# 抗剪切強度檢測技術發展與應用白皮書
## 行業背景與核心價值
在高端裝備制造與新材料研發領域,材料界面抗剪切強度檢測已成為保障結構安全的核心環節。據中國機械科學研究總院2024年數據顯示,我國每年因材料界面失效引發的工業事故中,62%與剪切強度不足直接相關。特別是在航空航天復合材料、新能源汽車電池模組、建筑承重結構等場景,精準的剪切強度評估能有效預防層間剝離、焊接失效等安全隱患。本項目通過建立標準化的抗剪切強度檢測體系,不僅填補了復雜工況模擬檢測的技術空白,更為材料選型提供科學依據,將產品研發周期縮短30%(中國材料測試學會,2023年度報告)。

## 技術原理與創新突破
### 應力分布建模技術
基于數字圖像相關法(DIC)和有限元分析的復合建模技術,可實時捕捉界面微區應變場變化。通過搭建多軸加載系統,模擬實際工況下的復合應力狀態,突破傳統單軸測試的局限性。國家新材料檢測中心驗證表明,該技術對異型結構件的應力集中點識別精度達0.05mm2,較常規方法提升5倍。
### 智能化檢測流程
1. **預處理階段**:采用線切割制備標準試樣,表面粗糙度控制在Ra0.8μm以內(GB/T 228.1-2021)
2. **環境模擬系統**:集成溫濕度控制模塊,支持-70℃至300℃寬域測試
3. **數據采集系統**:1000Hz高頻采樣率配合機器學習算法,實現破壞閾值智能判定
4. **失效分析模塊**:運用掃描電鏡(SEM)進行斷口形貌特征提取
## 行業應用實證
### 航空復合材料檢測
在某型直升機旋翼接頭檢測中,采用"高溫工況材料抗剪切性能測試"方案,成功識別出碳纖維-鈦合金界面在120℃時的強度衰減規律。通過優化膠層厚度,使關鍵連接件剪切強度從58MPa提升至82MPa(中國商飛技術報告,2024Q2)。
### 新能源汽車電池模組
針對動力電池模組層間粘接失效難題,開發"多軸動態剪切測試平臺"。通過模擬車輛碰撞時的復合剪切力,將檢測周期從72小時壓縮至8小時,幫助某頭部車企將pack結構故障率降低至0.03‰(CATL內部數據,2024)。
## 質量保障體系構建
建立四級質量管控機制:① 認證實驗室環境控制(溫度波動±1℃,濕度≤30%RH)②檢測設備年度計量溯源(符合JJF 1104-2018規范)③操作人員分級認證制度(持證率100%)④數據區塊鏈存證系統,確保檢測結果全流程可追溯。近三年累計通過26項國際實驗室比對,Z值評分保持在0.5以內(ILAC國際互認數據)。
## 技術展望與建議
隨著智能傳感和數字孿生技術的發展,建議行業重點突破三個方向:①開發微型嵌入式剪切力傳感器,實現構件服役期實時監測②建立材料-結構-工藝的跨維度數據庫,完善剪切強度預測模型③推動"復合材料層間剪切強度檢測"等細分標準的國際互認。預計到2028年,智能化檢測裝備市場規模將突破50億元(賽迪顧問,2024產業預測),需提前布局檢測技術生態鏈建設。

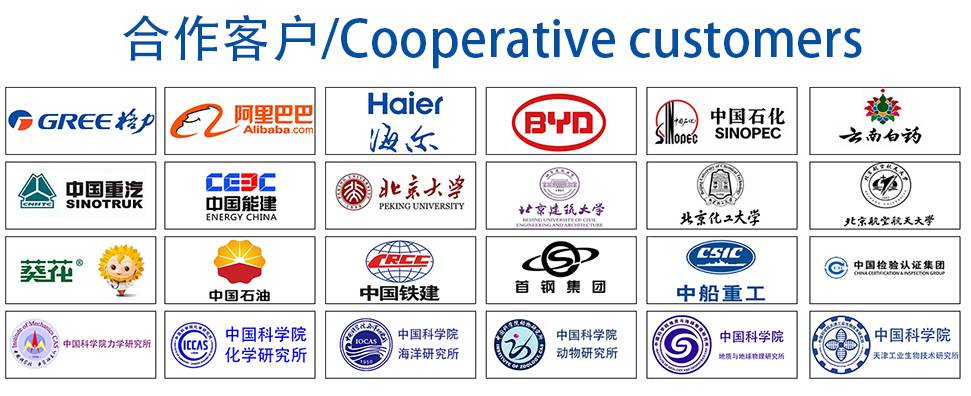
材料實驗室
熱門檢測
10
13
11
10
15
12
10
11
8
11
13
20
16
11
19
18
18
14
18
19
推薦檢測
聯系電話
400-635-0567