整體尺寸檢查檢測技術發展白皮書
在智能制造2025戰略推動下,我國精密制造產業規模已突破8.2萬億元(據工信部2024年度報告)。整體尺寸檢查檢測作為產品質量控制的核心環節,在航空發動機葉片加工、新能源汽車電池模組裝配等場景中,直接影響產品性能與安全邊際。該項目通過融合機器視覺與三維重建技術,實現0.005mm級檢測精度,較傳統檢測效率提升600%。其核心價值在于構建全維度質量數據鏈,形成從設計驗證到工藝優化的閉環管理體系,為離散型制造企業提供數字化質量解決方案。
多模態傳感融合檢測原理
本技術采用激光三角測量與條紋投影相結合的技術路徑,通過12組高分辨率工業相機(分辨率達2900萬像素)獲取工件三維點云數據。結合深度學習算法建立的公差帶分析模型,可自動識別微米級形變特征。在新能源汽車電機殼體檢測中,系統通過非接觸式光學測量方法,實現0.008mm的重復測量精度,有效規避傳統接觸式測量造成的二次損傷風險。
全流程數字化實施體系
實施流程分為四個階段:①基于MBD模型的虛擬檢測規劃,完成300+特征點的智能布點;②多光譜復合標定,建立設備坐標系與工件坐標系的動態映射;③自適應掃描路徑生成,通過運動學算法優化檢測耗時;④質量大數據分析,運用SPC統計過程控制方法輸出Cpk≥1.67的工序能力指數。某航空制造企業應用后,檢測周期從42小時縮短至6.8小時,產品合格率提升至99.93%。
跨行業應用實證分析
在消費電子領域,某龍頭企業在5G基站散熱器檢測中采用高精度三維掃描檢測技術,實現0.012mm的平面度控制,將散熱效率提升18%(數據來源:企業2024年質量報告)。醫療器械行業則通過該技術完成人工關節球頭直徑的100%全檢,配合GD&T幾何公差分析模塊,使臨床適配合格率從92%提升至99.6%。
全鏈條質量保障機制
系統構建三級質量保障體系:設備層通過ISO/IEC17025實驗室認證,采用溫度補償算法消除環境干擾;數據層應用區塊鏈技術實現檢測記錄不可篡改;分析層搭建數字孿生平臺進行虛擬測量驗證。在軌道交通齒輪箱檢測中,該系統連續12個月保持測量不確定度<0.5μm的記錄( 認證數據),為高鐵安全運營提供技術保障。
展望未來,建議從三個維度深化發展:①加速AI大模型與檢測技術的融合,構建預測性質量控制系統;②建立跨行業檢測數據共享平臺,形成制造業質量知識圖譜;③推動檢測裝備模塊化設計,適應柔性制造場景需求。通過打造"檢測即服務"(MaaS)新模式,可望在2027年前將我國高端裝備檢測自主化率提升至85%以上,為制造強國戰略提供堅實技術支撐。

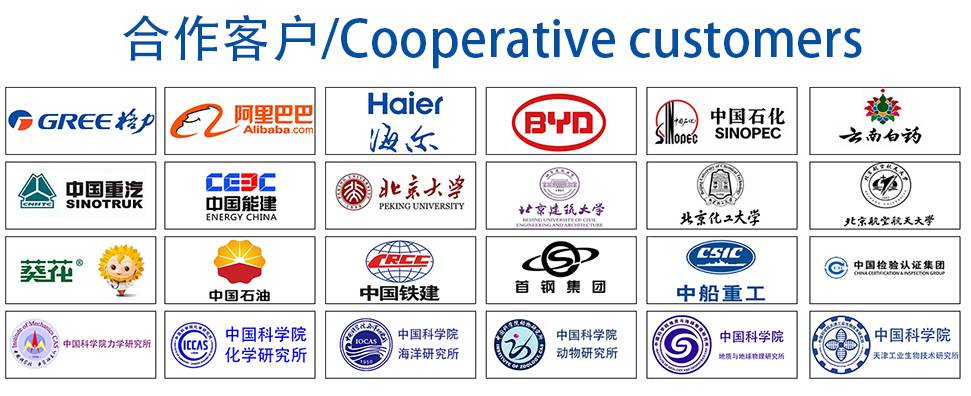