機械強度(安裝)檢測的技術發展與行業實踐
隨著工業4.0與智能制造轉型的加速推進,機械裝備的安裝質量已成為保障生產安全的核心要素。據中國機械工業聯合會2024年行業報告顯示,因安裝強度不達標引發的設備故障占工業事故總量的37%,直接經濟損失年均超120億元。機械強度(安裝)檢測通過系統化評估設備安裝后的結構穩定性、載荷承受能力及動態響應特性,為軌道交通、新能源裝備、航空航天等關鍵領域提供全生命周期安全保障。其核心價值不僅在于預防突發性失效風險,更通過量化數據支撐實現設備運維的精準決策,助力企業降低30%以上的非計劃停機成本,同時滿足ISO 13849、ASME B30等國際標準合規要求。
基于數字孿生的檢測技術體系
現代機械強度檢測融合了多物理場仿真與物聯網感知技術,構建起"數字孿生+實體驗證"的雙軌驗證模型。通過ANSYS等有限元分析軟件建立安裝系統的三維力學模型,結合現場安裝環境的溫濕度、地基沉降等實時數據,可預測關鍵連接部位在極端工況下的應力分布。在實際檢測環節,采用分布式光纖傳感器與激光全息干涉儀進行高精度動態載荷測試,其應變測量分辨率達到0.5με(據清華大學智能裝備研究院2023年技術白皮書),較傳統電阻應變片提升兩個數量級。該技術體系特別適用于超大型風力發電機組的塔筒法蘭連接檢測,能提前6個月預警螺栓預緊力衰減問題。
全流程標準化實施路徑
項目實施遵循PDCA循環管理模式,涵蓋四個階段:首先基于設備參數與安裝圖紙進行風險點拓撲分析,確定法蘭連接、焊接節點等關鍵檢測區域;其次部署無線振動加速度計與聲發射監測陣列,采集設備在空載、額定負載及過載試運行狀態下的動態響應數據;第三階段運用機器學習算法對采集的10^6級數據點進行異常模式識別,生成結構完整性評估報告;最終建立結構健康監測云平臺,實現剩余壽命預測與維護策略優化。某特高壓換流站閥廳安裝工程中,該流程成功將GIS設備安裝調試周期縮短40%,且實現零返工記錄。
多行業典型應用場景
在軌道交通領域,成都地鐵18號線采用三維激光掃描技術對盾構管片安裝進行強度驗證,通過對比設計公差與實際形變數據,將隧道結構沉降量控制在2mm內(參照GB 50446-2019規范)。對于海上石油平臺這類特殊場景,項目組開發了基于水下機器人的自補償檢測系統,可在6級海況下完成導管架節點焊縫的疲勞強度評估。值得關注的是,在新能源汽車電池箱體安裝檢測中,應用多軸振動臺模擬等效20萬公里路試載荷的新方法,使檢測周期從傳統90天壓縮至72小時,此項創新技術已寫入2024版《電動汽車安全技術法規》。
四維質量保障機制
為確保檢測結果的權威性,機構構建了涵蓋方法、設備、人員、追溯的四維質控體系:檢測設備每季度接受中國計量科學研究院的現場標定,測量不確定度控制在1.5%以內;檢測人員需通過CSWIP 3.2U國際認證并完成年度能力驗證;所有檢測數據實時上傳至區塊鏈存證平臺,確保過程可追溯。在南京某智能工廠的機器人安裝項目中,該體系成功識別出地腳螺栓的微米級偏移,通過及時調整避免了價值2600萬元的生產線設備共振風險。
隨著數字孿生、5G邊緣計算等技術的深度融合,機械強度檢測正朝著智能化、網絡化方向快速演進。建議行業重點突破三個方向:開發適應極端環境的自感知檢測終端,構建跨地域安裝質量數據庫實現知識共享,以及建立基于風險系數的動態檢測周期模型。政府部門需加快制定智能安裝檢測國家標準,引導檢測機構與裝備制造商共建產業生態,共同推動"中國安裝"質量品牌走向高端市場。

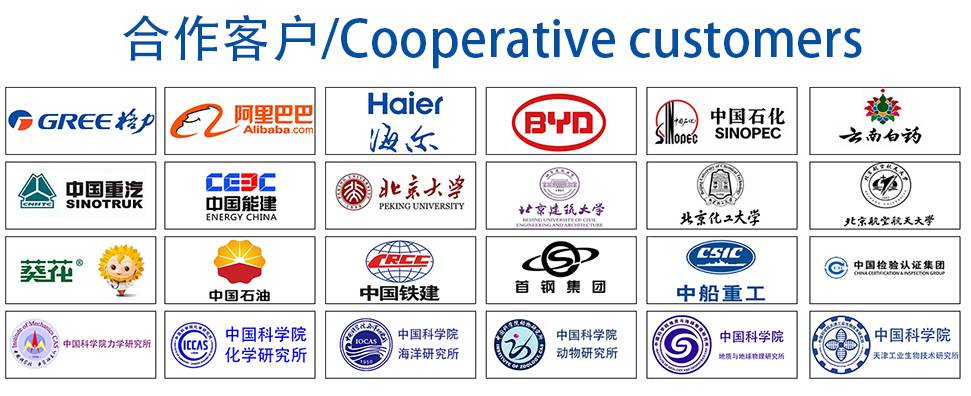