涂鍍層耐腐蝕性試驗檢測
在制造業轉型升級與"雙碳"目標推動下,金屬表面涂鍍層質量已成為影響工業產品服役性能的關鍵指標。據中國腐蝕與防護學會2024年報告顯示,我國每年因材料腐蝕造成的直接經濟損失達2.8萬億元,其中30%與防護層失效直接相關。涂鍍層耐腐蝕性試驗檢測通過模擬真實服役環境的加速腐蝕試驗,可精準評估鍍鋅層、達克羅涂層等防護體系的耐久性,為汽車零部件、海洋工程裝備等關鍵領域的質量控制提供科學依據。該項目通過建立覆蓋不同腐蝕因子(Cl?、SO?、濕度等)的復合檢測體系,有效解決了傳統單一鹽霧試驗與真實工況偏離度大的行業痛點,其核心價值在于實現防護涂層全生命周期性能預測,助力企業產品可靠性提升15%-30%。
多維度檢測技術原理
現代涂鍍層檢測采用電化學加速腐蝕與物理表征相結合的技術路線。基于ASTM B117標準的中性鹽霧試驗,配合循環腐蝕試驗箱的多因子耦合模擬,可精確復現海洋大氣、工業污染等差異化腐蝕環境。電化學阻抗譜(EIS)技術通過測定涂層/金屬界面電荷轉移電阻,可量化評估有機涂層的抗滲透性能。X射線光電子能譜(XPS)則用于分析腐蝕產物元素價態,揭示鍍層失效的化學機制。這種"環境模擬+機理分析"的雙軌模式,顯著提升了鍍鋅層鈍化膜致密性檢測等專業場景的評估精度。
標準化檢測實施流程
檢測流程嚴格遵循ISO 17025質量體系,包含五個關鍵環節:1)樣品預處理階段,根據GB/T 10125進行表面清潔與邊緣封蠟;2)加速腐蝕階段,采用Q-FOG CRH型循環腐蝕箱,執行72小時鹽霧-干燥-濕熱交替循環;3)電化學測試,在Gamry 1000E設備上完成0.1-100kHZ頻段的阻抗掃描;4)形貌表征,使用KEYENCE VHX-7000超景深顯微鏡進行1000倍微區觀測;5)數據判讀,基于ASTM D610標準對銹蝕面積進行九級量化分級。該流程已在國內某汽車板生產企業的鍍鋁鋅產品檢測中實現全流程數字化管理。
行業應用實踐案例
在新能源充電樁防護領域,某龍頭企業通過引入ISO 14993循環腐蝕檢測方案,將鍍層耐蝕性檢測周期縮短40%。針對沿海地區充電樁普遍存在的點蝕問題,檢測團隊采用40℃/95%RH濕熱試驗結合5%NaCl鹽霧的復合測試,成功識別出傳統鍍鋅層在Cl?滲透下的薄弱環節。經工藝優化后的鋅鎳合金鍍層,在青島實地掛片測試中展現出12年以上的防護壽命。另一典型案例是港珠澳大橋緊固件涂層檢測,通過ASTM G85 Annex A5酸性鹽霧測試,篩選出滿足50年設計壽命要求的氟碳涂層體系。
全鏈條質量保障體系
檢測機構構建了"人員-設備-方法"三位一體的質量控制網絡。技術人員須通過NACE CIP-2級認證,定期參與ASTM標準解讀培訓。關鍵設備實施三級量值溯源制度,鹽霧箱溫濕度傳感器每季度進行 認可實驗室比對。在數據可靠性方面,引入區塊鏈技術實現檢測參數實時上鏈,確保試驗過程不可篡改。針對風電葉片涂層檢測等特殊需求,開發出符合IEC 61400-6標準的戶外曝曬大數據校正模型,使實驗室加速試驗與自然暴露的相關系數提升至0.92。
隨著智能制造與綠色材料的發展,涂鍍層檢測技術將向智能化、微區化方向演進。建議行業重點發展三方面能力:1)構建基于機器視覺的腐蝕形貌自動評級系統;2)開發適用于鎂合金輕量化材料的專用檢測標準;3)建立跨區域腐蝕大數據共享平臺。通過融合工業互聯網與材料基因工程技術,有望實現防護涂層"檢測-預測-優化"的閉環管控體系,為裝備制造業高質量發展提供關鍵技術支撐。

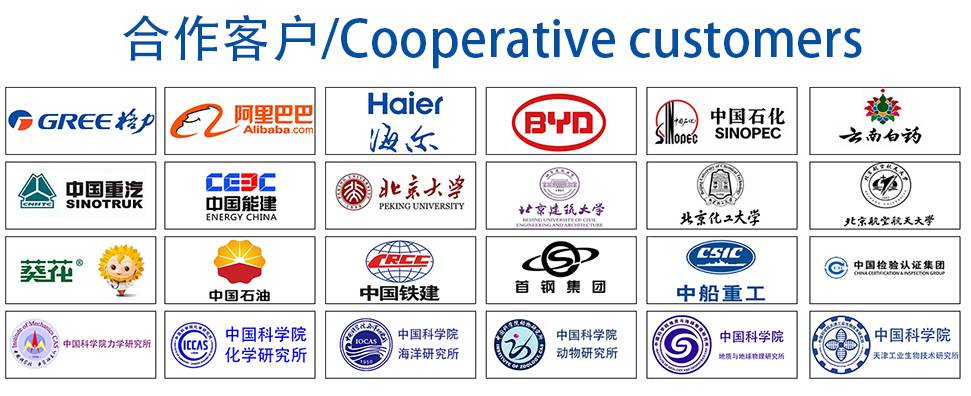