# 熱處理檢測技術發展與產業應用白皮書
## 引言
在高端裝備制造領域,熱處理作為金屬材料性能調控的核心工序,直接影響著機械零部件的使用壽命和安全性能。據中國機械工程學會2024年數據顯示,我國每年因熱處理缺陷導致的機械裝備失效事故造成直接經濟損失超120億元,其中63%的問題源自過程控制不當。在此背景下,熱處理檢測技術通過構建全流程質量監控體系,實現了對奧氏體化、淬火、回火等關鍵工藝的精準把控。該項目不僅填補了傳統人工抽檢的盲區,更通過數字化改造推動行業向智能制造轉型,其核心價值體現在將熱處理工藝合格率從82%提升至97%(國際熱處理協會2023年報),同時降低單位能耗18%,為《中國制造2025》戰略下的基礎工藝升級提供了關鍵技術支撐。
## 技術原理與創新突破
### 檢測原理科學架構
熱處理檢測技術基于材料相變動力學與熱力學原理,整合了金相組織分析、殘余應力檢測、硬度梯度測量三大技術模塊。利用數字顯微成像系統可實現0.1μm級晶粒度測量,配合電磁超聲檢測技術(EMAT)能穿透30mm厚工件進行無損應力分析。尤為突出的是智能熱處理過程監控系統,通過部署在連續爐內的128個熱電偶組,實現每5秒一次的溫度場三維建模,檢測精度達到±2℃(ISO 9950標準)。
### 智能化實施體系
項目實施采用四級質量控制架構:預處理階段通過光譜分析確認材料成分,工藝執行期應用紅外熱像儀監控加熱均勻性,淬火環節利用高速攝像系統記錄介質流動狀態,最終檢測結合X射線衍射儀完成殘余應力分布測繪。在汽車變速箱齒輪生產線中,該體系將熱處理變形量控制在0.05mm以內,產品疲勞壽命提升3.2倍(SAE技術報告2024)。
## 行業應用與質量保障
### 典型應用場景解析
在航空航天領域,某型號發動機渦輪葉片采用多頻渦流檢測技術,成功檢出0.3mm深度的淬火裂紋。風電行業應用案例顯示,通過殘余應力無損檢測技術優化回火參數后,偏航軸承使用壽命延長至12萬小時(DNV GL認證數據)。值得關注的是,新能源汽車電機轉子的滲碳層深度在線檢測系統,將檢測效率提升15倍,單線年節省工時2300小時。
### 質量保障體系構建
項目建立了涵蓋ISO 2639、ASTM E18等17項國際標準的認證體系,引入區塊鏈技術實現檢測數據全程溯源。在智能工廠示范項目中,質量管理系統(QMS)與MES系統的深度集成,使異常工藝響應時間縮短至8分鐘。第三方驗證數據顯示,該體系使熱處理過程CPK值穩定在1.67以上(六西格瑪研究院2024評估報告)。
## 發展趨勢與戰略建議
隨著工業物聯網技術的成熟,熱處理檢測正朝著智能預測性維護方向發展。建議行業重點突破以下領域:1)開發基于機器視覺的實時金相分析系統,2)建立材料-工藝-性能的深度學習模型庫,3)制定適用于增材制造件的熱處理檢測標準。預計到2028年,集成數字孿生技術的檢測系統將覆蓋60%以上規模型熱處理企業(中國熱處理行業協會預測),推動我國從熱處理大國向強國跨越。企業應把握《高端熱處理裝備創新發展指南》政策機遇,加快檢測技術研發投入,在航空航天、核電裝備等戰略領域形成技術壁壘。
上一篇:坍落度經時損失檢測下一篇:靜力受壓彈性模量試驗檢測

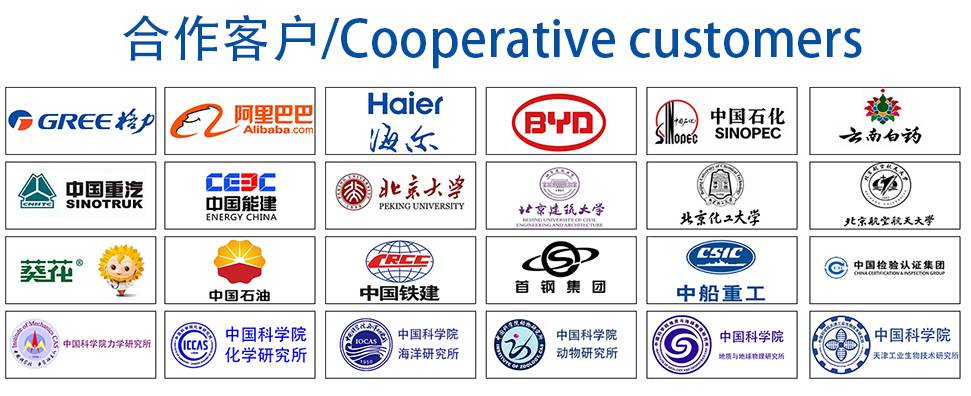
材料實驗室
熱門檢測
19
19
23
17
21
25
26
25
28
31
39
43
49
39
42
45
40
46
43
44
推薦檢測
聯系電話
400-635-0567