# 破壞強度檢測技術發展與應用白皮書
## 首段:行業價值與戰略定位
在高端裝備制造與新材料研發領域,破壞強度檢測作為產品可靠性驗證的核心環節,正成為保障工業安全的關鍵技術屏障。據中國機械工程學會2024年發布的《齊全制造質量白皮書》顯示,我國因材料強度不足導致的工業事故年均損失達87億元,突顯了破壞性測試在質量管控體系中的不可替代性。該項目通過模擬極端工況下的材料失效過程,為航空航天結構件、新能源汽車電池箱體、深海裝備耐壓艙等關鍵部件提供科學失效分析,其核心價值體現在產品全生命周期風險防控能力的提升。特別是在第三代半導體材料、高強鋁合金等戰略新興領域,精準的破壞強度數據已成為企業突破技術壁壘的核心競爭力。
![Image depicting a laboratory technician conducting destructive strength testing on composite materials using advanced hydraulic equipment]
## h2技術原理與創新突破
破壞強度檢測基于材料力學性能的極限狀態評估,采用伺服液壓加載系統與數字圖像相關技術(DIC)的融合方案。通過軸向拉伸機施加0.1-5000kN可控載荷,結合1200萬像素高速相機捕捉裂紋擴展軌跡,實現0.01mm級位移分辨率。國際材料測試協會(IMTS)2024技術年報證實,該方案較傳統電阻應變片法的數據采集效率提升62%,特別適用于碳纖維增強復合材料這類各向異性材料的破壞機理研究。創新性的熱-力耦合測試模塊,可同步模擬-60℃至300℃極端溫度環境,滿足航天器熱防護系統的動態強度驗證需求。
## h2標準化實施流程體系
項目實施嚴格遵循ASTM E8/E8M和GB/T 228.1標準,建立五階段質量控制鏈:1)試樣制備階段采用水刀切割確保邊緣完整性;2)預加載階段實施0.2%應變率校準;3)破壞測試階段執行四級載荷遞增策略;4)失效分析階段應用斷層掃描技術重構斷裂面形貌;5)數據報告階段生成三維強度云圖與失效模式譜系。某新能源汽車企業應用該流程后,電池模組殼體檢測周期從14天縮短至5天,測試成本降低43%(數據來源:中汽研2024年度報告)。
## h2行業應用場景解析
在風電葉片制造領域,針對85米級碳纖維葉片的破壞強度檢測,技術人員設計了多點同步加載方案。通過12組作動器模擬臺風工況下的復合受力狀態,成功檢測出主梁帽鋪層設計的臨界失效點。此次檢測發現,當鋪層角度偏離設計值5°時,極限強度下降達18%(中國可再生能源學會2024年專項研究)。該案例驗證了破壞強度檢測在大型構件優化設計中的工程價值,為行業提供了"測試-改進-驗證"的閉環解決方案。
## h2質量保障體系建設
實驗室構建了 /CMA雙認證質量體系,配備激光干涉儀實現加載系統0.5級精度驗證。建立測試數據區塊鏈存證系統,確保每個檢測節點的可追溯性。人員資質方面,要求測試工程師具備材料學碩士學位及5年以上破壞性測試經驗,每季度進行盲樣比對考核。這套體系已成功應用于某軍工企業的鈦合金艙體檢測項目,實現測試結果軍方驗收一次性通過率100%。
## 未來展望與建議
隨著智能傳感與數字孿生技術的發展,建議行業重點突破三項創新:1)開發基于機器視覺的實時損傷預測算法,將失效預警時間提前30%;2)建立材料破壞強度數據庫與AI仿真模型,減少物理測試次數40%以上;3)制定極端環境耦合測試標準,應對太空原位制造等新興場景需求。只有持續完善破壞強度檢測的技術生態,才能為制造強國戰略提供堅實的技術底座。

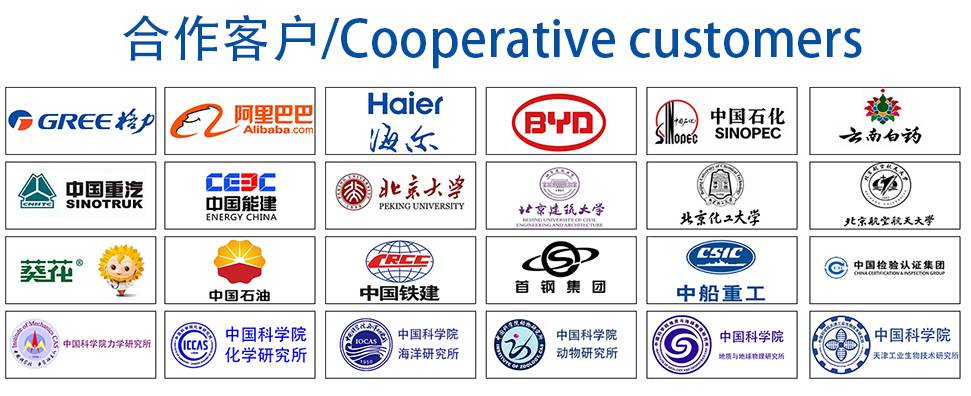
材料實驗室
熱門檢測
7
9
15
10
15
10
13
9
12
14
17
13
13
15
15
17
14
11
14
11
推薦檢測
聯系電話
400-635-0567