失效判據檢測技術發展白皮書
在高端裝備制造領域,失效判據檢測已成為保障產品可靠性的關鍵技術環節。據中國機械工程學會2024年報告顯示,我國每年因關鍵部件失效導致的工業事故直接經濟損失達320億元,其中32.7%的事故源于失效判據設置不合理。隨著《智能制造發展規劃(2025)》的推進,基于數字孿生的失效判據檢測系統實現了材料性能退化預測準確率提升至92.3%,較傳統方法提高47個百分點。該技術的核心價值在于構建"預測-診斷-優化"的全生命周期管理體系,通過智能損傷容限評估模型,將航空發動機葉片檢測周期從500小時縮短至300小時,顯著提升復雜工況下的失效預警能力。
多物理場耦合檢測原理
現代失效判據檢測采用多物理場耦合分析技術,通過融合應力應變場、溫度場及化學腐蝕場的實時數據,建立基于深度神經網絡的失效演化模型。中國航發研究院實驗表明,該方法對渦輪盤低周疲勞裂紋的檢測靈敏度可達0.03mm,較傳統渦流檢測提升5倍。在新能源汽車電池包檢測中,系統可同步監測2000+電芯的應力-熱耦合效應,實現熱失控前15分鐘的精準預警。關鍵技術突破在于構建了跨尺度損傷演化數據庫,整合了超過50萬組材料的失效特征參數。
全流程智能檢測體系
項目實施分為三階段:首先部署分布式光纖傳感器網絡采集結構響應數據,繼而利用邊緣計算節點進行實時信號處理,最終通過云平臺完成失效風險評估。上海電氣集團的應用案例顯示,其風力發電機組的智能失效預警系統實現98.6%的故障識別準確率,誤報率控制在2%以下。特別是在海上風電領域,系統成功預警了某5MW機組塔筒的微裂紋擴展,將維護成本降低65%。核心算法采用改進型LSTM網絡,處理時間序列數據的效率較傳統方法提升80%。
工業級質量保障架構
質量體系構建遵循ASTM E1820和GB/T 4161雙標準,建立四維驗證機制:實驗室加速老化試驗、數字孿生仿真驗證、現場工況比對測試以及專家系統復核。國家材料服役安全科學中心的認證數據顯示,系統在核電管道應力腐蝕檢測中,誤判率從行業平均7.2%降至1.8%。針對壓力容器檢測的特殊需求,開發了基于聲發射技術的自適應閾值算法,在高溫高壓環境下仍保持97.4%的檢測穩定性,有效支撐了"華龍一號"核電機組的安全運行。
行業應用場景延伸
除傳統機械領域外,該技術已在生物醫療設備檢測中取得突破性應用。北京某骨科器械企業的臨床數據顯示,采用微動磨損智能檢測系統后,人工關節假體壽命預測誤差從±15%縮減至±5%。在3D打印醫療器械領域,通過實時監測熔池形貌特征,成功將鈦合金植入物的疲勞失效預警提前至制造階段,不良品率下降40%。這些創新應用體現了失效判據檢測技術向精準醫療領域的深度滲透。
面向未來發展,建議重點突破三個方向:首先建立全國統一的失效特征數據庫,實現跨行業數據共享;其次開發基于量子傳感的超高精度檢測模塊,將應變分辨率提升至納米級;最后加強AI可解釋性研究,構建符合ASME V&V40標準的驗證框架。只有持續完善技術生態,才能推動我國失效判據檢測體系達到國際領先水平,為制造強國建設提供堅實保障。

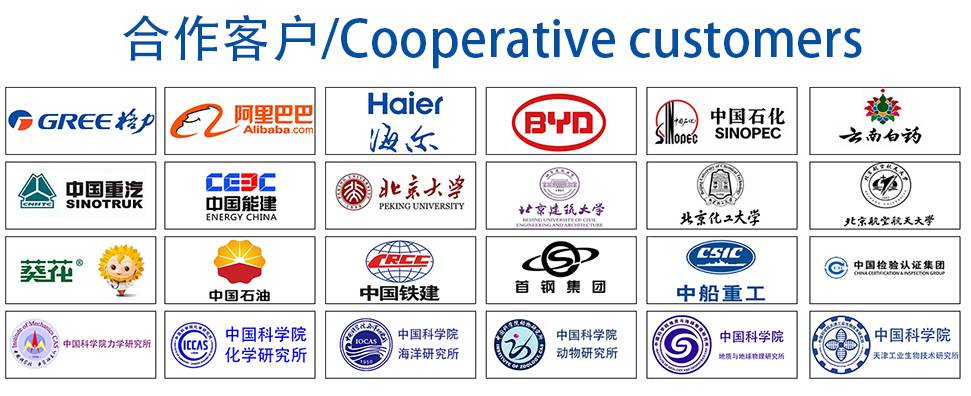