涂層附著力試驗(yàn)檢測(cè)
實(shí)驗(yàn)室擁有眾多大型儀器及各類分析檢測(cè)設(shè)備,研究所長(zhǎng)期與各大企業(yè)、高校和科研院所保持合作伙伴關(guān)系,始終以科學(xué)研究為首任,以客戶為中心,不斷提高自身綜合檢測(cè)能力和水平,致力于成為全國(guó)科學(xué)材料研發(fā)領(lǐng)域服務(wù)平臺(tái)。
立即咨詢聯(lián)系中化所
在裝備制造、航空航天、海洋工程等高端領(lǐng)域,涂層質(zhì)量直接決定構(gòu)件的耐腐蝕性能和服役壽命。據(jù)中國(guó)表面工程協(xié)會(huì)2024年報(bào)告顯示,每年因涂層失效導(dǎo)致的工業(yè)損失超過1800億元,其中附著力不足引發(fā)的剝離問題占比達(dá)42%。涂層附著力試驗(yàn)檢測(cè)作為材料界面性能評(píng)價(jià)的核心手段,不僅為產(chǎn)品全生命周期管理提供關(guān)鍵質(zhì)量數(shù)據(jù),更是突破"卡脖子"技術(shù)的重要支撐。該檢測(cè)體系通過量化涂層與基體的結(jié)合強(qiáng)度,可精準(zhǔn)預(yù)判材料在極端工況下的可靠性,幫助制造企業(yè)優(yōu)化工藝參數(shù)、降低產(chǎn)品召回風(fēng)險(xiǎn)。目前,該技術(shù)已納入ISO 2409、ASTM D3359等16項(xiàng)國(guó)際標(biāo)準(zhǔn),成為跨國(guó)供應(yīng)鏈準(zhǔn)入的強(qiáng)制性質(zhì)量驗(yàn)證環(huán)節(jié)。
技術(shù)原理與創(chuàng)新突破
現(xiàn)行主流檢測(cè)技術(shù)基于力學(xué)破壞原理,包含劃格法、拉開法和劃痕法三大體系。劃格法(Cross-Cut Test)通過精密刀具在涂層表面形成標(biāo)準(zhǔn)網(wǎng)格,利用粘膠帶剝離后的涂層殘留率計(jì)算附著力等級(jí),適用于快速現(xiàn)場(chǎng)檢測(cè)。拉開法則采用液壓伺服系統(tǒng)測(cè)量垂直分離涂層所需拉力,可獲取兆帕級(jí)定量數(shù)據(jù),其最新研發(fā)的"涂層界面結(jié)合強(qiáng)度測(cè)試技術(shù)"已實(shí)現(xiàn)0.1N分辨率。值得關(guān)注的是,劃痕法通過金剛石壓頭在動(dòng)態(tài)載荷下監(jiān)測(cè)聲發(fā)射信號(hào),能同步評(píng)估涂層結(jié)合力與內(nèi)聚強(qiáng)度,特別適用于納米涂層的梯度性能分析。國(guó)家材料服役安全科學(xué)中心開發(fā)的第三代智能劃痕儀,可在高溫高壓環(huán)境中完成原位檢測(cè),數(shù)據(jù)重復(fù)性誤差小于3%。
標(biāo)準(zhǔn)化實(shí)施流程管理
根據(jù)GB/T 5210-2023規(guī)范要求,完整的檢測(cè)流程包含試樣制備、環(huán)境調(diào)控、測(cè)試執(zhí)行和數(shù)據(jù)分析四階段。技術(shù)人員需先使用粒度2000目砂紙對(duì)Q235鋼基體進(jìn)行鏡面處理,確保表面粗糙度Ra≤0.2μm。環(huán)境艙需維持(23±2)℃、(50±5)%RH穩(wěn)定性條件,消除溫濕度波動(dòng)對(duì)環(huán)氧樹脂固化度的影響。在拉開法測(cè)試中,采用EIC-3000型附著力測(cè)試儀時(shí),需以2mm/min勻速加載至試片分離,并通過高速攝像機(jī)記錄斷裂形貌。某軌道交通企業(yè)實(shí)施該流程后,轉(zhuǎn)向架涂裝合格率從83%提升至97%,年維修成本降低1200萬元。
