一、電池組檢測的核心目標
- 性能評估:容量、能量密度、功率輸出能力等是否達標;
- 安全驗證:電池組在極端條件下的穩定性及抗風險能力;
- 壽命預測:循環次數、老化速率等壽命指標的量化分析;
- 一致性檢查:電芯間電壓、內阻、溫度等參數的均衡性。
二、核心檢測項目分類
1. 電性能檢測
- 容量測試: 通過充放電循環測定電池組在不同倍率下的實際容量(Ah),驗證是否滿足標稱值(如1C放電至截止電壓)。
- 內阻測試: 采用交流阻抗法或直流脈沖法測量電池組整體內阻,評估其能量轉換效率及發熱特性。
- 循環壽命測試 模擬實際使用場景,進行數百至數千次充放電循環,記錄容量衰減曲線(如容量衰減至80%時判定壽命終止)。
- 自放電率檢測 電池組靜置7~30天后測量電壓下降幅度,判斷是否存在微短路或電解液分解問題。
- 動態響應測試 模擬車輛加速、制動等工況,檢測電池組的瞬時功率輸出能力及電壓波動范圍。
2. 安全性能檢測
- 過充/過放測試 將電池組充電至1.5倍額定電壓(或放電至0V),監測是否發生起火、爆炸、電解液泄漏。
- 短路測試 外部強制短路(<5mΩ)模擬電池組極端故障,記錄溫升速率及保護裝置響應時間(如熔斷器動作時間≤1s)。
- 熱濫用測試 將電池組置于130~150℃高溫環境中,觀察熱失控傳播情況及隔熱設計有效性。
- 針刺/擠壓測試(機械觸發安全) 使用鋼針刺穿單體電芯或施加1kN~10kN壓力,驗證電池組結構抗機械破壞能力。
- 絕緣耐壓測試 檢測電池組外殼與電極間絕緣電阻(≥100MΩ)及耐壓強度(如1000V DC持續1分鐘無擊穿)。
3. 機械性能檢測
- 振動測試 依據GB/T 31467.3標準,施加X/Y/Z三軸隨機振動(頻率5Hz~200Hz),檢測結構件松動或連接失效。
- 沖擊測試 模擬交通事故沖擊(如50g加速度、6ms脈沖),檢查電池組固定支架及內部焊接點完整性。
- 跌落測試 從1~2米高度自由跌落至剛性地面,評估外殼變形程度及內部電芯位移風險。
4. 環境適應性檢測
- 高低溫循環測試 在-40℃至+85℃間循環切換,驗證電池組在極端溫度下的充放電性能及密封性。
- 濕熱測試 將電池組置于85℃、85%RH環境中48小時,檢測絕緣材料老化及金屬部件銹蝕情況。
- 低氣壓測試 模擬海拔5000米環境(約54kPa氣壓),評估電解液揮發及氣密性。
三、檢測方法與標準依據
-
- 高精度電池測試系統(如Digatron、Arbin);
- 環境試驗箱(溫度/濕度/氣壓控制);
- 數據采集模塊(電壓、溫度、壓力傳感器);
- 安全防護設施(防爆艙、滅火系統)。
-
- 國際標準:IEC 62660(動力電池)、UL 1642(鋰電池安全);
- 國家標準:GB/T 31484(循環壽命)、GB 38031(電動汽車安全要求);
- 行業規范:UN 38.3(運輸安全)、SAE J2464(濫用測試)。
四、檢測流程與結果分析
- 流程設計: 預檢(外觀/電壓一致性)→ 分階段測試(電性能→安全→環境)→ 數據分析→ 出具報告。
- 關鍵指標判定:
- 合格標準:容量≥95%標稱值、溫升≤20℃(1C放電)、無泄漏/爆炸;
- 風險預警:單體電壓差異>50mV、循環容量衰減率>0.1%/次。
五、行業趨勢與新技術
- 智能診斷技術: 基于BMS數據的在線健康狀態(SOH)監測,結合AI算法預測電池組剩余壽命。
- 無損檢測(NDT): 采用X射線斷層掃描(CT)或超聲波成像檢測內部結構缺陷。
- 快充兼容性測試: 針對800V高壓平臺電池組,驗證4C以上超充下的熱管理效能。
六、結語
轉成精致網頁

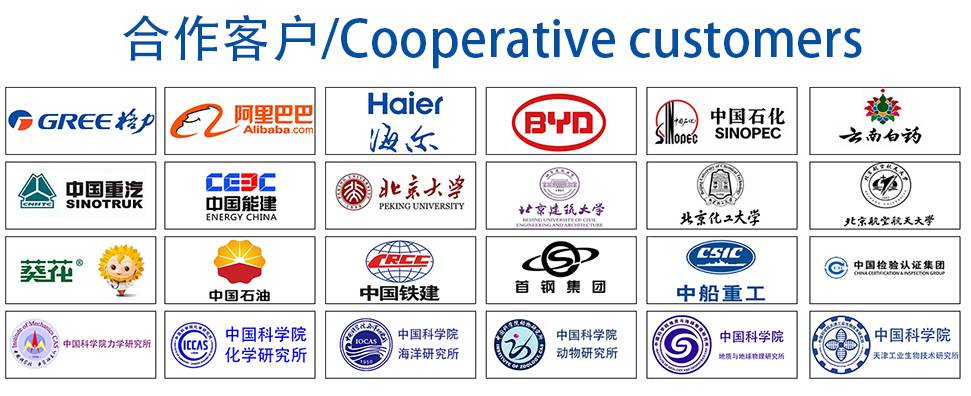
材料實驗室
熱門檢測
22
18
19
27
31
18
28
28
22
27
27
30
29
22
36
27
27
32
24
21
推薦檢測
聯系電話
400-635-0567