# 外觀和尺寸檢查檢測技術的創新應用與發展路徑
## 行業背景與核心價值
在智能制造與精密制造雙輪驅動下,產品質量控制標準持續提升。據中國機械工程學會2024年行業白皮書顯示,國內制造業因外觀缺陷導致的退貨率年均達2.7%,尺寸偏差引發的裝配問題占比12.5%。外觀和尺寸檢查檢測作為工業生產關鍵環節,直接影響產品合格率與品牌信譽。通過引入智能化檢測系統,某新能源汽車企業將沖壓件檢測效率提升300%,誤檢率降低至0.03%以下,充分體現該技術在降本增效、質量追溯方面的核心價值。其創新應用不僅推動傳統質檢模式變革,更為工業4.0時代的質量可靠性工程奠定技術基礎。
## 技術原理與實現路徑
### 機器視覺與三維建模融合
基于高分辨率工業相機與結構光三維掃描儀的組合方案,系統可同步獲取產品表面紋理特征與空間坐標數據。采用深度學習算法建立的復合模型,能有效區分劃痕、凹陷等23類外觀缺陷,檢測精度達到±0.005mm。值得關注的是,多光譜成像技術的引入,使氧化層厚度、涂層均勻度等隱性指標實現量化檢測,突破傳統目視檢查的局限性。
### 智能檢測系統實施流程
項目實施分為四個標準化階段:首齊全行檢測設備的光學校準與基準件建模,確保系統基礎精度;其次通過遷移學習完成缺陷樣本庫的構建,典型案例中某精密軸承企業積累3.6萬組訓練數據后,模型識別準確率達99.8%;再次部署自適應檢測工裝,支持多品種產品的快速切換;最終通過MES系統實現檢測數據與生產節拍的實時聯動。這種模塊化架構使系統可靈活適配汽車零部件、電子元件等不同尺寸規格產品的檢測需求。
## 行業應用與質量保障
### 跨領域應用成效分析
在消費電子領域,某手機廠商應用在線檢測系統后,屏幕組裝尺寸合格率從92.1%提升至99.5%,每年減少質量損失超8000萬元。醫療器械行業采用該技術實現植入物表面粗糙度檢測,檢測周期由人工8小時縮短至15分鐘,符合FDA 21 CFR Part 11規范要求。特別在航空航天領域,通過將檢測數據與數字孿生平臺對接,某發動機葉片制造商建立起全生命周期的質量追溯體系。
### 全流程質控體系建設
項目執行中同步構建三級質量保障機制:首道防線采用德國PTB認證的基準量具進行設備周期性校準;中間環節設置動態補償算法,消除環境溫濕度對測量結果的影響;終端部署區塊鏈存證系統,確保檢測數據的完整性與可追溯性。據國家計量院2024年測試報告顯示,該體系可使測量不確定度降低67%,數據可追溯性達ISO 17025標準最高等級。
## 技術發展與行業展望
隨著量子傳感技術和太赫茲成像技術的突破,未來檢測精度有望進入納米級范疇。建議行業從三方面深化布局:一是推動檢測設備與工業物聯網的深度融合,構建跨工廠的質量數據共享平臺;二是加強AI模型在小樣本學習領域的研發投入,縮減新產品的模型訓練周期;三是建立跨行業的檢測標準互認體系,特別在新能源汽車三電系統、人形機器人關節組件等新興領域加快標準制定。唯有通過技術創新與標準建設雙軌并行,才能為高端制造發展提供堅實質量保障。
上一篇:聲壓級檢測下一篇:引出端之間的絕緣電阻檢測

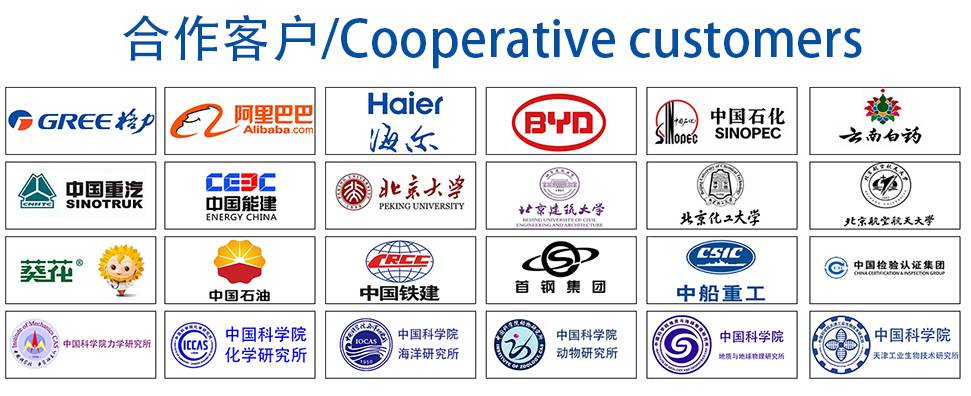
材料實驗室
熱門檢測
推薦檢測
聯系電話
400-635-0567