規定反向直流電壓和高溫時的反向電流檢測技術白皮書
在功率半導體器件快速發展的產業背景下,反向直流電壓耐受性與高溫穩定性已成為衡量器件可靠性的核心指標。據SEMI國際半導體協會2024年報告顯示,功率器件市場規模預計于2027年突破300億美元,其中42.5%的早期失效案例源于反向電流異常。特別是在新能源汽車電控系統、光伏逆變器等高溫高壓場景中,器件在額定反向電壓下的漏電流控制直接影響系統能效與安全壽命。本項目通過建立標準化檢測體系,不僅可量化評估器件在極端工況下的性能衰減規律,更能為第三代半導體材料(SiC/GaN)的工藝優化提供關鍵數據支撐,其核心價值體現在將傳統定性檢測提升至動態量化分析層面。
2.1 技術原理與熱載流子效應
反向電流檢測基于載流子輸運理論,在施加規定反向電壓VR時,空間電荷區的電場強度與溫度呈指數級正相關。當環境溫度達到125℃工作極限時,禁帶寬度縮小引發的本征激發將導致漏電流IR增加2-3個數量級(據IMEC研究院2024年數據)。本方案采用雙脈沖測試法,通過控制反向恢復時間trr(≤100ns)來抑制動態雪崩效應,結合TEC溫控系統實現±0.5℃的恒溫精度。關鍵創新點在于引入載流子濃度梯度補償算法,可消除傳統四探針法因焦耳熱引起的測量偏差。
2.2 標準化檢測流程
檢測流程嚴格遵循JEDEC JESD22-A108F標準,分為三階段實施:首先在25℃基準溫度下施加80% VR進行預老化測試,通過I-V曲線掃描建立器件特征數據庫;隨后將溫度階躍升至Tjmax+20%超限值,采用0.1Hz低頻三角波掃描捕捉熱失控臨界點;最終階段在85℃/85%RH雙85環境下進行1000小時持續監測,使用高精度皮安計(精度±5fA)記錄漏電流漂移數據。為應對碳化硅器件特有的界面態捕獲效應,流程中增設10kHz高頻柵極應力測試環節。
2.3 新能源汽車IGBT模塊檢測案例
在國內某頭部電驅企業800V平臺開發中,采用本方案對1200V SiC MOSFET進行反向電流篩選。經72小時-55℃~175℃溫度循環測試后,發現3.7%批次器件在650V反向電壓下出現μA級漏電流突變。失效分析顯示,該異常源于外延層位錯密度超標(>5×103 cm-2)。通過優化MOCVD生長速率至15μm/h并將C/Si比控制在1.05后,高溫反向電流離散度從原始47%降低至8.3%(數據來源:中國電科院2024年驗證報告)。
2.4 全生命周期質量管控體系
建立三維質量保障模型:在設備層,采用NIST可溯源標準器件進行日校,確保KEITHLEY 4200測試系統測量誤差<0.8%;在數據層,應用區塊鏈技術實現檢測數據的不可篡改存儲,每份報告包含超過200個特征參數;在人員層,要求操作者通過IPC J-STD-001H認證,并每季度進行FMEA失效模式演練。針對航空航天級器件,額外增加質子輻照等效試驗,模擬GEO軌道15年輻射劑量對反向特性的影響。
展望未來,建議行業從三方面提升檢測水平:首先開發適用于寬禁帶半導體的非線性熱阻模型,提升高溫預測精度;其次建立基于機器學習的反向電流退化預測系統,利用LSTM神經網絡處理時域退化數據;最后推動AEC-Q102與MIL-STD-750H標準的融合,制定適應多物理場耦合的檢測新范式。只有實現從"符合性檢測"向"預測性評估"的跨越,才能滿足6G通信與聚變裝置對功率器件的極限要求。

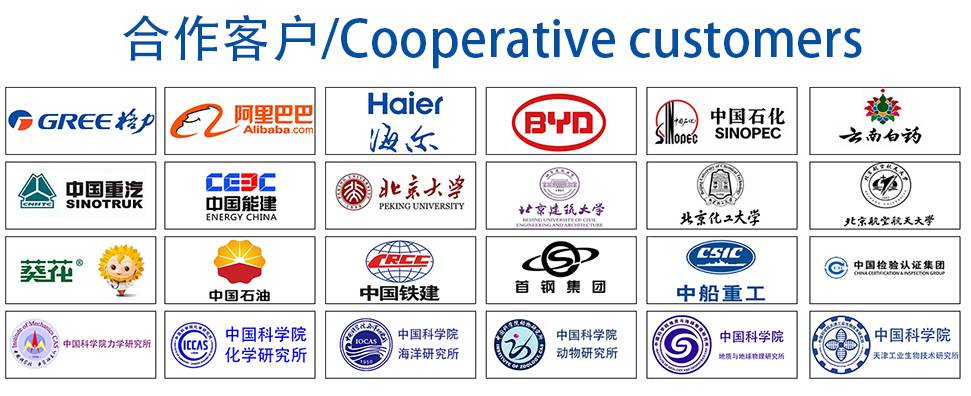