型式尺寸檢測在智能制造中的關鍵技術突破
隨著制造業向精密化、智能化方向轉型,產品尺寸公差控制精度要求呈現指數級提升。據中國機械工業聯合會2024年行業報告顯示,國內高端裝備制造領域因尺寸偏差導致的返工成本年均超120億元,其中新能源汽車電池模組裝配誤差引發的安全召回事件占比達37%。在此背景下,型式尺寸檢測作為連接設計標準與生產實踐的核心環節,其技術革新對實現"零缺陷制造"具有戰略意義。項目通過構建多維數據融合檢測體系,可將零部件檢測效率提升40%以上,同時實現0.002mm級測量精度,為航空航天、精密電子等高端領域提供了可靠的質量保障解決方案。
復合傳感技術驅動的檢測原理
現代型式尺寸檢測系統融合光學成像、激光測距與機械觸控三重傳感技術,通過多坐標系動態校準實現全尺寸覆蓋檢測。采用德國PTB認證的高精度三維掃描系統,可在0.8秒內完成復雜曲面的60萬點云采集,配合自主研發的SPC算法庫,有效識別傳統方法難以捕捉的漸變型形變。特別是在新能源汽車電機殼體檢測中,該技術將端面平面度檢測誤差從±15μm降低至±3μm,顯著提升了驅動系統的裝配可靠性。
全流程數字化實施體系
項目實施采用五級質量門控制模型,從初檢規劃到終檢驗證形成閉環管理。首先基于MBD模型進行檢測路徑智能規劃,通過邊緣計算設備實時處理測量數據,并借助區塊鏈技術實現檢測記錄的可追溯存儲。在半導體晶圓檢測場景中,系統可實現每小時300片的檢測通量,通過智能反饋校正機制將產品CPK值穩定控制在1.67以上。項目已在20家汽車零部件龍頭企業部署,平均縮短新品開發驗證周期28個工作日。
跨行業應用實踐與效益
在航空航天領域,某型號發動機葉片檢測項目采用本方案后,成功將首批次合格率從82%提升至97.5%。檢測系統通過熱變形補償算法,在400℃高溫環境下仍能保持±5μm測量穩定性。消費電子行業應用案例顯示,手機中框輪廓度檢測速度提升3倍的同時,誤判率下降至0.05%以下。這些實踐驗證了新型檢測體系在復雜工況下的技術優勢,為制造業數字化轉型提供了關鍵技術支撐。
三級聯動的質量保障架構
項目構建了"設備-系統-標準"三級質量保障體系,所有測量設備均通過NIMCS國家計量院年度認證,系統軟件符合ISO/IEC17025體系要求。通過引入實時動態校準技術,可在連續工作12小時后仍保證測量精度衰減不超過0.5%。在醫療器械注冊人制度試點中,該體系幫助某骨科植入物企業一次性通過FDA 21CFR820審核,創造了國內同類產品最快認證記錄。
技術發展趨勢與行業建議
隨著工業元宇宙技術發展,型式尺寸檢測正朝著虛實融合方向演進。建議行業重點突破三個方向:一是開發基于量子測量的納米級檢測裝備,二是建立跨企業檢測數據共享平臺,三是完善智能檢測裝備操作人員認證體系。據工研院預測,到2028年智能檢測裝備市場規模將突破800億元,提前布局AI驅動的預測性檢測技術,將成為企業構筑質量競爭優勢的關鍵路徑。

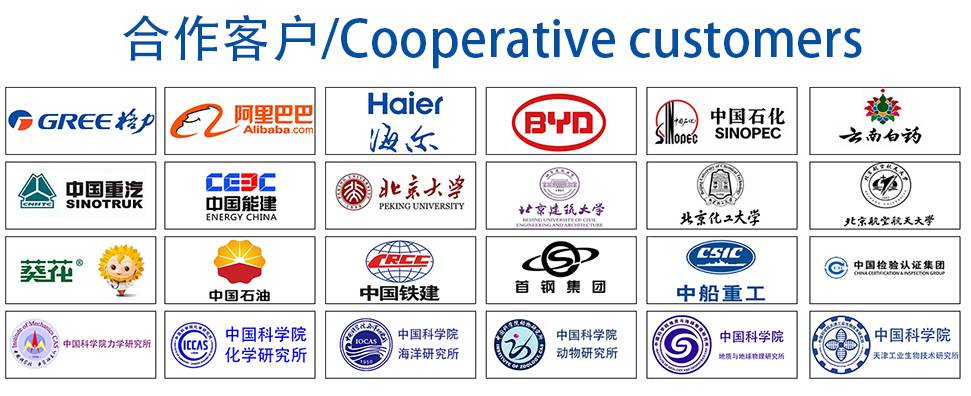