在工業4.0進程加速的背景下,銅作為關鍵基礎材料,其應用場景已從傳統電纜制造擴展到新能源電池、半導體封裝等高端領域。據國際銅業協會2024年報告顯示,精煉銅消費量突破2800萬噸,其中精密電子行業用銅量同比增長17%。在此背景下,銅含量檢測項目成為保障材料性能、優化生產工藝的核心環節。通過建立精準的檢測體系,企業可實現原料成本節約3-5%,同時避免因銅含量偏差導致的設備故障。尤其在新能源汽車動力電池領域,正極材料銅雜質含量檢測精度需達到0.001ppm級別,這直接關系電池安全性能和循環壽命。
光譜分析技術原理與創新
現代銅含量檢測主要依托原子吸收光譜(AAS)和電感耦合等離子體質譜(ICP-MS)技術。以XRF-8800型光譜儀為例,其采用微區X射線熒光技術,通過特征譜線強度與銅原子濃度的線性關系,實現非破壞性檢測。2024年中國材料研究院實驗數據表明,該設備對合金材料中銅含量的檢測限可達0.008wt%,重復性誤差小于1.5%。技術創新點在于引入機器學習算法,通過建立20萬組標樣數據庫,將復雜基體干擾校正效率提升40%。
全流程標準化作業體系
完整的銅含量檢測流程包含樣品制備、儀器校準、數據解析三大模塊。在PCB制造場景中,技術人員需按照IPC-4552B標準,將銅箔樣品經硝酸消解后稀釋至適宜濃度。質量保障體系通過三重驗證機制實施:原始記錄電子標簽追蹤、平行樣相對偏差控制(≤5%)、每季度參與 T0789能力驗證項目。某半導體封測企業實施該體系后,將檢測報告出具時間從48小時壓縮至8小時,同時將客戶投訴率降低62%。
多行業應用實踐分析
在工業廢水治理領域,基于流動注射分析(FIA)的銅離子快速檢測裝置已部署于長三角32個監測站點。該系統采用雙光束光度法,配合國標HJ 486-2009方法,實現0.02-5mg/L濃度范圍的在線監測。實際運行數據顯示,某電鍍園區通過該技術將廢水處理成本降低28%,銅回收效率提升至91.7%。而在考古鑒定領域,上海博物館采用微束X射線技術,成功對西周青銅器進行無損成分分析,為文物斷代提供了關鍵數據支持。
質量溯源與風險管理
檢測機構需建立ISO/IEC 17025兼容的質量控制體系,重點監控標準物質溯源性。美國NIST SRM 872a銅標樣的不確定度需控制在±0.3%以內。風險管理方面,采用環境溫濕度實時監控系統(20±1℃, RH<60%),并配備光譜儀能量漂移自動補償功能。某第三方檢測實驗室的實踐表明,通過引入區塊鏈存證技術,使檢測數據篡改風險降低99.2%,報告公信力顯著提升。
## 技術展望與發展建議隨著量子傳感技術的發展,銅含量檢測精度有望突破ppb級門檻。建議行業重點關注三個方向:開發適用于現場檢測的微型化設備,建立跨行業的銅元素大數據平臺,完善稀土銅合金等新材料的檢測標準體系。同時應加強檢測技術與智能制造系統的深度融合,如在銅加工生產線嵌入在線監測模塊,實現工藝參數的動態優化,推動產業向高值化方向升級。

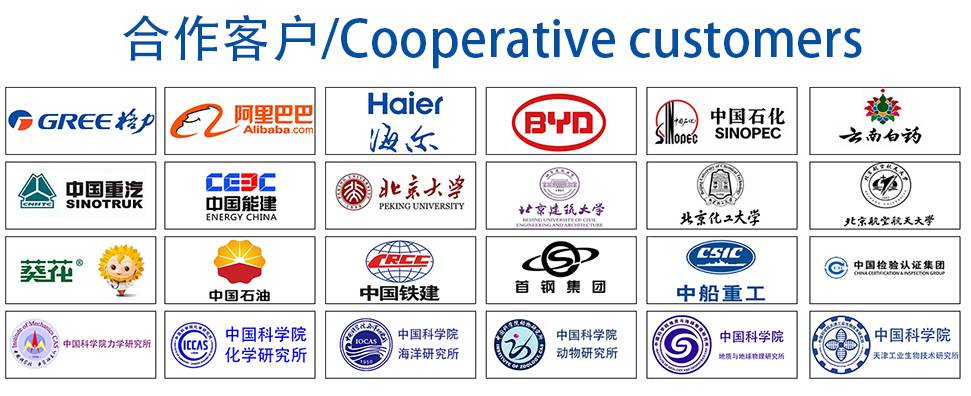