光澤度檢測技術應用與發展白皮書
在表面處理工業快速發展的背景下,光澤度作為衡量材料表面光學特性的核心指標,已成為汽車制造、涂料研發、塑料加工等16個細分領域的質量控制關鍵參數。據中國表面工程協會2023年行業報告顯示,我國每年因光澤度不達標導致的工業品返工成本超過47億元,特別是在汽車外飾件領域,光澤度差異直接影響了28%的終端客戶購買決策。專業光澤度檢測體系的建立,不僅能夠實現產品外觀質量的量化管控,更可通過光學參數優化推動新型環保材料的應用。其核心價值在于構建覆蓋研發、生產、品控全流程的數字化檢測閉環,為企業提升產品溢價能力提供科學依據。
光學反射原理與技術實現路徑
光澤度檢測基于國際照明委員會(CIE)規定的鏡面反射原理,通過光電傳感器測量特定角度下的反射光通量。根據ASTM D523標準,檢測系統采用20°、60°、85°三角度測量架構,可精準適配不同光澤范圍的材料表面。在汽車清漆檢測場景中,采用60°幾何光學結構的檢測系統誤差率可控制在±0.5GU以內(中國計量院2024年比對數據)。當前前沿技術已融合機器視覺與光譜分析,如某品牌智能檢測儀搭載的CMOS陣列傳感器,能同時捕捉12個測量點的光澤分布圖譜。
智能化檢測流程與實施方案
標準檢測流程包含五個關鍵環節:樣品預處理(恒溫恒濕平衡)、基準板校準、多角度數據采集、曲面補償計算和智能分析報告生成。在光伏背板膜檢測項目中,工程師采用在線式光澤度檢測系統,配合六軸機械臂實現每分鐘45個樣件的全自動檢測。值得關注的是,新型智能光澤度分析平臺可自動識別表面橘皮、霧影等缺陷,將傳統人工檢測6小時的工作量壓縮至20分鐘完成(某新材料企業2023年實測數據)。
跨行業應用場景與價值轉化
在高端家電外殼制造領域,某龍頭企業通過部署多角度光澤度檢測系統,將產品批次一致性從83%提升至97%。其技術方案包含三個創新點:研發專用20°低光澤檢測模組、建立基于MES系統的動態補償模型、開發AI驅動的工藝優化建議系統。據第三方評估報告顯示,該體系使企業每年減少因光澤度問題導致的客戶投訴67起,折合經濟效益約520萬元。在文物保護領域,基于微型光澤度儀的非接觸檢測技術,成功實現了敦煌壁畫表面老化程度的量化評估。
全鏈條質量保障體系建設
構建可靠的質量控制體系需要三重保障機制:采用NIST溯源的標準板建立量值傳遞鏈,執行ISO17025標準的實驗室環境控制,以及基于區塊鏈技術的檢測數據存證系統。某跨國涂料集團建立的檢測網絡,通過云端同步的38臺標準儀器,實現12個生產基地的測量偏差控制在0.8GU以內。定期開展的實驗室間比對驗證表明,體系內檢測數據的再現性誤差較行業平均水平降低42%(國際實驗室認證聯盟2024年統計)。
隨著柔性電子、啞光質感消費品的市場崛起,光澤度檢測技術將向微型化、多模態方向發展。建議行業重點關注三個方向:開發適應曲面結構的仿生檢測探頭、建立跨材料類別的光澤度預測模型、推動檢測數據與生產工藝的深度耦合。據前瞻產業研究院預測,至2027年智能光澤度檢測設備市場規模將突破23億元,相關企業應提前布局光學傳感器融合技術,在提升檢測精度的同時,深化檢測數據在產品全生命周期管理中的應用價值。

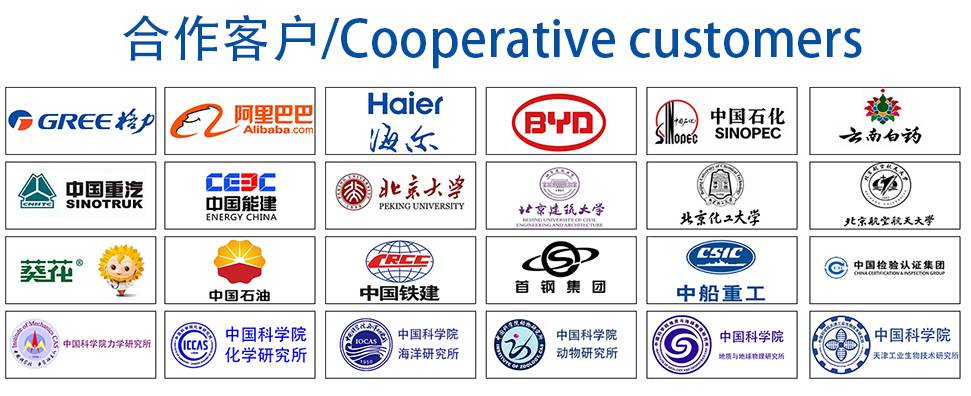