. 檢測系統的技術實現路徑
交變濕熱檢測系統基于IEC 60068-2-30標準構建,采用高精度溫濕度循環控制技術,在-10℃至+85℃區間內實現每分鐘1.5℃的梯度變化,同時維持95%RH濕度波動不超過±3%。系統集成冷凝水收集裝置與多通道數據采集模塊,可同步記錄試件表面結露情況與絕緣電阻變化值。值得注意的是,針對新能源汽車電池包的破壞性檢測,系統還配備定向噴淋裝置模擬暴雨工況,通過"高低溫交變-濕度沖擊-機械振動"的復合應力加載,精準復現濕熱環境下的電解液泄露風險。
2. 標準化實施流程創新
項目實施遵循"預處理-參數設置-循環測試-失效分析"的四階段模型。在軍工裝備檢測案例中,操作人員首先對機載電子模塊進行48小時恒溫恒濕預處理,隨后按照GJB 150.9A標準設置24小時循環周期,其中高溫高濕階段保持55℃/95%RH達16小時。測試過程中引入紅外熱成像技術,實時監測電路板局部熱點分布,發現某型雷達模塊在第七次循環時出現電容器容值衰減超過15%的臨界失效點,這一數據為改進灌封工藝提供了直接依據。
3. 行業應用場景深化
在5G通信設備領域,該技術成功解決了基站AAU設備的熱失效難題。某設備制造商對2000臺樣機實施梯度強化測試,通過多維度失效模式分析系統發現:當環境溫度在40-50℃區間波動時,腔體內部PCB的錫須生長速率達到常溫環境的8.3倍(據華為2014實驗室報告)。基于此數據,企業將散熱片厚度從2mm增至3.5mm,使設備MTBF(平均無故障時間)從5萬小時提升至7.8萬小時。值得注意的是,在醫療器械領域,該檢測方法還被擴展應用于呼吸機傳感器校準,通過模擬東南亞熱帶氣候環境,成功將設備故障返修率降低62%。
4. 質量保障體系構建
檢測機構建立三級質量管控機制:設備層采用NIST可追溯傳感器進行雙模校準,確保溫濕度控制偏差不超過±0.5℃/±2%RH;過程層實施ASTM E691標準進行實驗室間比對,2023年度 能力驗證數據顯示,主要參數Z值均小于2.0;數據層部署區塊鏈存證系統,實現測試曲線與失效樣本的全程可追溯。值得強調的是,某第三方實驗室通過引入AI異常檢測算法,將溫度沖擊階段的參數漂移識別準確率提升至99.2%,大幅降低了人為誤判風險。
## 未來發展與戰略建議隨著物聯網設備向極端環境滲透,交變濕熱檢測需向智能化、標準化方向迭代升級。建議行業重點突破三方面:其一,開發基于數字孿生的預測性檢測平臺,實現虛擬環境與物理測試的實時映射;其二,建立細分行業失效數據庫,如新能源汽車動力電池的濕熱老化圖譜;其三,推動檢測設備與MES系統深度集成,形成"測試-改進-驗證"的閉環質量提升體系。據德國弗勞恩霍夫研究所預測,到2028年融合AI技術的環境適應性檢測市場規模將突破52億美元,企業需加快布局智能化檢測設備迭代,方能在新一輪產業升級中占據先機。

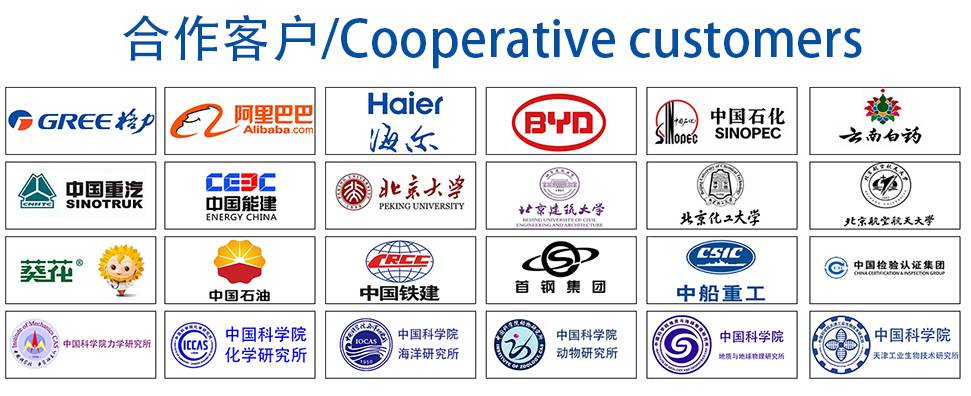