塑料注射成型收縮率檢測
實驗室擁有眾多大型儀器及各類分析檢測設備,研究所長期與各大企業(yè)、高校和科研院所保持合作伙伴關系,始終以科學研究為首任,以客戶為中心,不斷提高自身綜合檢測能力和水平,致力于成為全國科學材料研發(fā)領域服務平臺。
立即咨詢塑料注射成型收縮率檢測
塑料注射成型收縮率的背景和重要性
塑料注射成型是一種廣泛應用于制造業(yè)的核心技術,通過將熱塑性塑料加熱至熔融狀態(tài),然后注入到冷卻模具中以制造復雜而精確的部件。然而,在塑料注射成型中,收縮率是一個至關重要的參數(shù),因為它會直接影響成品的尺寸精度和質量。了解和控制收縮率對于絕大多數(shù)潛在應用和實現(xiàn)產(chǎn)品規(guī)格至關重要。
塑料的收縮特性
收縮率是在塑料冷卻固化的過程中,體積減小的程度。該現(xiàn)象主要由于兩個因素導致:第一,熱塑性塑料在從熔融狀態(tài)冷卻到固態(tài)時,分子鏈的移動和凝固導致體積縮小;第二,模具墻壁對塑料施加的壓力在成型過程中的變化。不同類型的塑料,其收縮率都不盡相同,甚至在同一種塑料中,由于工藝條件不同也會導致不同的收縮率。
例如,結晶性塑料如聚乙烯(PE)和聚丙烯(PP),其分子有序排列導致較高的體積收縮。而無定形塑料如聚苯乙烯(PS)和聚碳酸酯(PC),由于沒有結晶過程,其收縮率相對較低。
收縮率的測量方法
為了檢測和測量塑料注射成型的收縮率,通常采用以下幾個步驟。首先,通過測量從模具中取出的塑料件的實際尺寸,并與模具原設計尺寸比較。其次,通過對幾何尺寸與設計尺寸的偏差計算出塑料的收縮率,其通常表達為百分比形式,計算公式為:
收縮率 = [(模具尺寸 - 零件尺寸) / 模具尺寸] × 100%
這種方法可以為工廠提供非常直觀和有效的制造質量控制。同時,利用計算機模擬工具也可以對模具設計和熔融流動行為進行預測,并對模具進行適當?shù)难a正。
影響收縮率的因素
影響塑料注射成型收縮率的因素眾多,其中,材料特性、模具設計和成型工藝參數(shù)都起著非常重要的作用。首先,不同的塑料材料因其分子結構和熱性能的不同,會表現(xiàn)出不同的收縮率。因此,在選擇塑料材料時,需要充分考慮其固有收縮特性。其次,模具設計的精度和復雜度也直接影響收縮率。模具應該確保零件的各個部分均勻冷卻,以避免不均勻的收縮和變形。
成型工藝中的參數(shù)如模溫、注塑壓力、冷卻時間和料溫等也對收縮率有顯著影響。通常,較高的模溫和注塑壓力會導致較低的收縮率,而足夠的冷卻時間可以確保零件穩(wěn)定成形,減少收縮不均勻的風險。
如何控制和優(yōu)化收縮率
為了有效控制塑料注射成型中的收縮率,企業(yè)可采用一些優(yōu)化措施。例如,選擇適當?shù)牟牧喜⑦M行工藝參數(shù)調整,以減少因材料收縮特性而產(chǎn)生的影響。優(yōu)化模具設計,提高模具的精度和冷卻效率,也可以顯著降低收縮問題。
此外,工廠可以引入齊全的計算機輔助設計(CAD)和計算機輔助工程(CAE)技術,通過軟件仿真工具進行流動分析與模具填充模擬,最終優(yōu)化模具設計和成型參數(shù),以達到最佳收縮率控制目的。這種方法不僅降低了試制成本及周期,而且確保了產(chǎn)品質量的穩(wěn)定。
與未來發(fā)展
塑料注射成型收縮率檢測不僅是質量控制的重要手段,也是提高生產(chǎn)效率、確保產(chǎn)品性能的關鍵環(huán)節(jié)。隨著現(xiàn)代科技的發(fā)展和市場需求的變化,對塑料成型收縮率的精確控制顯得尤為重要。未來,隨著更加智能化的制造技術和高精度測量工具的引入,注塑成型的收縮率控制將向著更加全面、精準、智能化的方向發(fā)展。這將不僅提高產(chǎn)品質量,還會為可持續(xù)生產(chǎn)和齊全制造增添新的動力。

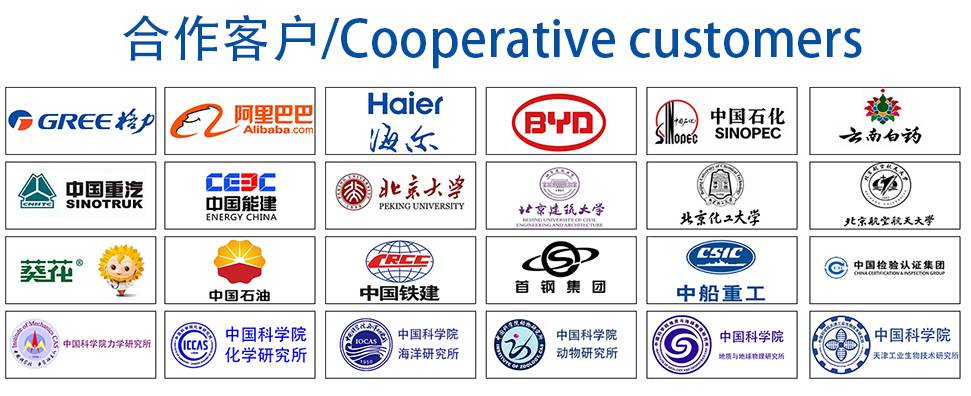