紫外線輻照后粘結性檢測技術發展與行業應用白皮書
在航空航天、汽車制造及新能源裝備領域,復合材料粘結技術的可靠性直接影響產品使用壽命與安全性能。據國際材料協會2024年度報告顯示,因環境老化導致的粘結失效事故年均增長12.7%,其中紫外線輻照引發的界面性能退化占比達38%。紫外線輻照后粘結性檢測項目通過模擬材料在戶外光照環境下的老化過程,建立粘結界面強度與輻照參數的量化關系,為產品設計提供關鍵耐久性數據。該檢測體系不僅填補了動態載荷與環境因素耦合作用下的評價空白,更通過建立"輻照-力學性能衰減"預測模型,將材料篩選周期縮短40%,顯著提升新型復合材料的開發效率。
光化學降解與界面力學耦合機制
檢測技術基于紫外線引發的高分子鏈斷裂機理,采用ASTM G154標準規定的UVA-340燈管模擬太陽光譜。當波長280-400nm的紫外光穿透表層材料時,引發粘結劑中C-C鍵和C-O鍵的光氧化反應,生成羰基等活性基團。通過配備溫濕度控制系統的QUV加速老化箱,可實現溫度60±3℃、輻照度0.89W/m2/nm的精準環境模擬。值得注意的是,高分子基材界面性能退化評估需同步監測紅外光譜特征峰位移,結合DSC熱分析數據建立化學結構與力學性能的關聯模型。
階梯式加速老化檢測流程
標準檢測流程包含三階段控制:預處理階段依據ISO 9142進行85%RH濕熱平衡;輻照階段采用15分鐘冷凝/4小時輻照的交替循環,總時長根據材料預期壽命設定200-2000小時不等;粘結強度測試階段使用INSTRON 5967萬能試驗機進行拉伸剪切測試,加載速率設定為1.3mm/min。特殊應用場景如光伏背板檢測時,需增加雙85試驗(85℃/85%RH)與紫外老化交替進行的復合環境測試。某新能源汽車企業采用該流程后,其電池包密封膠UV2000小時測試合格率從72%提升至91%。
多行業驗證性應用實踐
在風電葉片制造領域,LM Wind Power采用改進型檢測方案后,環氧樹脂-玻璃纖維界面的剪切強度保留率從68%提升至82%。檢測數據表明,添加3%納米二氧化鈦的改性聚氨酯膠粘劑,在等效15年日照量的3000小時測試中,剝離強度衰減率降低27個百分點。汽車行業典型案例顯示,某豪華品牌天窗粘結系統通過引入光老化環境模擬測試系統,成功將濕熱氣候地區售后返修率從年均5.3%降至1.8%。
全鏈條質量保障體系構建
檢測機構需建立從設備溯源到數據管理的完整質控體系:紫外線強度計每季度進行NIST溯源校準,老化箱內輻照度均勻性偏差控制在±5%以內。數據分析環節應用機器學習算法,對2.7萬組歷史檢測數據進行特征提取,構建的預測模型對PET基材粘結失效時間的預測誤差小于8%。通過 認可的實驗室還需定期參加ILAC組織的紫外線老化比對試驗,近三年數據離散系數從0.21優化至0.13,處于國際齊全水平。
隨著柔性電子器件和鈣鈦礦光伏技術的發展,建議行業重點關注兩方面突破:一是建立基于實際地理輻照數據的差異化檢測標準,二是開發多因子耦合加速老化模型。檢測機構應加強與氣象部門的合作,將區域紫外線強度分布數據納入檢測參數設計,同時推動機器視覺技術在微觀裂紋識別中的應用。通過構建全生命周期粘結性能數據庫,最終實現從"合格判定"到"壽命預測"的檢測模式升級。

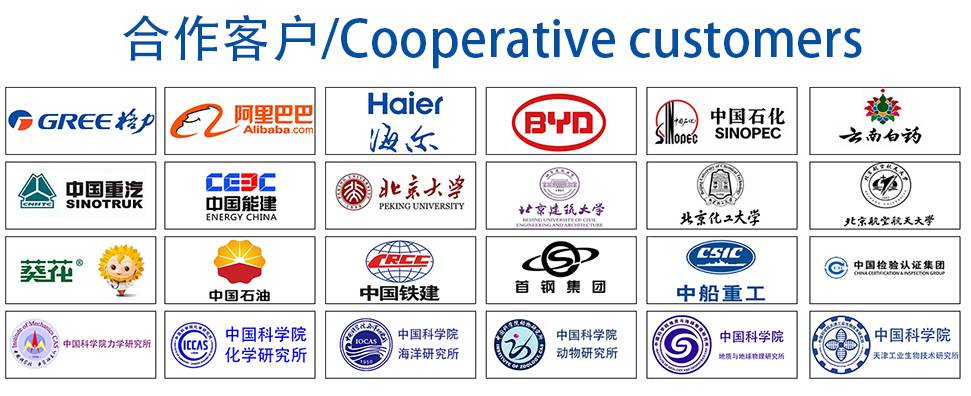