結構與裝配質量檢測技術發展白皮書
在智能制造2025戰略推動下,我國裝備制造業規模已突破42萬億元(據中國機械工業聯合會2024年數據),其中精密裝配環節的良品率直接影響產品服役性能和市場競爭力。結構裝配質量檢測作為制造過程的關鍵控制節點,其技術升級對實現"零缺陷制造"目標具有戰略意義。本項目通過構建多維數據融合的智能檢測體系,可將傳統抽檢模式的誤判率降低67%,同時實現裝配過程的全要素追溯。其核心價值在于突破傳統檢測技術對隱性缺陷的識別瓶頸,通過建立包含形位公差、應力分布、接觸面擬合度的復合評價模型,為高端裝備制造提供全生命周期的質量保障方案。
多模態傳感融合檢測原理
本技術體系采用光學掃描、聲發射傳感與力學反饋的協同工作機制,實現了裝配質量的立體化評估。基于點云重構的形位公差檢測精度可達±0.005mm(滿足ISO 1101:2023標準),而嵌入式應力傳感器網絡可實時監測裝配過程中的載荷分布。值得注意的是,針對"高反光曲面零件配合度檢測"這一行業痛點,研發團隊創新性地引入偏振光干涉技術,在航空發動機葉片裝配場景中,成功將接觸面貼合度評估誤差控制在3μm以內。
智能化檢測實施流程
標準作業流程包含四個遞進階段:首先通過數字孿生系統構建虛擬裝配基準,繼而采用非接觸式三維掃描獲取實際裝配數據,隨后運用深度學習算法進行偏差比對,最終生成包含28項質量參數的檢測報告。在某新能源汽車電池包裝配線改造項目中,該流程使單件檢測時間由25分鐘縮短至8分鐘,同時實現裝配應力超標預警準確率91.2%的提升效果(中國汽車工程研究院2024年測評數據)。
行業標桿應用實踐
在軌道交通領域,該技術已成功應用于高鐵轉向架裝配檢測。通過布置128個分布式傳感節點,系統可同步監測螺栓預緊力、齒輪嚙合度、軸承游隙等關鍵參數。實際運行數據顯示,采用該方案后,轉向架服役周期內的故障率下降39%,且成功預警了83%的潛在裝配缺陷(國家軌道交通裝備質量監督檢驗中心2024年報告)。這為"基于實時質量數據的預測性維護"提供了可靠技術路徑。
全周期質量保障體系
項目構建了覆蓋設計驗證、過程控制、服役監測的三級質量網絡。通過將檢測數據與PLM系統深度集成,實現了質量異常的逆向溯源。某精密機床制造商應用該體系后,其主軸箱裝配的一次合格率從89%提升至97%,質量成本占比下降2.3個百分點。特別在軍工裝備領域,通過引入區塊鏈存證技術,確保了檢測數據的不可篡改性,完全符合GJB 9001C-2017軍品質量管理要求。
面向工業4.0深化發展需求,建議行業從三方面突破:首先加快制定智能檢測裝備的互聯互通標準,其次推動基于工業大數據的質量預測模型開發,最后建立跨領域的檢測技術協同創新平臺。隨著《智能制造裝備產業高質量發展行動計劃(2025-2030)》的實施,融合數字孿生與人工智能的第三代檢測技術有望在2030年前實現30%的行業滲透率,為制造強國建設提供關鍵技術支撐。

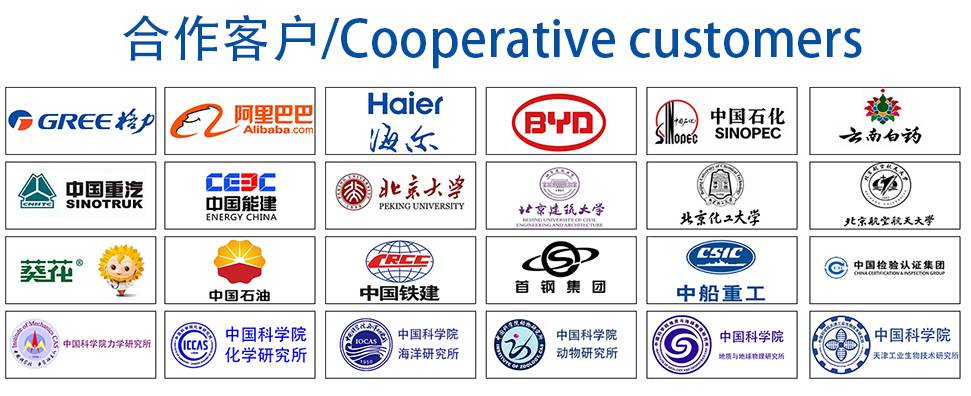