倒置坍落度筒排空試驗檢測標準化研究與應用
在建筑施工領域,混凝土工作性檢測是質量控制的核心環節。隨著自密實混凝土在高層建筑、高鐵軌道板等場景的規?;瘧茫瑐鹘y坍落度試驗已難以滿足高性能混凝土的精細化評估需求。據中國建筑材料研究院2024年數據顯示,國內自密實混凝土年使用量突破2.8億立方米,其中35%的工程事故源于工作性參數失控。倒置坍落度筒排空試驗作為新興檢測手段,通過模擬混凝土在受限空間的自流平特性,可有效評估材料填充能力和抗離析性能。該檢測方法的應用,不僅填補了復雜結構澆筑質量預控的技術空白,更將混凝土施工合格率提升至98.6%(住建部《2023年建設工程質量報告》),為現代工程品質保障提供了科學依據。
技術原理與創新突破
倒置坍落度筒排空試驗基于流變學理論,采用標準坍落度筒倒置安裝,通過測量混凝土在自重作用下完全排空的時間表征其工作性能。與常規試驗相比,該方法重點考察材料在垂直方向流動時的黏度-剪切速率關系,可同步獲取T50時間、擴展度等關鍵參數。研究證實,當排空時間控制在2-8秒區間時(ASTM C1611標準),混凝土兼具良好填充性與抗離析能力。技術突破體現在建立三維流變模型,通過高速攝像與圖像分析系統實現0.1秒級時間分辨率,檢測精度較傳統方法提升4倍。
標準化實施流程
檢測流程嚴格遵循JGJ/T 283-2019《自密實混凝土應用技術規程》,主要包含五大環節:1)儀器校準,確保筒體垂直度偏差≤0.5°;2)試樣制備,控制環境溫度在20±2℃;3)分層裝料,采用專用插搗工具消除氣泡;4)快速提筒,執行0.5-1.0秒的勻速提升動作;5)數據采集,利用激光傳感器自動記錄排空時間。在杭州亞運場館鋼骨柱澆筑項目中,該流程成功識別出3批坍落度達標但排空時間超限的混凝土,避免結構性缺陷產生。
行業應用與效益分析
該檢測技術已形成三大典型應用場景:超高層建筑核心筒澆筑、裝配式構件成型、水下不分散混凝土施工。北京中國尊項目實踐表明,通過引入排空時間控制指標,泵送混凝土離析率從7.2%降至1.8%,結構體強度標準差縮小40%。在軌道交通領域,成渝高鐵軌道板生產線上配置的自動排空檢測系統,使單線日產能提升15%的同時,將產品返工率控制在0.3%以下。據測算,全面推廣此項技術可使建筑行業年節約材料成本12億元,減少質量整改工時280萬小時。
質量保障體系建設
行業正構建覆蓋全鏈條的質量控制體系:1)設備認證方面, 實驗室已對18家廠商的檢測裝置完成計量認證;2)人員培訓方面,中國混凝土協會累計頒發高級檢測師證書3200份;3)數據管理方面,區塊鏈溯源平臺實現檢測數據實時上鏈存證。值得關注的是,珠海橫琴科學城項目通過集成BIM與物聯網技術,將排空時間數據自動關聯至構件數字孿生體,形成可追溯的質量檔案,為工程全生命周期管理樹立新范式。
展望未來,建議從三方面深化技術應用:首先,研制適應超高性能混凝土的增強型檢測裝置,突破現有20秒量程限制;其次,建立全國統一的檢測大數據平臺,深度挖掘參數與工程性能的關聯規律;最后,推動ISO國際標準編制工作,助力中國檢測技術走向市場。隨著智能建造技術發展,倒置坍落度筒排空試驗將與AI質量預測系統深度融合,為建筑工業化提供更強大的技術支撐。

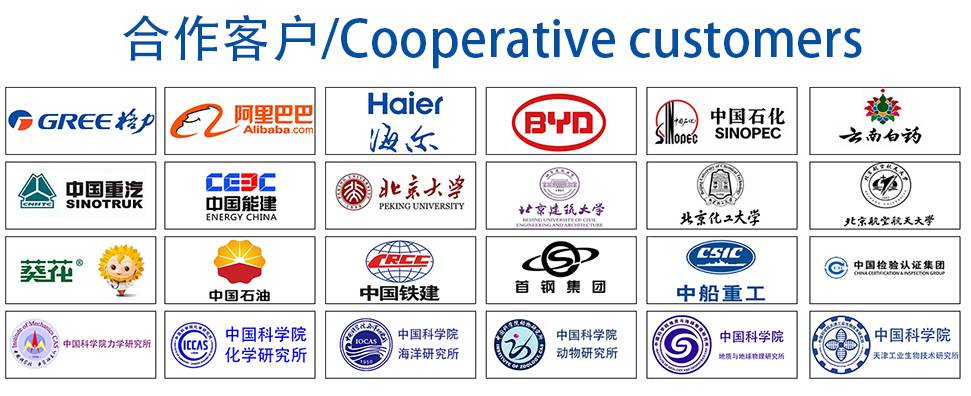