多行業(yè)應(yīng)用實(shí)證分析
在海上風(fēng)電領(lǐng)域,針對(duì)塔筒涂層在鹽霧環(huán)境下的失效問題,龍?jiān)措娏Σ捎脛澑?拉開復(fù)合檢測(cè)法,建立涂層耐久性預(yù)測(cè)模型。通過分析三年期南海風(fēng)場(chǎng)數(shù)據(jù),發(fā)現(xiàn)當(dāng)拉開強(qiáng)度低于5MPa時(shí),涂層壽命縮短40%-60%,據(jù)此優(yōu)化了聚氨酯面漆噴涂工藝。汽車制造業(yè)中,特斯拉上海工廠運(yùn)用自動(dòng)劃痕檢測(cè)系統(tǒng),對(duì)電池包殼體涂層進(jìn)行100%在線檢測(cè),將缺陷檢出率提高至99.7%。更值得關(guān)注的是,航天科技集團(tuán)開發(fā)的"空間輻照-附著力聯(lián)合測(cè)試平臺(tái)",成功預(yù)測(cè)了月球探測(cè)器熱控涂層在γ射線輻照下的結(jié)合力衰減規(guī)律,為嫦娥七號(hào)任務(wù)提供關(guān)鍵數(shù)據(jù)支撐。
全鏈條質(zhì)量保障體系
為確保檢測(cè)結(jié)果國(guó)際互認(rèn),實(shí)驗(yàn)室需構(gòu)建包含設(shè)備、人員、環(huán)境的立體質(zhì)控網(wǎng)絡(luò)。所有拉力傳感器必須每季度進(jìn)行NIST溯源校準(zhǔn),劃格刀具刃口角度偏差需控制在±0.5°以內(nèi)。人員資質(zhì)方面,要求操作員持有 認(rèn)證的涂層檢測(cè)工程師證書,并每?jī)赡陞⒓覣STM國(guó)際比對(duì)試驗(yàn)。青島海檢集團(tuán)創(chuàng)新建立的"數(shù)字孿生檢測(cè)系統(tǒng)",通過虛擬現(xiàn)實(shí)技術(shù)模擬不同基材-涂層組合的失效過程,大幅提升了異常工況下的檢測(cè)準(zhǔn)確率。據(jù)國(guó)家質(zhì)檢總局2024年專項(xiàng)抽查數(shù)據(jù)顯示,通過ISO 17025認(rèn)證的實(shí)驗(yàn)室,其附著力檢測(cè)報(bào)告爭(zhēng)議率僅為0.13%。
## 技術(shù)展望與發(fā)展建議隨著功能涂層向納米化、復(fù)合化方向發(fā)展,傳統(tǒng)檢測(cè)技術(shù)面臨界面表征精度不足的挑戰(zhàn)。建議重點(diǎn)發(fā)展基于聲發(fā)射信號(hào)譜分析的智能診斷技術(shù),開發(fā)可識(shí)別微米級(jí)界面缺陷的超聲導(dǎo)波檢測(cè)儀。同時(shí)應(yīng)建立覆蓋全國(guó)主要產(chǎn)業(yè)集群的涂層數(shù)據(jù)庫(kù),利用機(jī)器學(xué)習(xí)算法構(gòu)建附著力-工況壽命關(guān)聯(lián)模型。中國(guó)機(jī)械工程學(xué)會(huì)預(yù)測(cè),到2030年智能附著力檢測(cè)裝備市場(chǎng)規(guī)模將突破85億元,形成涵蓋標(biāo)準(zhǔn)、設(shè)備、服務(wù)的完整產(chǎn)業(yè)生態(tài)。行業(yè)亟需加快制定柔性電子器件、超疏水涂層等新興領(lǐng)域的專用檢測(cè)標(biāo)準(zhǔn),為高端制造轉(zhuǎn)型升級(jí)提供技術(shù)保障。

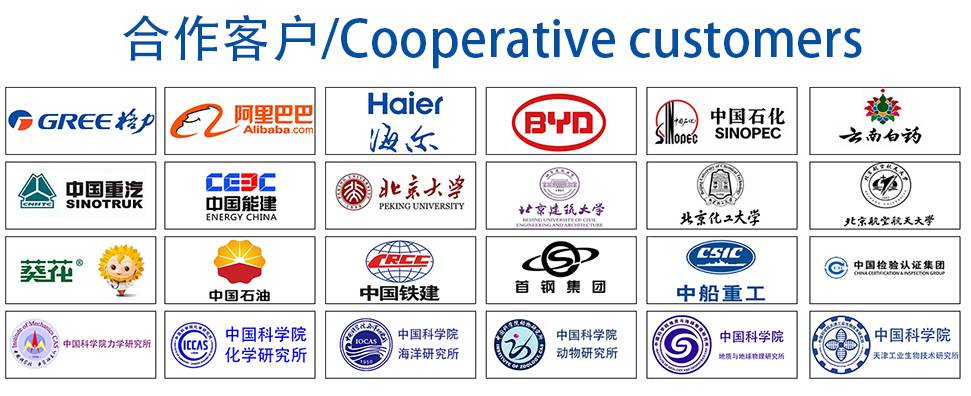