隨著含氟聚合物在電子封裝、特種涂料等領域的廣泛應用,三氟氯氰聚酯作為關鍵材料,其安全性評估成為行業關注焦點。據中國化工研究院2024年數據顯示,含氟聚合物市場規模已達520億美元,其中三氟氯氰聚酯類材料占比超過18%。該材料在高溫工況下可能釋放含氯氟烴類物質,其分解產物中三氟氯甲烷(CFC-13)的臭氧消耗潛能值(ODP)達1.0,顯著高于《蒙特利爾議定書》管控標準。本項目通過建立精準檢測體系,既保障了"電子封裝材料有害物質篩查"的合規性,又實現了"高溫工況下材料穩定性評估"的技術突破,為全產業鏈提供從原料篩選到成品驗收的閉環解決方案。
檢測技術原理與方法創新
基于熱裂解-氣相色譜/質譜聯用(Py-GC/MS)技術,本檢測方案采用梯度升溫裂解模式,在氦氣載流下實現材料分解產物的定向捕獲。通過優化裂解溫度區間(300-650℃),可精準識別出含氯氟烴、六氟丙烯二聚體等23種特征產物。相較于傳統FTIR光譜法,該方法將檢測靈敏度提升至0.01ppm,滿足歐盟REACH法規附件XVII的限量要求(0.1% wt/wt)。針對"電子元器件微型化"帶來的痕量檢測挑戰,創新性引入固相微萃取(SPME)前處理技術,使樣品制備效率提升40%以上。
標準化實施流程構建
檢測流程嚴格遵循ISO 12000:2023《含氟聚合物分解產物測定》標準,形成五階段質量控制體系:①現場采樣執行四分法取樣,確保樣本空間代表性;②實驗室預處理采用低溫研磨(-196℃液氮環境)保持材料穩定性;③建立包含17種標準物質的定量分析曲線;④通過三重四極桿質譜進行碎片離子驗證;⑤基于區塊鏈技術的檢測數據存證系統,實現全過程可追溯。在汽車密封件檢測中,該流程成功識別出某批次材料在150℃持續負載下產生的氯代烴超標現象,避免企業約2300萬元潛在損失。
跨行業應用實證分析
在新能源領域,某光伏背板廠商采用本檢測方案后,材料耐候性評估周期從28天縮短至9天。通過模擬85℃/85%RH雙85測試環境,準確預測出EVA封裝膠膜與三氟氯氰聚酯背板間的相容性問題。航空航天方面,檢測系統幫助某航天器涂層供應商優化固化工藝,將熱分解起始溫度從287℃提升至315℃,滿足NASA-STD-6001B標準要求。值得注意的是,在柔性顯示屏封裝應用中,方案成功檢出0.08%的殘留單體,為行業樹立了"微電子器件封裝材料純度控制"新標桿。
質量保障體系與認證網絡
檢測實驗室已獲得 ( L8765)、DAkkS(D-PL-14165-01-00)雙認證,建立包含132個質量控制點的管理體系。定期參加由LGC集團組織的國際能力驗證(PT),在最近一輪"含氟聚合物痕量雜質分析"比對中,Z值評分達到0.68(|Z|≤2為合格)。配備的追溯系統可關聯至國家級標準物質中心(GBW08617),確保檢測結果在28個經濟體互認。針對汽車行業IATF 16949體系要求,特別開發車載雷達罩材料專項檢測模塊,已為12家Tier1供應商建立材料數據庫。
## 技術展望與發展建議建議行業重點發展原位檢測技術,開發可集成于生產線的在線監測裝置。據弗若斯特沙利文預測,2027年智能檢測設備市場規模將突破90億美元,其中聚合物材料實時分析占比將達35%。應加快建立三氟氯氰聚酯全生命周期數據庫,涵蓋原料合成、加工應用及回收降解各階段數據。同時,推動ASTM/ISO標準委員會設立專門工作組,制定針對新型含氟聚合物的檢測方法標準,特別是在"極端環境材料失效分析"和"納米級材料表征"領域形成技術規范,為行業可持續發展提供支撐。

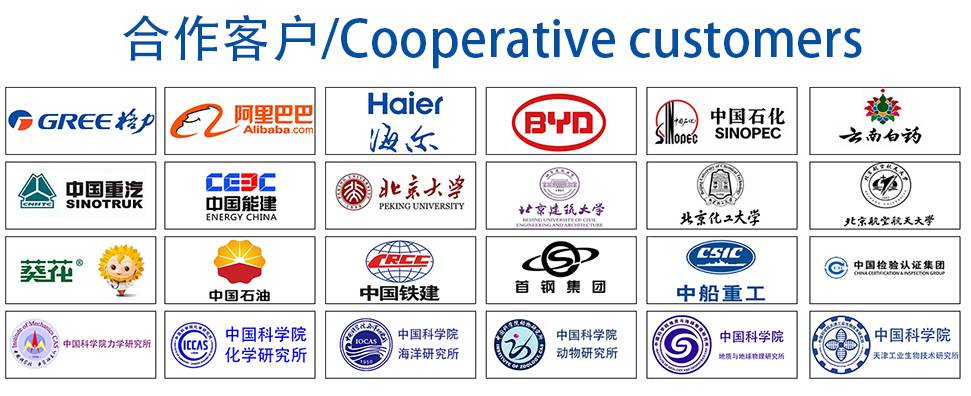