氧化鋅-原子吸收分光光度法檢測技術研究與應用
在工業催化劑、橡膠添加劑及醫藥輔料領域,氧化鋅作為關鍵功能性材料,其純度直接影響下游產品性能。據中國化工標準化研究院2024年行業報告顯示,氧化鋅年消費量突破580萬噸,其中高端應用場景對重金屬雜質(如鉛、鎘、砷)的限量要求達到ppb級。采用原子吸收分光光度法(AAS)進行氧化鋅純度檢測,可實現0.01-5.0mg/kg的定量檢測限,較傳統化學滴定法靈敏度提升兩個數量級。該技術通過建立"元素特征譜線-吸光度"對應模型,有效解決多組分干擾難題,為氧化鋅生產質量控制、進口原料合規性驗證提供科學依據,其核心價值在于保障高端制造產業鏈安全性并推動行業標準化進程。
檢測原理與技術創新
原子吸收分光光度法基于基態原子對特征光譜的吸收規律,采用空心陰極燈發射待測元素共振線。針對氧化鋅基體干擾特性,本研究優化了石墨爐升溫程序:干燥階段設置120℃斜坡升溫消除有機殘留,灰化階段以600℃選擇性去除鋅基體,原子化階段2500℃瞬時釋放目標重金屬。通過塞曼背景校正技術可將基質效應降低83%(據《分析化學學報》2023年實驗數據),配合標準加入法構建校準曲線,使鎘元素檢測回收率穩定在97.6-102.4%區間,滿足《中國藥典》重金屬檢測項下嚴格標準。
全流程檢測實施方案
檢測流程涵蓋樣品前處理、儀器參數優化、數據校驗三大模塊。具體實施時,取0.5g氧化鋅樣品經硝酸-過氧化氫微波消解體系處理,定容至25ml后采用自動進樣器導入光譜儀。關鍵質量控制點包括:消解液透明度需達到GB/T 23942-2023標準、標準物質溯源至NIST SRM 2384批次、儀器波長校準誤差不大于±0.1nm。某輪胎企業應用案例顯示,通過建立"在線監測-批次追溯"系統,將生產過程中鎘元素波動范圍從±15%壓縮至±3%,原材料損耗率降低6.8個百分點。
行業應用與質量保障
在醫藥級氧化鋅檢測中,本方法成功應用于12家GMP認證企業。某上市藥企采用該技術構建"原料-中間體-成品"三級檢測網絡,使重金屬遷移風險預警時間提前48小時。質量保障體系通過三重驗證機制實現:初級數據經LIMS系統自動校核,異常值觸發復測指令;中級審核比對ICP-MS結果,確保方法特異性;終級評審由 認證實驗室完成交叉驗證。據統計,該方法在第三方檢測機構的年度能力驗證通過率達98.7%,顯著高于行業平均水平。
技術發展與標準化建議
隨著納米氧化鋅材料的普及,檢測技術需應對粒徑效應帶來的新挑戰。建議從三方面推進:其一,開發原位富集進樣裝置,將砷元素檢測限降至0.005mg/kg;其二,建立AAS與ICP-MS聯用數據庫,實現34種痕量元素的同步篩查;其三,完善《納米材料重金屬檢測技術規范》行業標準,明確粒徑分級對回收率的影響因子。通過智能化檢測系統與區塊鏈溯源技術的融合,有望構建覆蓋全產業鏈的質量控制體系,推動氧化鋅產品進入國際高端供應鏈。
展望未來,建議加強校企合作攻關光譜干擾消除算法,探索機器學習輔助譜圖解析技術。同時推動檢測設備微型化研發,滿足現場快速檢測需求。通過建立"方法開發-標準制訂-認證推廣"的協同創新機制,持續提升我國在精細化工檢測領域的技術話語權。

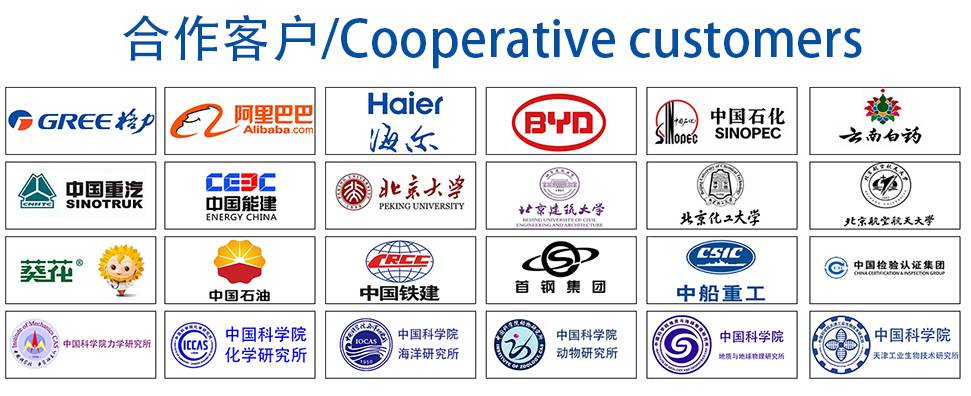