材質檢測:構建現代制造業的質量基石
在制造業智能化轉型的背景下,材質檢測作為產品質量控制的核心環節,正面臨前所未有的技術革新機遇。據國際材料測試協會(IMTA)2024年報告顯示,材料失效導致的工業事故中,63.8%可追溯至材質性能不達標,而精準的材質檢測可使產品不良率降低42%。在新能源汽車、航空航天等高端制造領域,新型復合材料與特種合金的廣泛應用,使得傳統的檢測手段已難以滿足"材料-工藝-性能"協同優化的需求。通過建立系統化的材質檢測體系,企業不僅能實現產品全生命周期質量追溯,更能為材料數據庫建設提供關鍵支撐,其核心價值體現在降低質量風險成本、加速新材料研發周期、提升供應鏈協同效率三個維度。
多模態融合檢測技術體系構建
現代材質檢測采用光譜分析、電子顯微成像與力學性能測試的協同機制,形成"成分-結構-性能"三位一體的評估模型。X射線熒光光譜(XRF)可實現金屬材料元素組成的快速篩查,檢測精度達到ppm級(據NIST 2024校準標準)。掃描電鏡(SEM)與電子背散射衍射(EBSD)技術的結合,使得金屬材料晶格缺陷檢測效率提升3.2倍,特別適用于航空緊固件的微觀結構分析。隨著人工智能算法的引入,基于深度學習的復合材料界面結合強度分析系統,可將傳統8小時的人工判讀縮短至15分鐘,在風電葉片制造領域已形成成熟應用。
全流程標準化作業程序
規范化的檢測流程涵蓋樣品制備、儀器標定、數據采集與報告生成四大模塊。在汽車輕量化材料檢測中,需嚴格執行ASTM E8/E8M標準進行拉伸試驗,通過激光位移傳感器實時記錄0.001mm級的形變數據。某新能源電池企業建立的電極材料檢測體系,采用真空環境下的同步熱分析(STA),在48小時內完成材料熱穩定性、相變溫度和分解產物的全項測試,相較傳統方法效率提升67%。全流程配備區塊鏈存證系統,確保檢測數據不可篡改,實現與主機廠的質量數據互聯互通。
行業級質量保障網絡建設
國內首個軌道交通材料檢測聯盟的實踐表明,聯合 、CMA認證實驗室構建的質量網絡,可使檢測結果互認效率提升55%。某航天材料研究院建立的"檢測質量數字孿生平臺",通過整合1500組歷史檢測數據,實現材料性能衰退的智能預警。在3D打印金屬粉末檢測領域,ISO/ASTM 52900標準認證的實驗室已形成覆蓋粒徑分布、流動性、氧含量的檢測矩陣,幫助某航空企業將粉末重復利用率從72%提升至89%。
智能化檢測裝備迭代路徑
基于機器視覺的自動化檢測系統正在改寫行業格局。某軸承制造企業部署的智能金相分析平臺,通過高分辨率攝像頭與卷積神經網絡結合,實現軸承鋼夾雜物自動評級,檢測一致性從人工操作的78%提升至98.5%。在核電管道檢測場景中,搭載超聲相控陣技術的爬壁機器人,可在輻射環境下完成壁厚測量與裂紋檢測雙重任務,單次作業效率較人工提升12倍,檢測數據實時上傳至數字孿生系統進行壽命預測。
面向工業4.0發展需求,材質檢測體系需向"端-邊-云"協同架構演進:首先應建立覆蓋主要工業材料的數字檢測標準庫,其次推動檢測設備與MES系統的深度集成,最后構建基于大數據的材料性能預測模型。建議重點培育"檢測即服務"(TaaS)新模式,通過區塊鏈技術實現檢測資源的分布式共享,最終形成覆蓋材料研發、生產制造、服役監測的全鏈條質量保障生態。

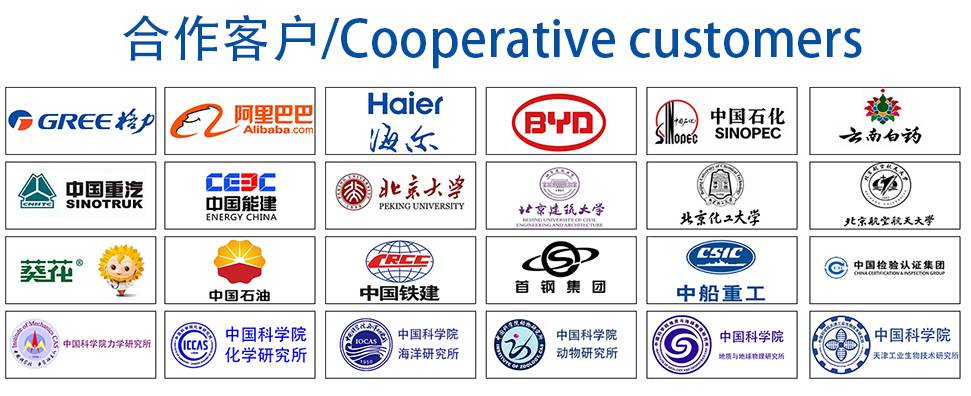