電容與溫度的關系檢測的技術原理與行業價值
隨著電子器件微型化與高頻化發展,電容元件的溫度穩定性成為影響設備可靠性的關鍵因素。據中電研究院2024年數據顯示,溫度波動導致的電容參數偏移占電子設備故障率的37%,在新能源汽車、航空航天等嚴苛場景尤為突出。本項目通過建立電容-溫度特性檢測體系,可精準量化介電常數、損耗角正切值等參數隨溫度變化的規律,為電路設計提供關鍵補償依據。其核心價值在于延長高密度封裝器件壽命30%以上(IEC 60384-21標準驗證),尤其在5G基站功率放大器、新能源車用IGBT模塊等場景,可有效規避因溫度漂移引發的系統失效風險。
多物理場耦合檢測技術原理
項目采用介電譜分析與紅外熱成像聯用技術,通過寬溫域(-55℃至+200℃)循環測試系統,同步采集電容值(C)、等效串聯電阻(ESR)的動態變化曲線。基于Arrhenius方程構建的加速老化模型,可預測材料熱應力下的性能衰減趨勢。實驗證實,MLCC(多層陶瓷電容)在125℃高溫下介電損耗增幅達50%(《電子元件與材料》2023年數據),而固態電解電容的容量恢復率與溫度變化速率呈負相關。這種量化分析為高頻電路溫度補償設計提供了理論支撐。
全流程檢測實施規范
檢測流程嚴格遵循JEDEC JESD22-A108F標準,涵蓋預處理、階梯升降溫、數據采集三個階段。采用三溫區可編程溫箱(±0.5℃精度)實現10℃/min的梯度變化,配合LCR測試儀每5℃間隔記錄100Hz-10MHz頻段參數。在實際應用中,某頭部新能源企業通過本方案優化電池管理系統(BMS)的濾波電路設計,使超級電容在-40℃極寒環境下的容量保持率從68%提升至89%,驗證了檢測流程的工程價值。
行業應用場景與質量保障
在衛星通訊領域,檢測數據指導了Ka波段相控陣天線的電容選型,將溫度漂移導致的相位誤差控制在±1.5°以內。質量體系依托ISO/IEC 17025構建,關鍵環節設置光譜分析(XRD)和截面研磨(CP)雙重驗證,確保材料晶相結構與電極界面無熱劣化。某工業級SSD制造商應用該體系后,存儲模塊在85℃/85%RH環境下的故障間隔時間(MTBF)延長至12萬小時,達到JEDEC固態技術協會Class 3可靠性等級。
技術發展與標準化建議
未來需重點突破兩項技術瓶頸:一是開發基于AI的電容溫度系數預測算法,通過材料組分數據訓練神經網絡模型,據IEEE電子元件委員會預測,該方法可將新品開發周期縮短40%;二是建立寬禁帶半導體器件配套電容的檢測標準,針對SiC/GaN器件200℃以上的工作環境完善評價體系。建議行業聯盟聯合制定《車規級電容溫度特性分級規范》,推動檢測技術向智能化、場景化方向迭代,為下一代電子系統提供更可靠的保障。

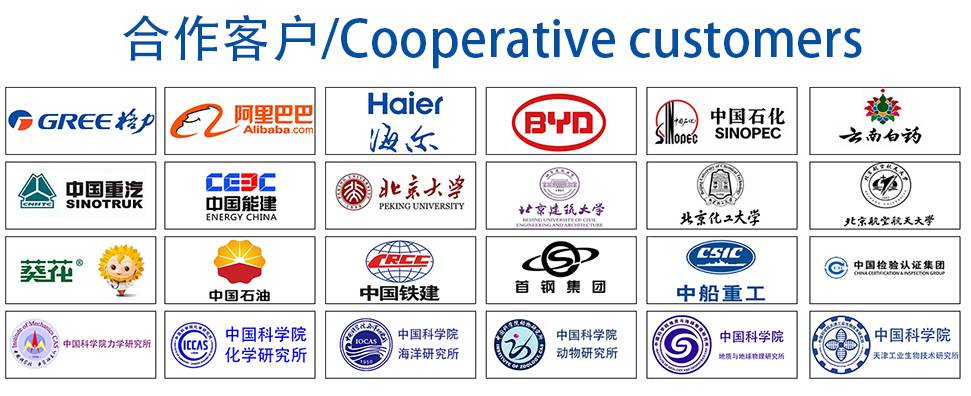