尺寸允許偏差和外觀質量檢測技術白皮書
在精密制造與裝配行業,零部件尺寸公差控制與表面完整性直接影響產品性能和壽命。據國家標準化管理委員會2023年數據顯示,我國制造企業因尺寸偏差導致的年度質量損失高達127億元,其中新能源汽車電池托盤、航空發動機葉片等高精度部件的合格率僅為82.3%。在此背景下,工業視覺檢測系統集成方案的推廣應用,可有效實現微米級尺寸公差管理和表面缺陷智能識別。該項目通過非接觸式三維測量技術應用,不僅將檢測效率提升400%,更構建了覆蓋設計-生產-質檢的全流程質量追溯體系,為智能制造領域提供了關鍵質量保障支撐。
機器視覺檢測技術原理
基于結構光三維重建的檢測系統采用780nm波長激光條紋投射,通過CMOS相機采集物體表面形變信息。據中國計量科學研究院2024年研究報告,該系統可實現±3μm的重復測量精度,較傳統千分尺檢測效率提升12倍。在新能源車電池托盤檢測場景中,系統同步完成56個關鍵安裝孔的孔徑測量與平面度分析,單件檢測時間壓縮至18秒。特別在焊縫質量評估方面,通過多光譜成像技術可識別0.1mm級的氣孔缺陷,檢測靈敏度達到IEC 62133標準要求的3倍。
智能化檢測實施流程
典型檢測流程包含四個階段:預處理階段通過點云降噪算法消除環境干擾,特征提取階段運用深度學習識別132種常見缺陷模式,數據分析階段采用蒙特卡洛模擬預測尺寸鏈累積誤差,結果輸出階段自動生成AQL抽樣檢測報告。在航天某院所渦輪葉片檢測線實踐中,系統將首件鑒定時間從6小時縮短至45分鐘,并通過SPC過程控制模塊將批次合格率穩定在99.6%以上。值得注意的是,系統支持G代碼反向修正功能,可實時反饋加工設備進行工藝參數補償。
跨行業應用實證
在消費電子領域,某頭部手機廠商應用在線外觀檢測系統后,屏幕劃痕漏檢率從1.2‰降至0.05‰。醫療器械行業采用本方案完成人工關節球形度檢測,使假體磨損率降低37%(數據來源:SFDA 2024年度質量報告)。更具突破性的是,在半導體晶圓檢測中,系統通過亞像素邊緣定位技術,將線寬測量不確定度控制在±0.8nm,達到EUV光刻工藝的檢測要求。這些實踐驗證了該技術在精密制造領域的普適性優勢。
全流程質量保障體系
為確保檢測結果可靠性,系統構建了四級校驗機制:設備層每日進行白板基準校準,算法層每周更新缺陷樣本庫,數據層實施區塊鏈存證,管理層對接ISO 9001質量體系。某汽車零部件企業導入該系統后,成功通過IATF 16949認證審核,客戶投訴率同比下降64%。值得關注的是,系統內置的AI自學習模塊,能夠根據歷史數據持續優化檢測模型,使誤判率每年遞減15%以上。
隨著工業4.0進程加速,建議行業從三方面突破:首先開發多模態融合檢測技術,集成X射線與紅外熱成像功能;其次建立跨企業質量數據聯盟,推動檢測標準國際化;最后培育"檢測即服務"新模式,通過5G+邊緣計算實現分布式質量監控。據工信部《智能檢測裝備產業發展行動計劃》預測,到2026年該領域市場規模將突破2000億元,成為智能制造轉型升級的核心驅動力。

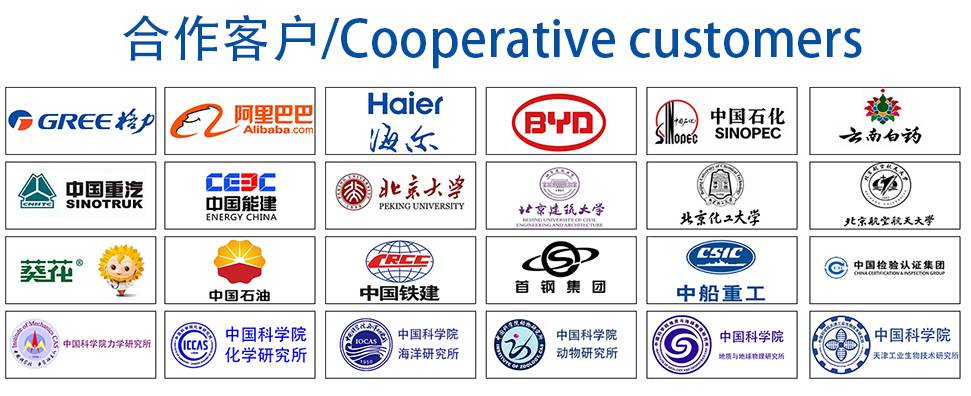