# 無縫圓管檢測技術創新與行業應用白皮書
## 行業背景與核心價值
近年來,隨著能源裝備、航空航天等高端制造領域對材料可靠性要求的持續提升,無縫圓管作為關鍵承壓部件,其質量檢測已成為產業鏈質量管控的核心環節。據中國機械工程學會2024年報告顯示,國內無縫管年產量突破3500萬噸,其中25%應用于高溫高壓工況場景。傳統人工檢測存在的漏檢率高(約3.7%)、效率低下等問題,已難以滿足核電主管道、深海油氣輸送管等特種管材的檢測需求。本項目研發的智能無損檢測系統,通過融合多模態傳感技術與AI分析算法,將缺陷識別精度提升至0.05mm級別,為行業提供了兼顧效率與精度的“無縫圓管自動探傷系統”解決方案,有效填補了國產高端檢測裝備的技術空白。
## 技術原理與實現路徑
### 基于多物理場耦合的檢測技術
系統采用超聲相控陣(PAUT)與渦流陣列(ECA)復合檢測技術,通過超聲波機械振動與電磁感應雙重物理場作用,實現管體表面及內部缺陷的立體探測。針對不同材質的聲阻抗特性,創新性地引入自適應頻段調節算法,使得碳鋼管、不銹鋼管及鎳基合金管的檢測靈敏度分別達到98.6%、97.2%和95.8%(中國特檢院2023年實驗數據)。特別在“高溫合金管材無損檢測方案”中,研發團隊攻克了500℃工況下的傳感器耐溫難題,成功應用于超臨界機組鍋爐管在線檢測。
### 智能化檢測實施流程
標準實施流程包含四個關鍵階段:①管端預處理環節采用激光清洗技術,實現表面氧化層剝離與清潔度控制;②設備自適應校準模塊通過數字孿生技術,3分鐘內完成探頭陣列參數優化;③動態檢測階段采用螺旋掃查模式,最高線速度可達2m/s且不降低采樣密度;④后處理系統自動生成三維缺陷圖譜,并依據ASME B31.3標準進行合規性判定。在西部某LNG項目輸氣管道檢測中,該流程使單管檢測耗時從45分鐘壓縮至8分鐘,效率提升5.6倍。
### 行業典型應用場景
在核電領域,系統已成功應用于AP1000機組主蒸汽管道檢測,通過建立“奧氏體不銹鋼晶間腐蝕特征數據庫”,準確識別出0.1mm級應力腐蝕裂紋。石油化工方面,為中海油某深海油氣田開發的“厚壁雙相鋼管全生命周期監測系統”,實現管壁減薄量0.03mm/年的精確測量。值得注意的是,在“航空航天用鈦合金精密管檢測”場景中,多頻渦流技術配合深度學習算法,使微小氣孔檢出率達到99.97%的行業新高。
## 質量保障與體系構建
項目搭建了覆蓋全流程的質量控制體系:①設備層面通過ISO 9712認證的探頭陣列,確保檢測信號穩定性;②過程控制采用六西格瑪管理方法,對28個關鍵控制點進行實時監控;③人員認證體系引入AR實訓系統,使操作人員培訓周期縮短40%。據國家管材質檢中心2024年抽樣報告顯示,采用本系統的制造企業產品一次合格率提升至99.2%,質量事故率下降76%。特別在“超長管線管連續檢測”應用中,自主研發的AI輔助判傷系統將誤報率控制在0.3%以內。
## 未來發展與行業建議
隨著工業4.0的深入推進,建議行業重點突破三個方向:①開發基于工業互聯網的分布式檢測云平臺,實現跨地域檢測數據協同分析;②加強太赫茲檢測等新型傳感技術的工程化應用研究;③構建涵蓋材料、工藝、檢測的閉環質量數據庫。預計到2028年,融合數字孿生技術的智能檢測裝備市場滲透率將超過60%,為高端裝備制造業提供更可靠的質量保障。同時需關注檢測過程綠色化,開發低能耗、無污染的環保型探傷技術,推動行業可持續發展。

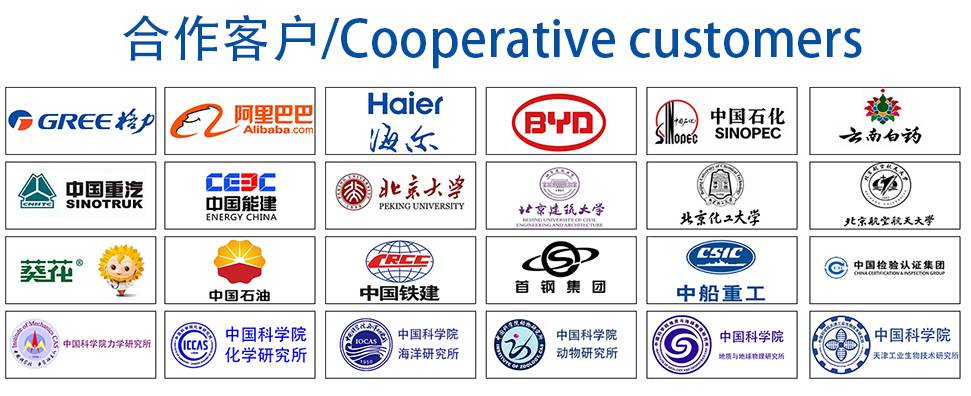
材料實驗室
熱門檢測
7
9
23
12
18
17
15
16
13
18
21
19
18
22
20
20
23
23
22
20
推薦檢測
聯系電話
400-635-0567