管線用鋼制平板閘閥檢測的重要性與流程
管線用鋼制平板閘閥作為石油、天然氣、化工等工業領域中管道系統的關鍵控制設備,其性能直接關系到介質輸送的安全性、密封性和可靠性。由于長期承受高壓、腐蝕性介質及頻繁啟閉的工況,閘閥可能因材料疲勞、密封失效或結構變形引發泄漏甚至事故。因此,定期開展科學、系統的檢測是保障設備運行安全的核心環節。通過檢測可及時發現潛在隱患,延長閥門使用壽命,降低運維成本,同時滿足行業標準(如API 6D、GB/T 19672等)的合規性要求。
核心檢測項目及技術要求
1. 材質成分與力學性能檢測
通過光譜分析儀、拉伸試驗機等設備,驗證閥體、閘板、閥桿等核心部件的材料是否符合設計標準(如ASTM A105、A182等)。重點檢測碳鋼、合金鋼的化學成分及抗拉強度、硬度、沖擊韌性等力學性能,確保材料在高壓和低溫環境下的穩定性。
2. 密封性能試驗
采用低壓氣密性試驗(0.6MPa)和高壓水壓試驗(1.5倍公稱壓力)結合滲透檢測法,驗證閘閥在全開/全閉狀態下的密封性。重點關注閘板與閥座接觸面的泄漏率,確保閥門在長期使用后仍能達到API 598規定的A級或B級密封標準。
3. 操作扭矩與靈活性測試
使用扭矩扳手或電動執行器模擬實際工況,測量閥門啟閉過程中的最大扭矩值。對比設計參數,分析閥桿與填料函的摩擦系數、閘板導向結構的磨損情況,確保操作力矩在允許范圍內且無卡阻現象。
4. 殼體強度與耐壓試驗 對閥體進行1.5倍公稱壓力的靜水壓試驗,持續保壓時間不少于10分鐘。通過應變儀監測閥體變形量,結合目視檢查確認無滲漏、裂紋或永久性形變,驗證閥門在極端壓力下的結構完整性。
專項檢測與功能性評估
5. 耐腐蝕性檢測
針對含硫、酸性介質等特殊工況,需進行晶間腐蝕試驗(如ASTM A262)、鹽霧試驗或硫化氫應力腐蝕開裂(SSC)測試。通過金相顯微鏡觀察材料微觀組織變化,評估閥門在腐蝕環境下的長期服役能力。
6. 尺寸精度與幾何公差檢測
使用三坐標測量儀、內徑千分尺等工具,檢測閥座內徑、閘板厚度、閥桿直線度等關鍵尺寸。公差范圍需滿足ISO 5208標準,確保閥門與管道系統的匹配精度及密封副的吻合度。
7. 功能性全周期試驗
在模擬工況下進行至少500次啟閉循環測試,記錄每次操作的密封性能和扭矩變化。結合振動測試與疲勞壽命分析,綜合評估閥門的耐久性及可靠性指標。
檢測結果分析與維護建議
檢測完成后需形成包含數據對比、缺陷定位、失效模式分析的綜合報告。對于密封面劃痕、閥桿微變形等可修復問題,建議采用激光熔覆或機械研磨工藝處理;若發現材料劣化或結構性損傷,則需立即更換部件。同時推薦建立周期性檢測檔案,結合工況調整維護頻率,實現閥門的全生命周期管理。

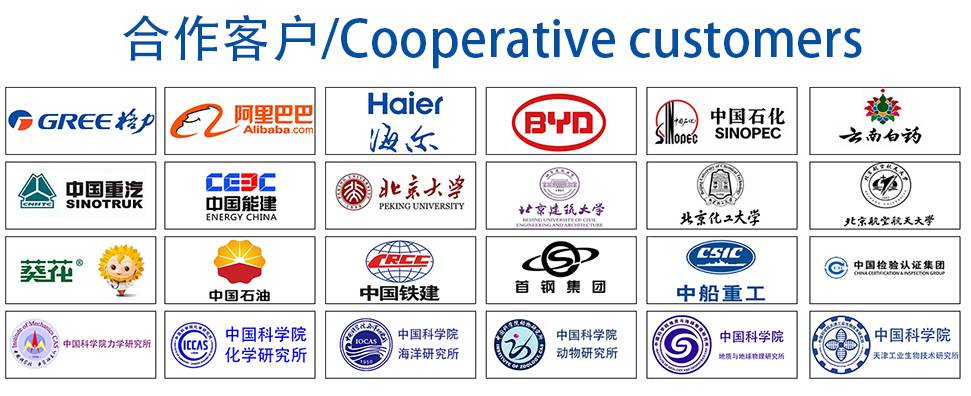