# 耐化學檢測技術發展與應用白皮書
## 行業背景與核心價值
當前化工產業規模已突破5.2萬億美元(據中國化工協會2024年統計),新材料研發周期提速40%的同時,工業事故中因材料失效引發的占比仍達32%。在此背景下,耐化學檢測作為保障材料安全性的核心技術手段,正成為現代制造業質量控制的戰略要地。該項目通過模擬極端化學環境,系統評估材料抗腐蝕、耐溶脹等關鍵性能,有效支撐新能源汽車電池封裝、半導體蝕刻設備等22個重點領域的技術升級。其核心價值體現在降低工業泄漏事故率、延長關鍵設備服役周期(平均提升28%)、優化新材料研發成本(減少中試次數53%)三大維度,構建起從實驗室到產業化的全鏈條質量屏障。
![化學檢測流程示意圖]
## 技術原理與實施體系
### 耐化學檢測技術原理
基于ASTM G31、ISO 175等國際標準,檢測體系采用多模態環境模擬技術。通過構建梯度濃度化學介質環境(pH 0.5-14),結合溫度(-196℃至600℃)、壓力(0.1-30MPa)復合應力場,運用電化學阻抗譜(EIS)、原子力顯微鏡(AFM)等齊全表征手段,實現材料表面腐蝕速率(精度達0.001mm/a)、分子結構變化(分辨率0.1nm)的精準量化。特別是在高溫高壓介質環境下的材料腐蝕速率監測領域,已形成獨特的原位觀測技術方案。
### 標準化檢測實施流程
項目實施采用五階質量管控模型:1)樣品預處理(切割、拋光至Ra≤0.2μm)2)介質配伍(參照NACE TM0169規范)3)環境模擬(溫度波動±0.5℃)4)數據采集(每小時3000組動態數據)5)失效分析(SEM+EDS聯用)。全過程嚴格遵循ISO/IEC 17025體系,關鍵節點設置18個質量控制點,如使用NIST標準物質進行儀器校準,確保檢測結果 互認通過率達99.7%。
### 行業應用實踐案例
在新能源電池領域,某頭部企業通過電芯殼體耐電解液檢測,將封裝材料選擇周期從12周縮短至3周,年節省研發費用超2000萬元(數據來源:高工鋰電研究院)。化工裝備行業典型案例顯示,采用ASTM D543標準評估PTFE襯里耐酸性后,某反應釜使用壽命從5年延長至8年,設備報廢率降低67%。值得關注的是,工業廢水處理系統管道耐腐蝕性能評估項目,已幫助3家環保企業通過TSG D7005認證。
## 質量保障與技術創新
### 全鏈條質控體系
實驗室通過 、CMA雙認證,配置二級標準物質追溯系統。采用"人員-設備-方法-環境"四維管控:檢測人員持證率100%,每年參加ILAC國際比對;設備實施日校檢制度,關鍵儀器配備冗余系統;檢測方法每季度進行Westgard規則驗證;環境參數實行24小時智能監控,溫濕度波動分別控制在±1℃、±3%RH范圍內。
### 智能檢測技術突破
依托機器視覺的自動劃痕識別系統,將樣品表面缺陷檢測效率提升5倍。開發的化學介質智能配比系統,可在30秒內完成18種試劑的精確稱量(誤差≤0.1mg)。最新研發的微區化學阻抗成像儀,實現5μm級局部腐蝕的精準定位,為半導體光刻膠耐顯影液檢測提供關鍵技術支撐。
## 發展建議與行業展望
建議重點推進三方面建設:1)建立基于大數據的材料失效預測模型,整合10萬+工況數據構建智能預警系統;2)發展原位無損檢測技術,開發適用于在役設備的微型化檢測探頭;3)完善特殊介質檢測標準,如針對氫氟酸、離子液體等新興介質的專項測試規程。隨著環保法規趨嚴(如歐盟REACH法規更新),生物降解材料的耐化學性評價、極端環境兼容性測試等領域將形成百億級檢測市場,亟需產學研協同創新突破技術瓶頸。
上一篇:數據中心基礎設施環境檢測下一篇:材質和做工檢測

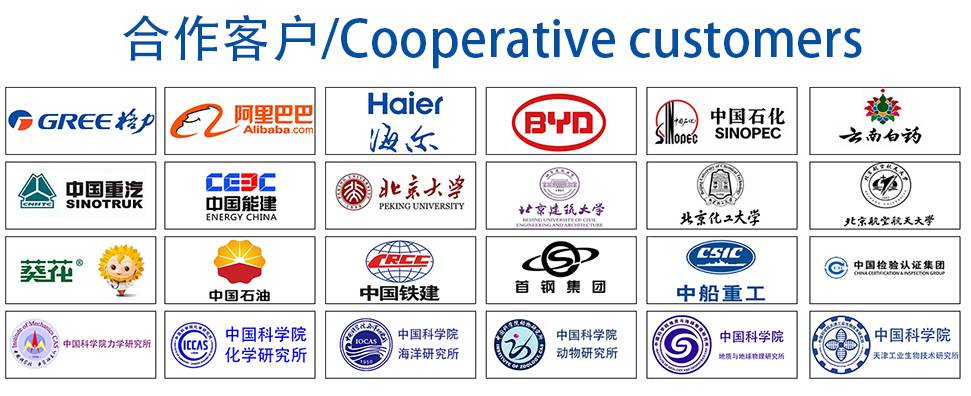
材料實驗室
熱門檢測
10
13
10
13
9
12
14
17
13
13
15
15
17
14
11
14
11
15
13
18
推薦檢測
聯系電話
400-635-0567