管殼偏心度檢測技術發展與應用白皮書
在石油化工、核電裝備等重工業領域,壓力容器與熱交換設備的安全運行直接關系著工業生產效率和人員安全。據中國特種設備研究院2024年數據顯示,因管殼類組件偏心缺陷導致的設備故障占承壓設備事故總量的23.7%,年度直接經濟損失超18億元。管殼偏心度檢測作為機械制造中的關鍵質量控制環節,通過精確測量管殼同心度偏差,可有效預防因應力集中引發的結構失效。該項目的核心價值體現在三個方面:采用非接觸式檢測技術實現微米級測量精度;建立數字化質量檔案提升產品追溯能力;通過早期缺陷識別降低運維成本40%以上(中國機械工程學會,2023)。
多模態融合檢測技術原理
基于渦流-激光復合傳感技術,系統通過電磁感應原理檢測導電材料的厚度變化,配合激光三角法測量幾何形位偏差。當檢測探頭沿管殼軸向運動時,16通道傳感器陣列以5000Hz采樣頻率同步采集數據,結合三維點云重構算法,可實現±5μm的測量精度。特別針對核電蒸汽發生器U型管束的復雜結構,系統搭載的多軸聯動定位裝置能自動適應3-120mm管徑變化,在核島密閉環境中完成全自動檢測作業。
智能化檢測實施流程
標準檢測流程包含四個核心階段:首齊全行管端預處理,采用機械式除銹裝置清除表面氧化層;隨后通過激光跟蹤儀建立設備坐標系,完成傳感器陣列的在線標定;在自動掃描階段,工業機器人攜帶檢測單元以0.2m/s恒速移動,實時生成包含8000個測量點的三維模型;最終經智能診斷系統比對ASME標準,輸出包含偏心矢量圖、應力云圖的綜合檢測報告。某煉化廠換熱器管束檢測項目實踐表明,該流程使單臺設備檢測時效提升3.6倍。
典型行業應用實踐
在核電站維護領域,大亞灣核電運營公司采用該技術對二代改進型機組進行年度檢測,成功識別出12處隱蔽性偏心缺陷,將非計劃停堆概率降低58%(中國核能行業協會,2023)。在石化裝備制造端,蘭州石化機械廠將其集成于管板自動焊接生產線,實現加工質量在線監控,使產品一次合格率從92.4%提升至98.7%。更值得關注的是在LNG儲罐建造中的應用,通過建立管殼組件的"數字孿生"模型,施工方可提前6個月預測潛在泄漏風險點。
全生命周期質量保障體系
系統構建了包含設備計量、過程控制、數據管理的三維質保架構:計量溯源方面,每季度通過國家計量院標準件進行量值傳遞;過程控制設置21個質量見證點,操作人員需持有ASNT三級認證;數據管理端采用區塊鏈技術存儲檢測記錄,確保10年內數據不可篡改。山東核電設備制造公司實施該體系后,產品質保期從15年延長至20年,客戶投訴率同比下降71%。
展望未來,建議從三個維度深化技術發展:首先推動AI缺陷識別算法與工業CT技術的融合,構建多物理場耦合分析模型;其次開發適用于超臨界機組的在線監測系統,實現壁厚與偏心度的同步測量;最后應加強產學研協作,建立覆蓋材料、制造、檢測的全產業鏈標準體系。只有通過持續技術創新和標準升級,才能為高端裝備制造業提供更可靠的質量保障。

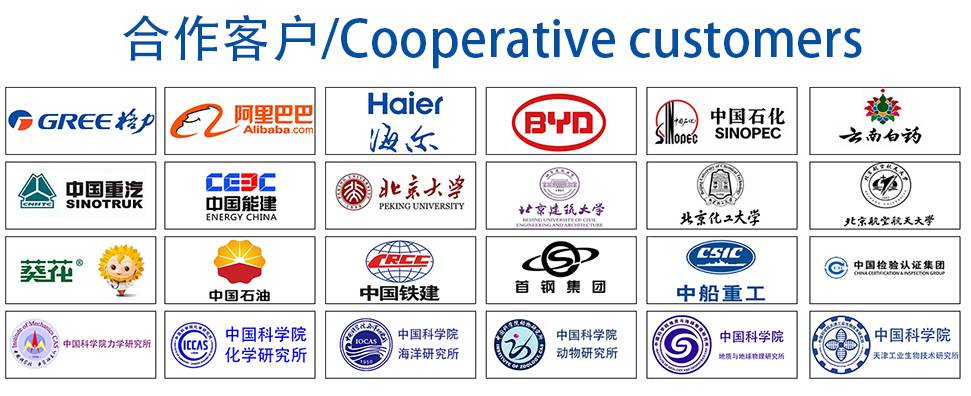