抽油機檢測的重要性與流程概述
抽油機作為石油開采的核心設備,其運行狀態直接影響油田生產效率和安全性。在長期高負荷、復雜工況下,抽油機易出現機械磨損、動力系統故障、平衡失調等問題,若不及時檢測維護可能導致停機事故甚至安全隱患。因此,定期開展抽油機檢測是保障油田穩定生產、延長設備壽命的重要手段。檢測工作需覆蓋機械結構、動力傳輸、安全防護等關鍵環節,結合國家標準(如SY/T 5044-2020)和智能化監測技術,形成系統性評估與優化方案。
核心檢測項目及技術要求
1. 機械系統檢測:重點檢查曲柄平衡塊位移量、連桿銷軸磨損量、支架垂直度偏差等指標。通過激光對中儀測量游梁與支架的同軸度,使用超聲波探傷儀檢測減速箱齒輪裂紋,確保誤差控制在±0.5mm/m范圍內。
2. 動力系統檢測:包括電機絕緣電阻測試(≥500MΩ)、減速箱油溫監測(≤85℃)、皮帶張緊力檢測(符合設備標定值±10%)。需采用熱成像儀分析電機繞組溫度分布,預防局部過熱故障。
3. 安全防護裝置檢測:驗證過載保護裝置的觸發閾值(額定載荷的110%-125%)、剎車系統響應時間(≤3秒)、防爆電氣設備完整性。特別在含硫油氣田,需增加防腐層厚度檢測和H2S濃度監測。
智能化檢測技術的應用
新型檢測方案融合物聯網傳感器和AI算法,通過在懸繩器安裝張力傳感器(精度±1%FS)、在曲柄軸加裝振動監測模塊(采樣頻率≥5kHz),實現實時數據采集。結合數字孿生技術構建設備三維模型,可預測剩余使用壽命(RUL)誤差率<15%。
檢測周期與結果處理規范
常規檢測應每季度開展1次,高含水油井需縮短至每月檢測。檢測報告須包含異常振動頻譜分析、能耗對比曲線(kW·h/噸油)、關鍵部件剩余壽命評估等內容。對于平衡度偏差>10%的機組,應優齊全行配重調整;減速箱鐵譜分析發現異常磨損顆粒時,需立即更換潤滑油并跟蹤監測。
通過系統化檢測與預防性維護,可降低抽油機故障率40%以上,提升系統效率5-8個百分點。建議油田企業建立數字化檢測平臺,實現設備全生命周期管理,為智慧油田建設奠定技術基礎。

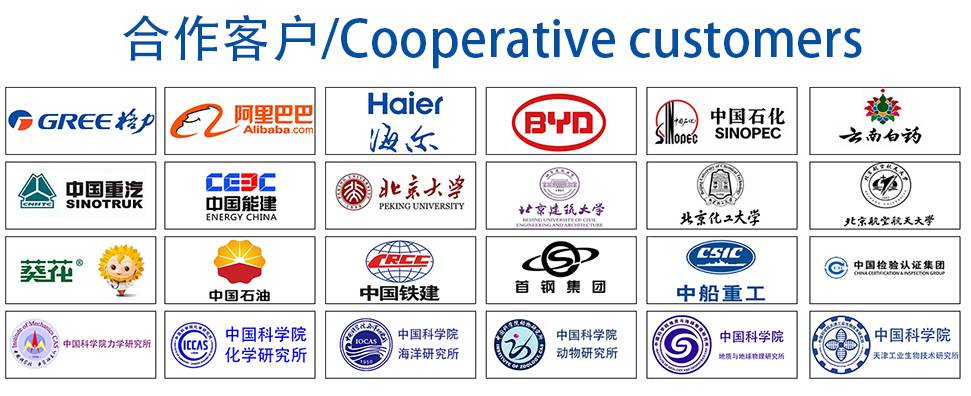