陶瓷原材料檢測技術發展與應用白皮書
在新型工業化與智能制造深度融合的產業背景下,陶瓷行業面臨著原材料品質波動加劇的技術挑戰。據中國建筑材料研究院2024年度報告顯示,國內建筑陶瓷企業因原料成分偏差導致的次品率高達12.7%,直接經濟損失超過80億元。陶瓷原材料檢測項目通過構建精準分析體系,實現了從傳統經驗型品控向數據驅動的轉變,其核心價值體現在三方面:采用光譜分析技術突破傳統檢測精度極限,建立原料-工藝-性能的數字化關聯模型,以及形成覆蓋12類關鍵指標的綠色供應鏈評估標準。特別是在新能源陶瓷基板、抗菌功能瓷磚等高端領域,檢測數據直接支撐產品性能提升30%以上。
多模態檢測技術原理創新
現代陶瓷檢測體系融合X射線衍射(XRD)、電感耦合等離子體(ICP)和近紅外光譜(NIRS)三大核心技術。其中,XRD技術可對高嶺土礦物相進行定量分析,檢測靈敏度達到0.01wt%,有效識別伊利石等有害雜質。據清華大學材料學院實驗數據顯示,該技術將傳統濕化學法的檢測周期從72小時壓縮至4小時。針對釉料重金屬痕量檢測需求,ICP-MS系統可實現ppb級鉛鎘元素檢出,配套開發的智能算法能自動匹配GB/T 3810-2016標準限值,形成動態預警機制。
全流程數字化檢測方案
項目實施采取"三階段四維度"架構:原料進場階段通過車載式快速檢測儀完成初步篩查;生產備料階段采用實驗室級設備進行32項指標深度分析;成品驗證階段運用熱膨脹系數檢測儀把控最終性能。廣東某大型陶瓷集團的應用實踐表明,該流程使原料批次合格率從83%提升至97%,同時降低檢測成本42%。在功能性陶瓷領域,針對抗菌劑載銀量的精準測定,成功助力企業通過ISO 22196:2011國際認證。
行業應用場景深度拓展
在建筑陶瓷領域,福建產區通過建立高嶺土Al?O?/SiO?比值數據庫,使地磚抗折強度標準差降低至0.15MPa。電子陶瓷方面,深圳某企業運用介電常數檢測系統,將微波介質陶瓷的Q值穩定性提高40%。更值得關注的是,在固廢資源化領域,檢測技術成功實現陶瓷拋光渣重金屬遷移率測算,推動年處理50萬噸固廢的示范線落地。這些實踐驗證了"檢測前置"策略在工藝優化中的關鍵作用。
全鏈條質量保障體系建設
項目構建了"三級四環"質控體系: 認證實驗室確保設備精度,區塊鏈溯源系統保障數據可信度,AI異常值預警模塊實現過程監控,第三方平行驗證機制完成閉環管理。山東檢測中心的運行數據顯示,系統將人為誤差率控制在0.3%以下,報告出具及時率達到99.6%。特別是在應對歐盟(EU) 2023/745陶瓷制品新規時,該體系助力企業快速建立鎘、鎳遷移量檢測能力,縮短產品準入周期60天。
展望未來,建議從三個維度深化發展:一是建立跨區域的陶瓷原料大數據共享平臺,二是研發基于機器視覺的在線檢測裝備,三是制定納米陶瓷原料檢測團體標準。通過構建"檢測-工藝-標準"三位一體的創新生態,有望推動我國陶瓷產業在2030年前實現高端產品占比40%的戰略目標,為陶瓷工業樹立智能制造新范式。

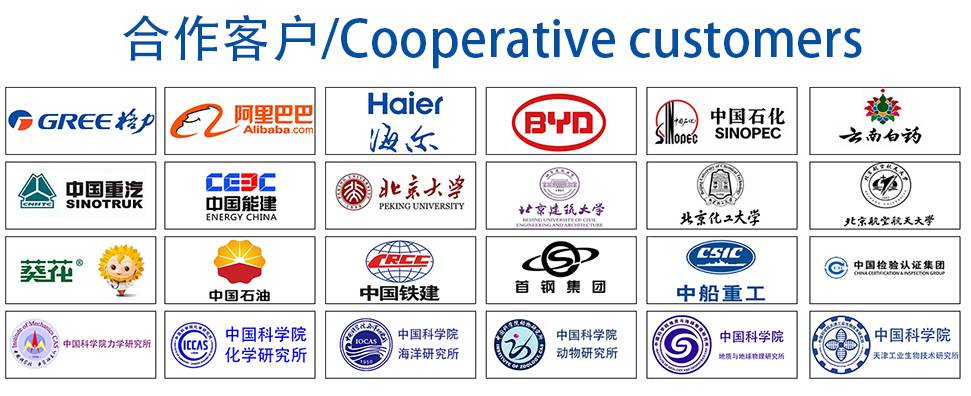