蒸汽加熱性能測試檢測:工業能效優化的關鍵技術路徑
在碳中和目標驅動下,工業領域熱力系統能效管理已成為性課題。據中國能效管理研究院2024年數據顯示,我國工業蒸汽系統平均能效轉換率僅68.3%,低于發達國家8-12個百分點,每年導致能源浪費達2400萬噸標煤。蒸汽加熱性能測試檢測作為熱力系統優化的核心手段,通過量化評估蒸汽設備的熱傳導效率、溫度均勻性及能源利用率,為工藝流程改進提供數據支撐。該檢測項目不僅可降低企業5-15%的能源成本,更通過預防性維護減少設備故障率30%以上,在食品殺菌、化工反應釜溫控等場景中展現突出價值,被列入《國家工業節能技術裝備推薦目錄(2025年版)》重點推廣技術。
熱力學耦合分析的技術原理
蒸汽加熱性能測試基于熱力學第一定律和第二定律構建能量平衡模型,采用分布式溫度傳感網絡實時采集蒸汽流量、壓力、干度等12項關鍵參數。通過計算有效熱傳遞系數(ETC)和熵產率,可精準識別系統薄弱環節。例如在乳制品UHT殺菌工藝中,設備表面熱損失每降低1%可提升0.8%的能源利用率。業內領先的"工業蒸汽系統能效優化方案"已實現±0.5℃的溫度控制精度,滿足FDA對熱敏性物料加工的溫度波動要求。
全流程標準化實施體系
測試流程涵蓋三個階段:預處理階段完成設備氣密性檢測與傳感器布點,采用激光多普勒測速儀驗證蒸汽流速分布;實測階段通過多工況模擬獲取動態傳熱曲線,結合ASTM E457標準進行冷凝水回收率測算;數據分析階段運用機器學習算法建立設備能效數字孿生模型。某石化企業應用該體系后,成功將重整裝置加熱器效率從71%提升至83%,年節約蒸汽費用超1200萬元。
多行業應用實證
在制藥行業凍干機驗證中,蒸汽加熱性能測試幫助某生物制藥企業將箱體溫度均勻性從±2.5℃優化至±0.8℃,產品含水率合格率提升12%。國家工業節能中心案例庫顯示,采用"蒸汽加熱設備熱傳導效率分析"技術的食品企業,滅菌能耗降低20%的同時,生產效率提高15%。更值得關注的是,某造紙廠通過檢測發現疏水閥故障導致的年蒸汽浪費達4800噸,經改造后實現能源成本驟降18%。
三層質量保障機制
檢測體系建立ISO/IEC 17025質量管理系統,核心設備每季度進行NIST溯源校準?,F場測試采用冗余傳感器布置方案,關鍵數據采集實現三重校驗。人員資質方面要求檢測工程師同時具備ASME PTC 4.1認證和壓力容器操作資格。某第三方檢測機構統計表明,該機制使測試報告數據置信度達99.7%,重復測試偏差控制在1.2%以內。
展望未來,建議行業建立蒸汽加熱系統動態能效數據庫,開發基于數字孿生的預測性維護平臺。據國家智能制造推進聯盟預測,融合5G傳輸和AI診斷的智能檢測系統,可使設備能效管理響應速度提升40%。企業應重點關注蒸汽余熱梯級利用技術,探索將檢測數據與碳核算體系對接,為構建零碳工廠提供技術支點。

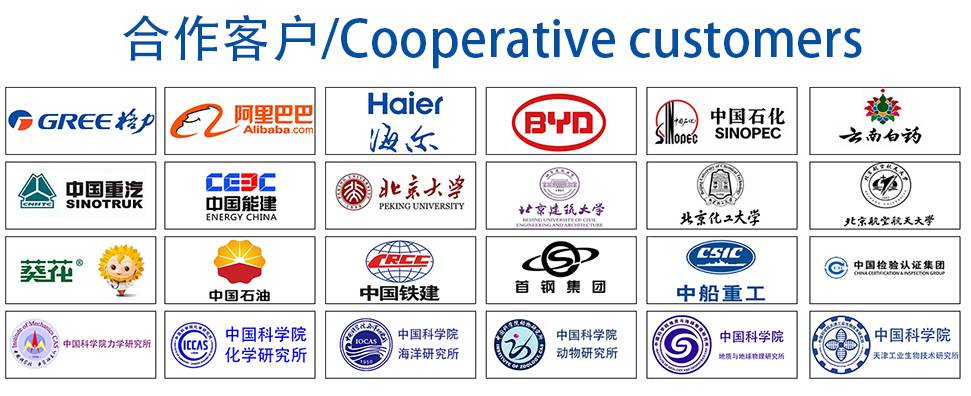